Further investment in the German motor industry should not be ruled out just yet, is the message BMW chairman Helmut Panke delivered at the official opening of the automaker’s new Leipzig plant in Saxony, eastern Germany on Friday, writes just-auto.com deputy editor Graeme Roberts.
“I would like to say quite pointedly: Germany still has the prerequisites to be successful in global competition,” Panke said.
“It is indisputable that, compared to other locations internationally, doing business in Germany entails high costs and, amongst other challenges, over-regulation.”
Panke added that automakers, and wider industry, were being harmed by “short-sighted and populist” reasonings sometimes reached for “careless, non-factual and sometimes incomprehensible motives”.
He called on German politicians to allow maximum flexibility in job and working conditions.
How well do you really know your competitors?
Access the most comprehensive Company Profiles on the market, powered by GlobalData. Save hours of research. Gain competitive edge.
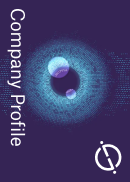
Thank you!
Your download email will arrive shortly
Not ready to buy yet? Download a free sample
We are confident about the unique quality of our Company Profiles. However, we want you to make the most beneficial decision for your business, so we offer a free sample that you can download by submitting the below form
By GlobalDataThe new Leipzig plant, which built its first saleable car on March 1, operates on a
“BMW Formula for Work Pact” that varies weekly operation from 60 to 140 hours. This “wider collective agreement” between the automaker and its labour “de-links” the personal working time of staff from the machine running time of the plant and can increase installed capacities by up to 40%.
“A great deal can be achieved right here in Germany when there is enough flexibility,” Panke said.
His comments come in a week when the European parliament began a process that could remove UK employers’ ability to negotiate an opt-out from the 48-hour maximum working week with employees. London is likely to enlist the support of eastern European countries, which have recently attracted jobs-rich vehicle and component plants, in beating back the latest proposal from Brussels.
In west Germany, collective work pacts mandate a 35-hour work week, while here in eastern Germany it is 38 hours.
BMW officials noted that their German plants in Dingolfing, opened in 1973 and Regensburg (1986) were each widely expected to be the last built in Germany at the time of opening, with the inauguration of Spartanburg in the USA apparently confirming that once and for all.
Panke noted: “Since the startup of our plant in Spartanburg, we have increased our US retail sales figures more than five times over.”
German-built models benefited, hence: “Our strong position abroad safeguards [and creates additional] jobs at home.”
He added that, though BMW sells 73% of its cars outside Germany, 75% of its staff work in the homeland and half its purchases – 50% of 15 billion euros – is spent there.
“This is far greater than the revenues we make in Germany.”
However, BMW officials frankly acknowledged that without about 350 million euros of European Union subsidy, the 1.3 billion euro Leipzig plant would not have been built. The site was chosen from an initial list of 250 locations and while not perfect in every respect it best met seven key BMW requirements overall.
Proximity to the automaker’s Bavarian plants and good links to suppliers in southern and central Germany also helped tilt the scales.
The plant has started life building 3-series sedans with four-cylinder petrol and diesel engines for European markets – including right-hand-drive UK-specification units – at the rate of 150-200 a day with around 2,500 workers (or associates as BMW calls them).
That will build to 650 a day with 5,000 employees on site and BMW expects a further 5,000 posts will be created in supporting industries such as components and logistics.
Despite prodding, no comparative figures were provided. Just-auto understands the workers here earn about 65% of the pay received by their western Germany counterparts (for 3 extra hours a week); on costs and productivity, the stock answer was effectively it’s too early to say; ask us again when we’re fully ramped up.
Plant employees come from a wide age range – the oldest is 61 – and some had previously been unemployed for extensive periods. Around 1,500 were trained in the west in a plant like Munich.
No pressing or engine building is done on site but 97% of body welding is robotic and the paint shop uses powder and water-based paints. Unique features of the stylish plant designed by London-based Iraqi architect Zaha Hadid include body-and white and painted body shells trundling through public and administrative areas on conveyors leading to high-rise buffer stores, and the patented ‘finger’ layout of the final assembly track.
Essentially, the less complex parts of the assembly line run down extendable corridors at right angles to the sections containing complex machinery, the sections in the finger can be lengthened in as little as a weekend at minimal cost as the expensive gear does not need to be shifted.
A few suppliers are already on site and a new line-sequenced supply centre will eventually deliver around 7,000 square metres of modules like seats and cockpits to the assembly track each day – about 70% of the plant’s delivery volume.