
BMW has confirmed its Mini factory at Cowley, near Oxford in England, will assemble the electric Mini.
The electric drivetrain will be made in Germany. The first all-electric variant will be the three-door hatchback, known as the Hardtop in the US.
The development is part of BMW’s latest electrification strategy, also announced on Tuesday (25 July).
“Electrification is one of the central pillars of the BMW Group’s corporate strategy Number One > Next and the company has announced that all brands and model series can be electrified, with a full-electric or plug-in hybrid drivetrain being offered in addition to the combustion engine option,” the automaker said.
“Additional electrified models will be brought to market in the coming years and beyond 2020, the company’s next generation vehicle architecture will be structured in order to enable new models also to be offered as a full electric vehicle.”
The battery-electric Mini will go into production in 2019. The Mini hatchback line currently offers petrol and diesel engines, as does the larger Countryman series to which a plug-in hybrid variant was added recently.
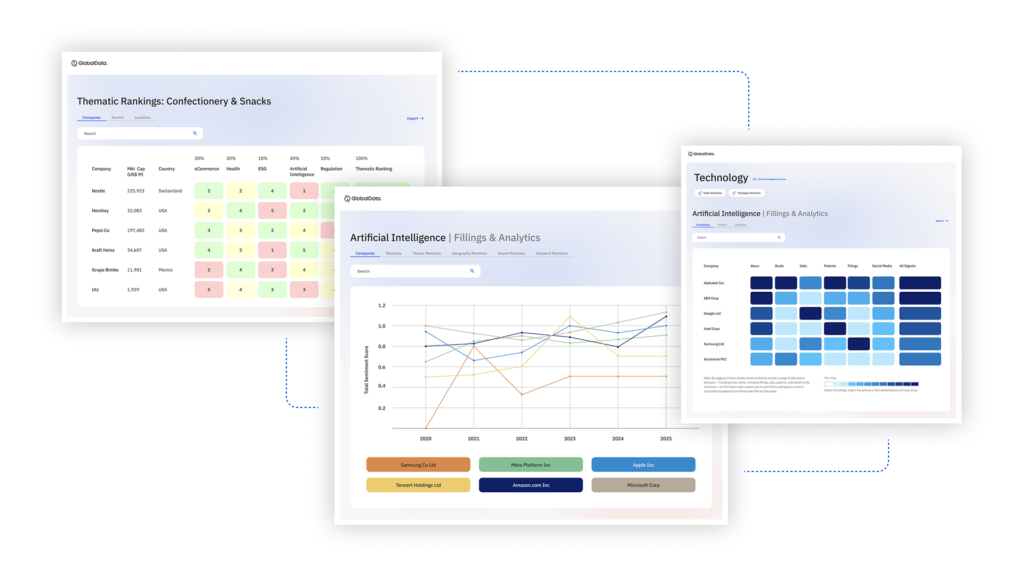
US Tariffs are shifting - will you react or anticipate?
Don’t let policy changes catch you off guard. Stay proactive with real-time data and expert analysis.
By GlobalDataThe hatch’s electric drivetrain will be built at group’s e-mobility centre at Plants Dingolfing and Landshut in Bavaria before being shipped to Oxford.
Oliver Zipse, BMW’s production chief, said: “[Dingolfing and Landshut] play a leading role within our global production network as the company’s global competence centre for electric mobility. Our adaptable production system is innovative and able to react rapidly to changing customer demand. If required, we can increase production of electric drivetrain motor components quickly and efficiently, in line with market developments.”
By 2025, the BMW Group expects electrified vehicles to account for between 15-25% of sales. However, factors such as regulation, incentives and charging infrastructure will play a major role in determining the scale of electrification from market to market. In order to react to customer demand, the group has developed a claimed “uniquely flexible system” across its global production network.
This will create structures that enable factories to build models with a combustion engine, plug-in hybrid or fully electric drive train at the same time.
The group currently produces electrified models at 10 plants worldwide; since 2013, most electric drivetrain parts for these vehicles have come from Dingolfing and Landshut. Dingolfing also builds the 5 and 7 Series PHEVs and from 2021, will add the i Next.
BMW said it had spent EUR100m on electro-mobility at Dingolfing so far with further investment continuing.
BMW will add an electric i8 Roadster to its model line in 2018. The electric X3 has already been announced for 2020 while the iNext is due in 2021.
The group claims to offer the widest range of electrified vehicles with nine already on sale.
The company has committed to selling 100,000 electrified vehicles in 2017 and expects 200,000 on the roads by the end of the year.
Its first large scale electric vehicle trial began worldwide in 2008 with the Mini E.
Learnings from this project (particularly in regard to ‘range anxiety’, according to company sources) guided subsequent development of the Leipzig-made i3 and i8 and subsequent PHEV variants of other models.
See also: Despite Brexit, business case strong for BMW’s UK Mini investment – ANALYSIS