Continuing its dramatic overhaul of business practice, Ford has launched an initiative to reduce losses due to absenteeism in its Cologne factory. The move highlights Ford’s newfound obsession with the details of its production and supply processes. By identifying many small inefficiencies and addressing them on a case-by-case basis, Ford hopes to make big savings.
Ford, which last year made a group-wide loss of $US5.45 billion, has cut employee absenteeism due to injury at its Cologne factory by 20% compared to this time last year. Part of the solution has been the removal of forklift trucks from the factory floor, eliminating injuries and sick leave caused by collisions with factory staff.
The move is one of many such initiatives that are part of Ford’s five-year cost-cutting program, which has so far netted the manufacturer savings of around $1.2 billion.
Since 2000, the company has focused on developing a flexible manufacturing system as well as new products. It has also reduced the number of its production facilities in Europe from 11 to 6, shedding 30,000 workers in the process.
In Europe, the company is attempting to reach 100% capacity utilisation in its production capabilities by next year. At present, it effectively uses 93% of its production capacity, up from 71% in 2000.
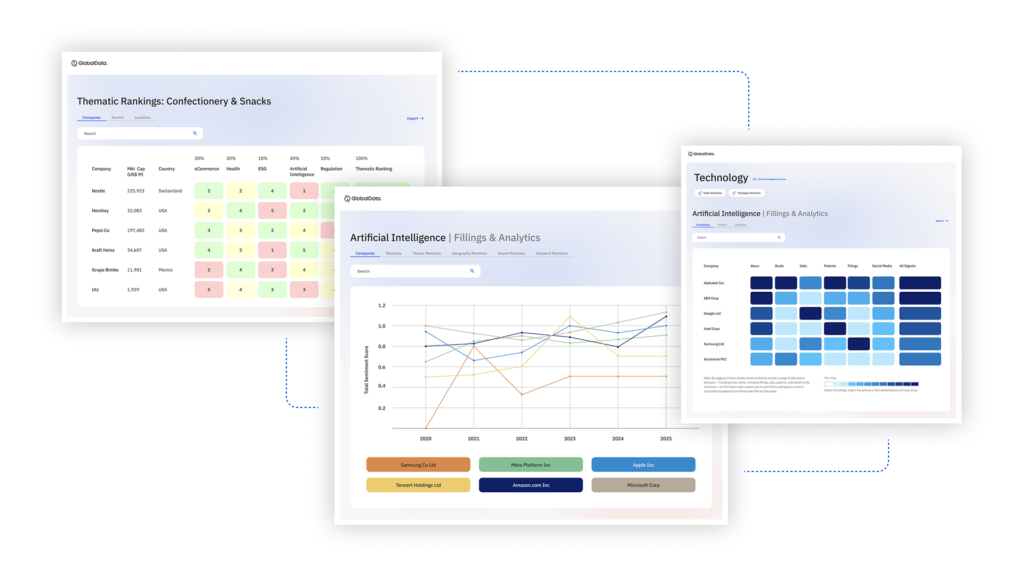
US Tariffs are shifting - will you react or anticipate?
Don’t let policy changes catch you off guard. Stay proactive with real-time data and expert analysis.
By GlobalDataIn addition, Ford has cut the number of parts suppliers to 140, a reduction of 200 compared to two years ago. This has been possible due to identifying overlap in the supply chain, and by reducing the number of suppliers who supply the same type of component.
Ford is also expanding its Team Value Management (TVM) strategy, which it has used to some success in North America. TVM, which employs detailed analysis of materials and parts prices, has been credited with cost savings of between 10% and 15% and has allowed the company to negotiate better prices with suppliers.
Ford’s latest move demonstrates a growing appreciation that further savings can only come through a painstaking process of identifying small inefficiencies that might easily otherwise be overlooked. It is an imaginative initiative, and one that can only help as Ford attempts to return to profitability.