GKN has unveiled two new constant velocity joint (CVJ) design technologies. Countertrack and Crosstrack are the first all-new design principles in CVJ applications in more than 70 years. Engineer Alfred Rzeppa patented the modern universal joint in 1934.
“We have now reached the limits of the Rzeppa principle” that all modern CVJs still work off, says Al Deane, engineering director, driveshafts at GKN.
New manufacturing processes and component improvements make the new GKN CVJs 30% more energy efficient. The two new designs are also lighter and smaller, and therefore offer greater power density. Power density is the torque capacity rating of a given diameter of CVJ.
Countertrack is applied to the fixed joints on the outboard end of sideshafts and propshafts. By using opposing tracks for the bearings in the joint to equalize the forces at work, the joint exhibits considerably less friction and heat-related energy loss. A further benefit is improved steering angle in the joint, meaning smaller turning circles. It is applicable to all front sideshafts on driven wheels. “The benefits of the principle are better at higher angles, which means the front axle for steering sideshafts,” says Rob Rickell, engineering director, sideshafts for GKN. Countertrack can also be used on all propshafts. In a typical midsize vehicle, countertrack CVJs are 8% smaller and 15% lighter than conventional joints.
Crosstrack applies to the plunging joints on the gearbox side of driveshafts. By using a combination of straight tracks and angled tracks for the bearings to run in, crosstrack offers “the best of both worlds, in terms of driveline ‘clunk’ and low plunge effort,” says Dan Booker, director, propshaft technology at GKN. Plunge effort is the force needed to plunge joint with torque applied. A high plunge effort results in a greater level of noise, vibration and harshness within the vehicle.
How well do you really know your competitors?
Access the most comprehensive Company Profiles on the market, powered by GlobalData. Save hours of research. Gain competitive edge.
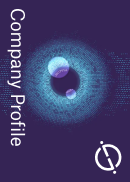
Thank you!
Your download email will arrive shortly
Not ready to buy yet? Download a free sample
We are confident about the unique quality of our Company Profiles. However, we want you to make the most beneficial decision for your business, so we offer a free sample that you can download by submitting the below form
By GlobalDataGKN’s product development system goes through four phases, A-D. In only 30 months, the new technologies have gone from initial concept, Phase A, to validated and industrialized prototypes – about halfway through Phase C.
Next year, countertrack will debut in the propshaft of an unnamed North American vehicle.
The European introduction of countertrack joints is expected in sideshafts for a front-wheel-drive car in 2007-8.
By 2010, GKN expects to be making around one million units annually says Deane. With GKN’s production of driveshafts running at about 95 million pieces per year, just over 1% will be based on the new design five years from now. “If within the next three to five years, we have launched five new applications across the board on mainstream launches, we would term that very successful,” says Deane.
As well as the planned production contracts, GKN is working on joint development programmes for countertrack with two OEMs in Japan and two more in Europe.
Crosstrack is a little further off, but GKN is working with a customer in North America on this technology too.
Countertrack is the leading technology because “customers bringing new vehicles through are much more conscious of weight and fuel economy than they have been before,” says Deane. GKN executives estimate that countertrack on a midsize front-wheel-drive car with a V6 engine would offer the end user around €200 fuel savings every year.
GKN’s designs offer “solutions to problems” such as the introduction of more powerful engines after the main launch of a vehicle. In such cases, OEMs need more powerful shafts and CVJs to handle the increased torque, but they don’t want to change any of the other components or geometries on the car underside. “We can offer 30% more torque in the same space, or the same torque for a smaller package,” says Rickell.
A step change in technology often heralds a wave of outsourcing, as OEMs choose to buy improved components from suppliers, rather than sink new capital of their own.
But labour issues and existing plant may be obstacles to outsourcing in this area. “So we’re willing to license our technology to help our customers,” says Deane.
Alex Graham