Preparations and construction of BASF battery materials plants in Europe are advancing as planned, the supplier said.
After laying the foundation for its precursor cathode active material (PCAM) plant in Harjavalta, Finland, BASF officially started construction.
It also received construction permits to begin building a cathode active material (CAM) plant in Schwarzheide, Germany.
"Despite the ongoing COVID-19 pandemic, the multi-step investment project is progressing as scheduled for a 2022 startup," the company said in a statement.
"BASF remains steadfast in its commitment to provide a reliable and sustainable local supply to cell producers and OEM customers in Europe."
The new plants are part of the company goal to be "the leading global supplier of high energy density CAM for the automotive industry".
How well do you really know your competitors?
Access the most comprehensive Company Profiles on the market, powered by GlobalData. Save hours of research. Gain competitive edge.
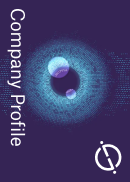
Thank you!
Your download email will arrive shortly
Not ready to buy yet? Download a free sample
We are confident about the unique quality of our Company Profiles. However, we want you to make the most beneficial decision for your business, so we offer a free sample that you can download by submitting the below form
By GlobalDataInitial factory capacity will enable the supply of battery materials for 400,000 full electric vehicles per year.
Peter Schuhmacher, president, catalysts division, said "Through regional production in combination with renewable energy sources as well as use of energy efficient and proprietary process technologies in our new plants in Europe, we are able to reduce CO2 footprint significantly – by around 30% compared with conventional industry standard."