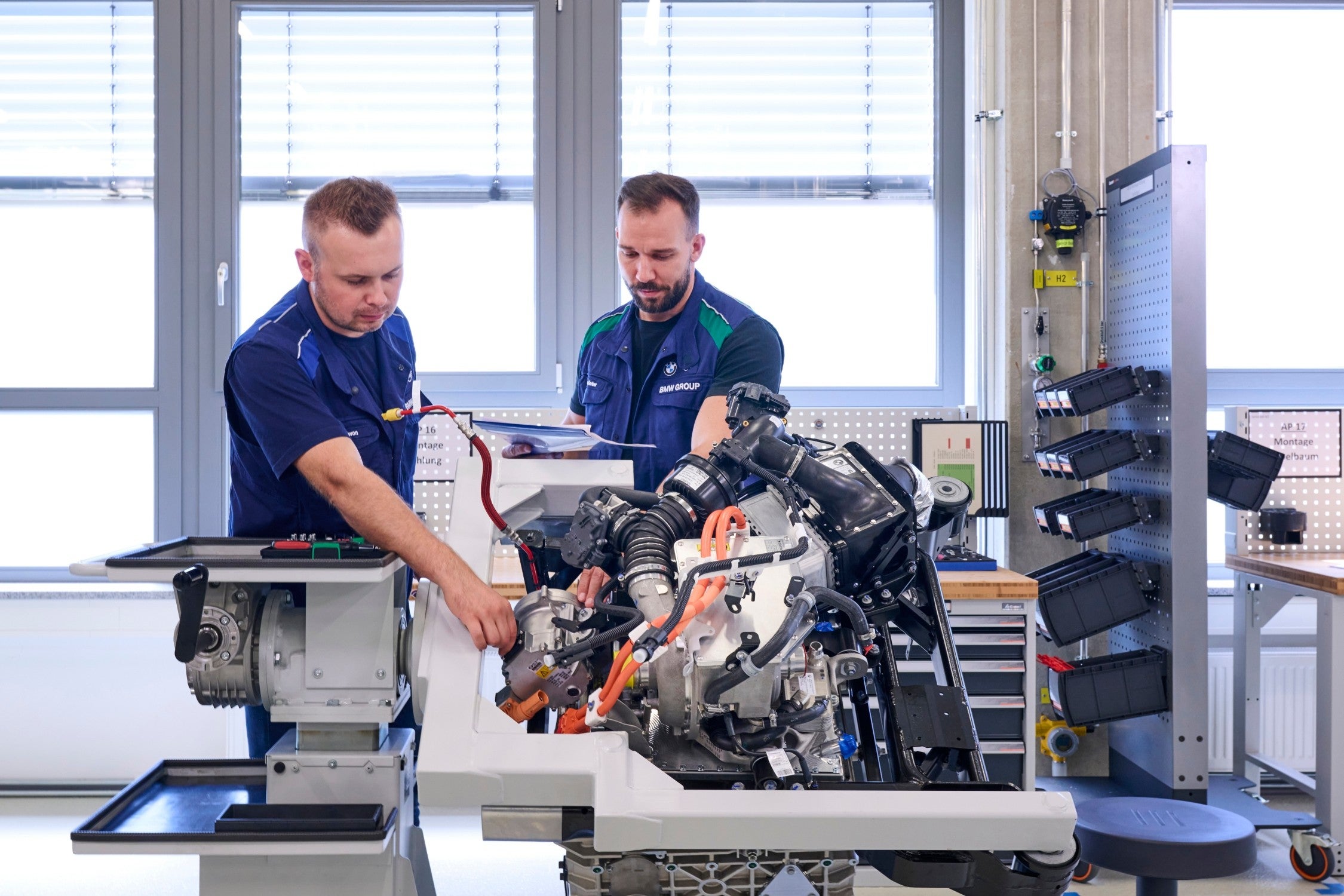
BMW has begun fuel cell system production in Munich. A small series of iX5 hydrogen cars will enter service worldwide from the end of this year for test and demonstration purposes.
“We think hydrogen powered vehicles are ideally placed technologically to fit alongside battery electric vehicles and complete the electric mobility picture,” said chairman Oliver Zipse. “By commencing small scale production of fuel cells today, we are demonstrating the technical maturity of this type of drive system and underscoring its potential for the future.”
Development chief Frank Weber added: “We have managed to more than double the fuel cell’s continuous output in the second generation fuel cell while weight and size have both decreased drastically.”
The system generates a high continuous output of 125 kW/170 hp and powers an electric motor and a high-performance battery purpose developed for this vehicle to enable the powertrain to deliver 275 kW/374 hp. The drive system comprises two hydrogen tanks, the fuel cell and the electric motor.
BMW Group sources the individual fuel cells from Toyota.
Fuel cell systems are manufactured in two main steps. The individual fuel cells are first assembled into a fuel cell stack. The next step involves fitting all the other components to produce a complete fuel cell system.
How well do you really know your competitors?
Access the most comprehensive Company Profiles on the market, powered by GlobalData. Save hours of research. Gain competitive edge.
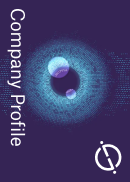
Thank you!
Your download email will arrive shortly
Not ready to buy yet? Download a free sample
We are confident about the unique quality of our Company Profiles. However, we want you to make the most beneficial decision for your business, so we offer a free sample that you can download by submitting the below form
By GlobalDataStacking of the fuel cells is a fully automated process. Once the individual components have been inspected for any damage, the stack is compressed by machine with a force of five tonnes and placed in a housing. The stack housing is manufactured in the light metal foundry at Landshut using a sand casting technique.
The pressure plate, which delivers hydrogen and oxygen to the fuel cell stack, is made from cast plastic parts and light-alloy castings, also from Landshut. The pressure plate forms a gas- and water tight seal around the stack housing.
Final assembly of the fuel cell stacks includes a voltage test along with extensive testing of the chemical reaction within the cells. Finally, all the different components are fitted together in the assembly area to produce the complete system. During this system assembly stage, further components are fitted, such as the compressor, the anode and cathode, the high-voltage coolant pump and the wiring harness.