
Mercedes-Benz powertrain plants in Germany are starting production of key components for the battery-powered eActros heavy truck. They include the electric axle and battery packs which are produced and assembled in Gaggenau, Kassel and Mannheim.
The components will be used for eActros series production which will begin at Woerth on 7 October.
Yaris Pursun, head of global powertrain operations at Daimler Truck, said: “This is ushering in a new era for the production and technology network of our German powertrain plants.”
Battery packs from Mannheim
The Competence Centre for Emission-free Mobility (KEM) in Mannheim assembles individual battery modules into complete packs, which are then subjected to a function test. A battery pack consists of six individual battery modules and a completely assembled pack is almost 2.2 metres long, 75 cm wide and 55 cm high. Before the modules become part of an operational pack, they are first installed into a metal housing and then connected to other components such as busbars, control systems and wires. They are then wired to the high-voltage cable sets, after which insulation layers are applied. In the final step, the electric/electronic box (E/E box) is attached to the pre-assembled metal housing, which will later form the interface between the battery and the vehicle. The E/E box is also pre-assembled at Mannheim. After a final function and leakage test of the entire battery pack, the component is shipped to Woerth.
Electric axle from Kassel
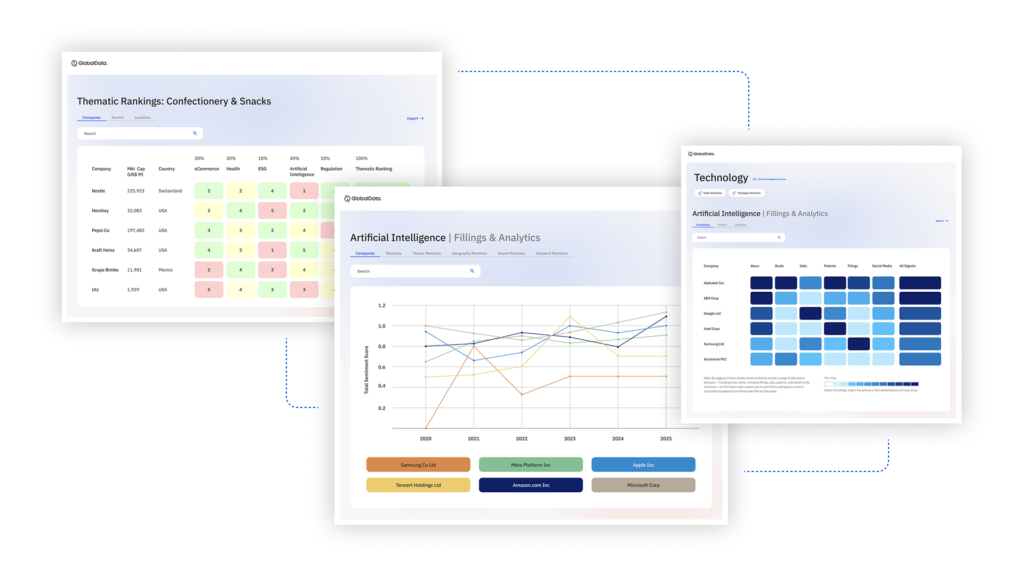
US Tariffs are shifting - will you react or anticipate?
Don’t let policy changes catch you off guard. Stay proactive with real-time data and expert analysis.
By GlobalDataKassel assembles the complete electric axle, consisting of the axle bridge, the electric motor and the shiftable transmission elements. The core axle is pre-assembled first. The drive unit, including the two-speed transmission, is pre-assembled in parallel. Gaggenau supplies the transmission components for this step. After the core axle is pre-assembled, the entire drive unit, including the two-stage transmission, is attached to the axle. Before the electric axle is prepared for shipment, it is subjected to a function and high-voltage test to check electrical safety and noise properties.
The electric axle is mounted on the same basis as its conventional counterpart. As a result, it is possible to integrate the manufacturing and assembly processes of the electric axle into existing production lines in parallel with the conventional production series. This makes the production process extremely flexible and cost efficient. During the integration of the electric axle, the main focus was on the commissioning of machines that were either adapted to the production of electric axles or newly purchased for them. This equipment includes machines for the pre-assembly of the drive unit, the final assembly of the electric axle and the entire test procedure.
Transmission-related components from Gaggenau
Gaggenau produces transmission-related mechanical components and the associated housings. The components produced range from a tiny planetary gear with an outside diameter of 57mm to a drive wheel with an outside diameter of 365mm and a raw component weight of over 40 kg. Ten transmission parts and three housings are supplied to Kassel for assembly of the electric axle.