
A EUR15m logistics improvement project at Daimler’s Kecskemét, Hungary factory is progressing well after construction started earlier this year, Daimler said.
The plant’s logistics hall is being expanded considerably to supply parts directly to the production line. A new shopping cart-based logistics system has brought clearly visible changes to the plant’s assembly area as there are now no shelves filled with boxes and parts anywhere on the production line.
The automaker said associated logistical supply processes have changed “almost beyond recognition” because previous transport routes have been freed up and driverless transport systems automatically take the carts from the picking zone in the logistics centre to the assembly line.
Employees receive the parts they need a specific work station ready for almost immediate installion in vehicles. Load carriers previously required in the production area are no longer necessary.
The space freed up by the removal of shelf stacks is being used for ergonomically designed break time areas for the line workers.
Construction work commenced earlier this year and is completion scheduled for the summer.
How well do you really know your competitors?
Access the most comprehensive Company Profiles on the market, powered by GlobalData. Save hours of research. Gain competitive edge.
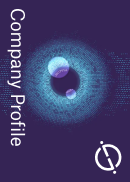
Thank you!
Your download email will arrive shortly
Not ready to buy yet? Download a free sample
We are confident about the unique quality of our Company Profiles. However, we want you to make the most beneficial decision for your business, so we offer a free sample that you can download by submitting the below form
By GlobalDataThe Kecskemét plant is is part of the Mercedes-Benz Cars compact car production network. Lead plant is Rastatt (Germany) and vehicles are also made at BBAC in Beijing, China. Contract assembler Valmet Automotive builds additional A-class models.
The shared compact car architecture enables each location to build any and all models in any sequence and any volume ensuring production can be distributed across the network flexibly and efficiently to meet current market demand.
Last year, Kecskemét produced over 183,000 cars.