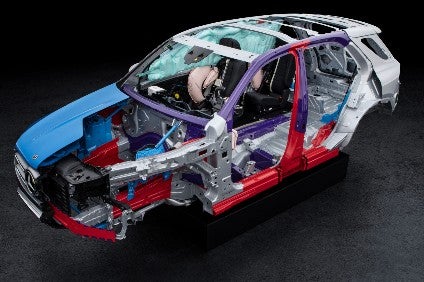
Daimler’s Mercedes-Benz is using organo panels in the main front end member of the redesigned, US-built GLE SUV, noting it’s the first time it has used this innovative material for such a large and visible component.
Organo panelling provides an alternative to sheet metal panels and consists of fibre-reinforced plastic panels. After heating in a press, these panels are formed into three-dimensional components via a process which involves very short cycle times.
The fibre reinforcement endows organo panels with very good mechanical properties, such as rigidity and strength, combined with only a fraction of the weight of their sheet metal counterparts.
The thermoplastic plastic matrix offers another advantage. An injection moulding process follows in a second, integrated production step, in the course of which ribs, mountings, and any other required items are added. This takes place in the same tool in which the organo panel was formed.
The organo panelling of the GLE can be permanently fused to adjacent parts made of polypropylene (PP). Only butt-welding was possible previously, with the risk of fractures. Use of the sandwich construction principle means that fewer components are needed overall, as air ducts and sleeves for bolt-on components are directly integrated. As organo panels do not corrode, they do not need to be painted.
The front end member made of organo panels is around 30% lighter than a conventional design, contributes to high torsional rigidity and improves crash performance, especially together with the crash boxes attached to it.
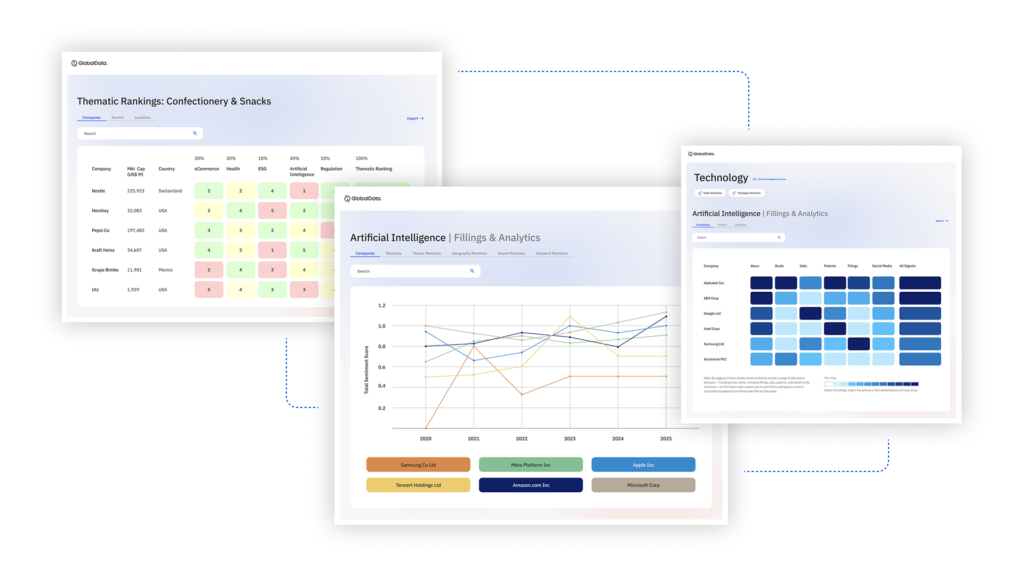
US Tariffs are shifting - will you react or anticipate?
Don’t let policy changes catch you off guard. Stay proactive with real-time data and expert analysis.
By GlobalData“This combines an innovative material with an integrated production process to produce an innovative component,” Daimler said.
The Society of Plastic Engineers recognised these merits by awarding the organo panelling first place in the Structural Components category at its 2018 Automotive Awards.