Evonik has developed a PulPress method, allowing manufacturers to mass-produce complex moulded parts at what it says is “a reasonable price,” taking technology from the high-end market to large-scale production.
The new method combines two traditional production techniques: compression moulding and pultrusion. Combined together, they make automated, continuous production of composite parts possible.
The most important raw material in the process is Rohacell, a structural foam core from Evonik that retains its shape and is temperature resistant. Fibres are woven around the core before being impregnated with resin.
The complete system is then compressed into the desired shape at high temperature and pressure. The method allows manufacturers to produce complex geometries and integrate recessed areas for threaded components or other fixtures.
Aspects of the new manufacturing process include its design flexibility and cost efficiency and the crash behaviour of the resulting composite parts—parts that are around 75% lighter than traditional steel structures, maintains Evonik.
The supplier also says the PulPress method reduces costs by up to 60% compared to composite parts manufactured using established methods such as resin injection. “These advantages have already won over a large number of customers in the European automotive industry,” said Evonik Resource Efficiency Segment manager for new applications, Sivakumara Krishnamoorthy.
How well do you really know your competitors?
Access the most comprehensive Company Profiles on the market, powered by GlobalData. Save hours of research. Gain competitive edge.
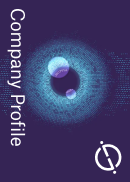
Thank you!
Your download email will arrive shortly
Not ready to buy yet? Download a free sample
We are confident about the unique quality of our Company Profiles. However, we want you to make the most beneficial decision for your business, so we offer a free sample that you can download by submitting the below form
By GlobalData“Moulded parts made using PulPress will soon be going into mass production.”
Data from just-auto’s QUBE service shows Evonik has 25 plants worldwide, employing 33,000 people.
Evonik is also focused on developing battery technology. Its CERIO technology is ceramic materials and ionic conductors to produce safer and smaller lithium ceramic batteries.