Volkswagen has achieved a 15% productivity improvement at four vehicle factories and one engine plant in three Brazilian states in the last 12 months.
It was accomplished by a productivity improvement process dubbed ‘PMP Wave’, intended to sharpen elements of the Volkswagen Production System.
The Brazilian VW subsidiary prefers not to comment but has admitted to technical support from Porsche Consulting.
German technicians from the Porsche subsidiary, from VW, and Brazilian VW workers have worked together to realise significant productivity gains.
“Our big challenge is to rank as one of the most profitable and flexible companies in the world”, said Volkswagen of Brazil head of operations Joerg Müller. He added that PMP Wave has already attracted the interest of other VW units in Germany, Argentina and Spain.
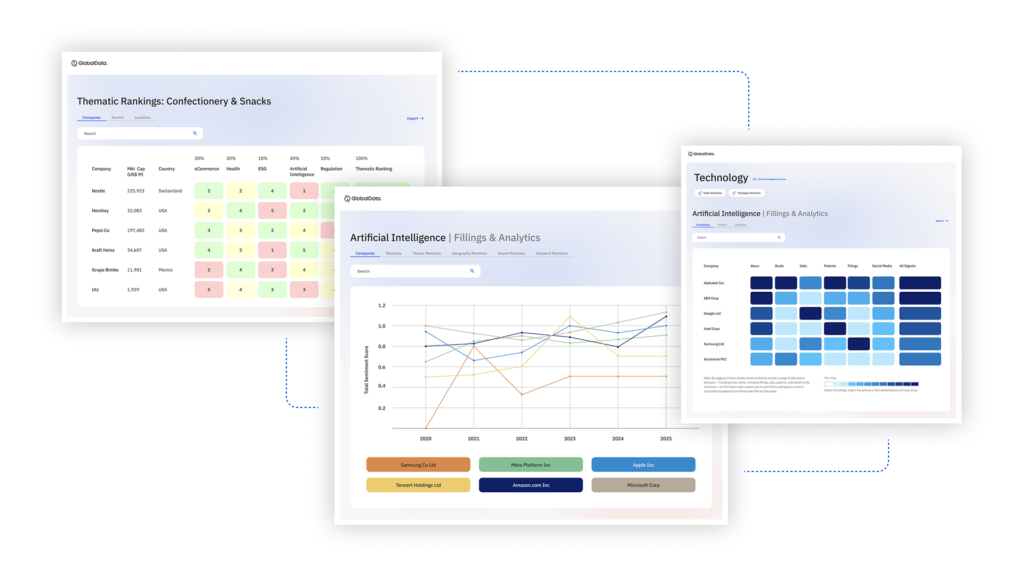
US Tariffs are shifting - will you react or anticipate?
Don’t let policy changes catch you off guard. Stay proactive with real-time data and expert analysis.
By GlobalDataOne of the most beneficial gains was through identifying and eliminating waste and operations that add no value. In one year, there was a reduction of 605 kilometres, or 739,444 footsteps, of unnecessary employee movement around production lines, effectively providing more work time.
The ergonomics of 196 operations were improved, 83 cases of excess production, 857 operations that required waiting and 156 rework tasks were eliminated.
In addition, 75 transport problems were solved, 170 unnecessary processes were eliminated and 91 failures attributed to faulty communications were identified. Other gains were made by making 234 layout changes in five manufacturing plants.
In all, the company managed last year to take 2,977 actions for productivity gain and waste elimination.
VW noted that standard employee suggestion programmes with financial rewards are too bureaucratic and require too much testing and evaluation time before ideas are eventually adopted.
Müller summarised the four principles of lean production: zero failure, by eliminating process failures; pulling principle, producing only what is needed; parts flow, to minimize inventory; and rhythm of production, synchronising all processes and cutting down intermediate inventory.
Fernando Calmon