The BMW Group is expanding production capacity and increasing its staff at the Competence Centre for E-Drive Production in Dingolfing faster than originally planned.
Due to growing demand for electrified vehicles, the plant expects the number of modules needed for production of high-voltage batteries to double from the previous year. The number of electric motors required will also increase significantly.
Michael Nikolaides, head of Production Engines and E-Drives at the BMW Group: “We are embarking on a massive expansion of our Competence Centre for E-Drive Production in Dingolfing: from 8,000 square metres currently to 80,000 in the future. This is where we produce powertrain components for our fully and partially electric models. By the end of the year, we will increase our staff in this area from 600 to more than 1,400.” Up to 2,000 employees will work on electric motors, battery modules and high-voltage batteries in Dingolfing in the medium term.
Christoph Schröder, head of BMW Group Plant Dingolfing, adds: “Thanks to close cooperation between vehicle and component development, our Dingolfing site is now leading the transformation of the automotive industry. More than one in five BMW 5 Series Sedans built at our Dingolfing vehicle plant today is already a plug-in hybrid. We deliver premium e-mobility from Lower Bavaria to customers all over the world.”
800 new jobs in electric component production – specialists needed
For the upcoming ramp-up and planned volume growth, qualified staff are currently being recruited on a large scale – both internally at the BMW Group’s plant locations and outside the company. As Nikolaides points out: “We are also combing the market for specialists for the future technology of e-mobility.”
How well do you really know your competitors?
Access the most comprehensive Company Profiles on the market, powered by GlobalData. Save hours of research. Gain competitive edge.
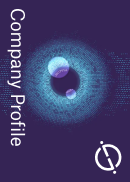
Thank you!
Your download email will arrive shortly
Not ready to buy yet? Download a free sample
We are confident about the unique quality of our Company Profiles. However, we want you to make the most beneficial decision for your business, so we offer a free sample that you can download by submitting the below form
By GlobalDataBroad electrified vehicle line-up creates stronger demand for electric powertrain components
The introduction of the new BMW 330e*, BMW X5 xDrive45e* and BMW X3 xDrive30e* plug-in hybrids, together with the pure electric MINI Cooper SE*, brings the number of electrified vehicles in the BMW Group line-up to 12. These will be joined in 2020 by additional electrified models, such as the BMW X1 plug-in hybrid and the fully-electric BMW iX3.
The BMW Group plans to expand its range of electrified vehicles to 25 models by 2023 – more than half of them fully electric. A quarter of the BMW Group vehicles sold in Europe are likely to be electrified by 2021; this percentage will reach a third in 2025 and half in 2030.
As a result, the company has a correspondingly high demand for electric motors and batteries. BMW Group Plant Dingolfing plays a pivotal role in supplying other sites with these electric powertrain components. “We don’t just supply the vehicle plant here in Dingolfing; we also delivery batteries and electric motors to most of our automotive plants worldwide,” says Nikolaides.
Preparations for production of fifth-generation electric powertrain components well underway
The site in Lower Bavaria has years of expertise in building components for electric vehicles. Series-produced batteries for the BMW i3 have being coming off the line here since 2013. Since then, products and processes have been continuously optimised.
Preparations are already underway for production of the fifth generation of electric motors and batteries. Production is slated to start later this year and will set new standards for scalability and performance capabilities.
Important infrastructure decisions are also being made in parallel. In the areas around Dingolfing, the search is underway for a site to locate a new supply centre for the Competence Centre for E-Drive Production. This would be built over the next few years and serve as a “logistics platform” for the competence centre once it reaches its full capacity.