![]() |
Plant director Colin Mitchell welcomes guests to the official opening of the Hams Hall engine factory |
Speaking on Thursday before the official opening of the new four cylinder engine factory in Warwickshire, in the English Midlands, BMW AG board member Dr Norbert Reithofer said: “Our engine plants are not conceived as insular units within the BMW production system but are fully integrated within the network as a whole.”
Reithofer noted that BMW sold 822,000 cars in 2000 and expects further growth.
“This is precisely why we are enlarging our [car] production capacities both at our German plants and in Spartanburg, USA, in order to meet demand.”
He said Hams Hall, given the go-ahead in November 1996 when BMW still owned Rover and Land Rover in nearby Birmingham, was “the most modern engine production plant in the world” with £400 million invested.
“This year alone, some 60,000 engines will be coming off the production line in Hams Hall [and] will be supplied to BMW plants worldwide,” Reithofer said.
How well do you really know your competitors?
Access the most comprehensive Company Profiles on the market, powered by GlobalData. Save hours of research. Gain competitive edge.
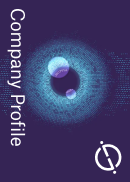
Thank you!
Your download email will arrive shortly
Not ready to buy yet? Download a free sample
We are confident about the unique quality of our Company Profiles. However, we want you to make the most beneficial decision for your business, so we offer a free sample that you can download by submitting the below form
By GlobalDataThe plant can build 400,000 engines annually.
![]() |
Engines nearing completion |
Reithofer noted that a data network gives the plant great flexibility with minimal parts stockholding. Hams Hall is linked to BMW’s engine development division in Munich, parts suppliers and the car assembly plants it supplies in Germany, the USA and South America.
However, a planned extension of the Channel Tunnel rail link to a freight depot close by the UK factory has not been built, forcing the plant to ship engines by road in what one insider described as “a problem, a logistical nightmare”.
The same source said that the plant will eventually have a “5000-engine pipeline” between it and the car assembly plants which means “that’s only a couple of days’ supply, it’s tight”.
The majority of engine parts used come from Germany, with the balance sourced from Great Britain, Austria and France.
![]() |
BMW chairman Joachim Milberg (right) and chief secretary to the UK Treasury Andrew Smith unveil one of the first engines produced at Hams Hall |
BMW has also developed specialist “centre of competence” parts factories so that, for example, camshafts assembled into engines at Hams Hall come from Berlin while connecting rods and cylinder block castings arrive from Steyr, Austria and Landshut, Germany, respectively.
As production of a new range of four-cylinder petrol engines, with unique infinitely variable inlet valve lift in place of a throttle butterfly, ramps up at Hams Hall, BMW will wind down production of the previous generation motors at Steyr, using the capacity to increase production of four- and six-cylinder diesel engines alongside six-cylinder petrol units.
“Close co-operation between our plants, an efficient transfer of know-how and a high standard of flexibility on the part of our associates are the primary features of this group-wide production network,” said Reithofer.
Flexible working time allows employees, called ‘associates’ at Hams Hall, to maintain ‘working time accounts’ of plus/minus 200 hours a year.
This is something BMW pioneered a decade ago with a new car assembly plant at Regensburg. It seems to have been accepted from the start at Hams Hall but BMW faced industrial action recently when introducing a similar system to the Cowley factory near Oxford that will soon start building the new Mini.
That car, strangely, will use engines produced in a joint venture with Chrysler in South America.
![]() |
Ready to ship to a car assembly plant |
“The individual locations of the BMW group co-operate in one global plant network,” Reithofer said.
“An ongoing exchange of knowledge and ideas within this network is indeed essential in order to handle the high standard of complexity we face in automobile production today.
“The flexibility of our associates, with more than 300 working time concepts, the exchange of knowledge and the flexible use of our plants help us to optimise our capacity.
“For this reason alone, our plants rank right at the top in terms of both quality and flexibility. And this will also be the case at Hams Hall,” Reithofer insisted.