
Production of the new BMW 7 Series has begun this week at the BMW Group Dingolfing plant in Germany.
“The BMW 7 Series has defined our identity at this site for over 40 years. We are proud that BMW’s top model, the new BMW 7 Series Sedan, will also be built here in Dingolfing. Our goal as the brand’s primary plant for the luxury class is to ensure that every vehicle our experienced and competent team puts on the roads guarantees excellent quality,” says Ilka Horstmeier, director of BMW Group Plant Dingolfing.
The so-called “digital launch” presented a particular challenge for the production start, BMW said. The company claims it means production of a new vehicle is ramped up to the full daily volume from one day to the next. To ensure high quality standards are fulfilled from the very first vehicle, complex components underwent virtual testing for fit accuracy prior to the start of production.
Since production of the first 7 Series began in 1977, more than 1.9m BMW 7 Series cars have been built in Dingolfing. The BMW 7 Series is the number-one export from the plant in Lower Bavaria. Last year, over 90% of all units produced were exported abroad. The Chinese market plays an especially important role for the model: In 2018, 44% of global sales were delivered to customers in China.
The BMW 7 Series will continue to be available in two body variants, including the Long Wheelbase version with its 14-cm-longer wheelbase. Some 80% of customers – especially in China – opt for this version, which offers more space in the rear.
Six-cylinder plug-in hybrid debuts
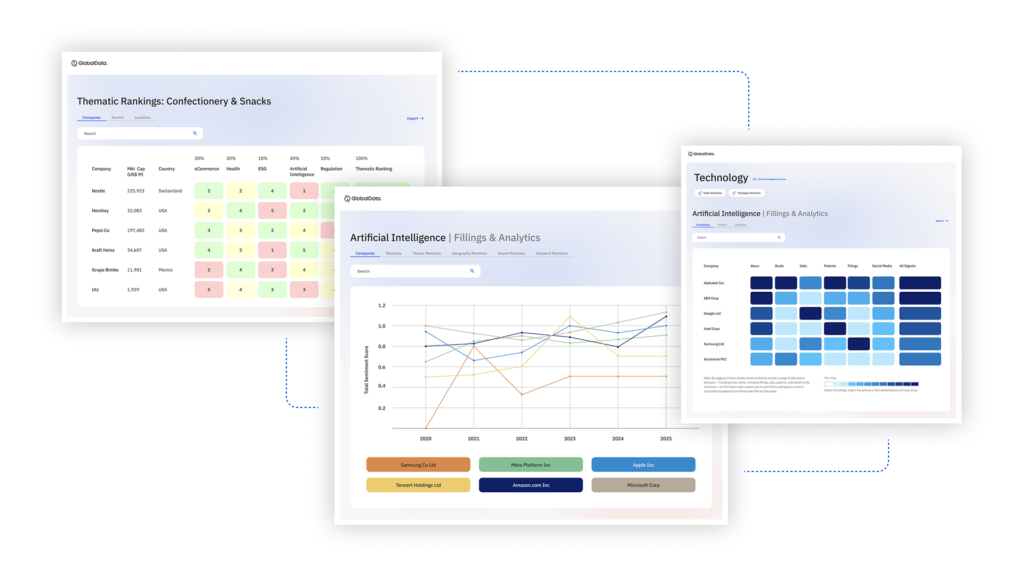
US Tariffs are shifting - will you react or anticipate?
Don’t let policy changes catch you off guard. Stay proactive with real-time data and expert analysis.
By GlobalDataFor the first time in a BMW Group vehicle, a plug-in hybrid will be available with a six-cylinder engine. In the BMW 745e / 745Le (combined fuel consumption: 2.3 – 2.1 l/100 km / 2.3 – 2.2 l/100 km; combined power consumption: 15.6 – 15.1 kWh/100 km / 15.7 – 15.6 kWh/100 km; combined CO2 emissions from fuel: 2 – 48 g/km / 53 – 50 g/km), a 286 horsepower six-cylinder inline engine is combined with a 113 horsepower electric engine, for a total system output of 394 horsepower. The new BMW 7 Series is the first BMW Group vehicle with a fourth-generation battery. The latest battery-cell technology gives the luxury sedan an all-electric driving range of up to 58 kilometres, ensures local emission-free driving and is virtually silent. The battery installed in the BMW 745e / 745Le is manufactured in Dingolfing, just a few kilometres away, at the Competence Centre for e-drive Production (component plant 02.20).
From there, Dingolfing already supplies BMW Group vehicle plants worldwide with batteries and electric engines for production of electrified vehicles.
Digitalisation supports BMW 7 Series production process
The production process for Dingolfing’s top model is ‘supported by a range of innovative solutions’, BMW maintains. For assembly of less-ordered special equipment, like the rear centre console, the vibrating alarm of a smartwatch alerts employees on the corresponding section of the line that an “exotic” is coming up and gives them instructions for additional work steps.
Data glasses are also used in training new staff. When learning new work steps, virtual assistance is projected into the employee’s field of vision. This enables rapid, sustainable learning in pre-assembly of complex components like the rear light. This augmented-reality application is used at assembly training centres and constantly refined in agile working methods in close cooperation between production planning and IT.
Digitalisation is also making further inroads in supplying assembly lines with components. The latest generation of autonomous tugger trains is currently being piloted on longer routes between the warehouse and assembly hall. The capabilities of driverless tugger trains go beyond automation of earlier solutions. New and smarter logistics helpers will enable dynamic route guidance according to delivery priority, with active obstacle avoidance.
See also:
Revised BMW 7 Series makes world premiere in China
BMW launches new 7 Series PHEVs
BMW to add 2,000 more jobs at Dingolfing plant