Volvo Trucks is testing self-driving FMX trucks in regular operations in the Boliden mine in Kristineberg, Sweden. The aim is to examine how this technology can contribute to safe and productive transport in tough geographically limited application areas.
“Through our cooperation with Boliden, the development of autonomous vehicles is entering an exciting new phase. This is the first time ever that self-driving trucks are being tested in regular operations underground, and the results will provide valuable input to our ongoing mission to transform technical breakthroughs into practical customer benefits,” said Volvo trucks president Claes Nilsson.
Volvo trucks pulled the wraps off its autonomous FMX earlier this year and it attracted considerable interest in the industry. The research and development project of which this truck is a part reveals that self-driving trucks may offer a significant contribution to increased transport efficiency and productivity, in particular in mines, ports and other geographically limited and well-controlled environments with a large proportion of repetitive driving.
Tests 1,000 metres underground
The first autonomous FMX will become operational in the mine this autumn and, over the coming year, the operation will gradually increase to include another three.
System based on standard components
How well do you really know your competitors?
Access the most comprehensive Company Profiles on the market, powered by GlobalData. Save hours of research. Gain competitive edge.
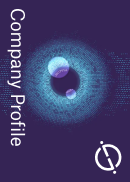
Thank you!
Your download email will arrive shortly
Not ready to buy yet? Download a free sample
We are confident about the unique quality of our Company Profiles. However, we want you to make the most beneficial decision for your business, so we offer a free sample that you can download by submitting the below form
By GlobalDataThe vehicles used in the mine are series-built FMX equipped with new functionality. Among other things, they include a system incorporating radar/laser-based sensors. This system is initially used to monitor the mine’s geometry and to generate a map of the route that the truck has to traverse. The collected information is then used to regulate the vehicle’s steering, gear changes and speed. On every new trip, the sensors are used to continuously scan the area around the truck and further optimise both the operation and the route.
Optimised logistics for better productivity
The technology used in the autonomous trucks makes it possible to optimise logistics in the mine in an entirely different way than at present. The trucks can operate continuously and, thanks to precise route planning and steady speed, there is no congestion and it is possible to cut loading and unloading times. During blasting operations drivers usually must wait until the mine gallery has been ventilated before the ore can be loaded but with self-driving trucks there are no such restrictions. All this means that each truck can be utilised more efficiently and can carry out more transport assignments per shift. The vehicles become an integrated part of the mine’s overall production system. Smoother transport flow and steadier speeds are also accompanied by lower fuel consumption and less wear and tear.
Safety top priority
An autonomous truck must be at least as safe and reliable as a manually driven truck. If an obstacle appears near the truck, the vehicle stops automatically and the transport management centre is alerted. Of the six sensors included in the system, there are always two that monitor the same part of the truck’s surroundings. If a fault occurs with the truck, it can be remotely operated from the transport management centre.
“Self-driving trucks may gradually become an important complement in mining operations, for instance, but for transport operations on public roads the driver will continue to play the major role,” Volvo Trucks said in a statement.