
By early 2023, the BMW Group will have a digital scan of every one of its vehicle plants worldwide. In this way, the company says it is systematically merging the real and virtual worlds and tapping into the enormous potential for highly efficient planning of future plant structures and production facilities.
Alongside data science and artificial intelligence, virtual planning is described by BMW as a core element of digitalisation within the strategic vision of BMW production: the BMW iFACTORY.
The aim is to make planning and simulation of all processes and the entire production system 100 percent virtual. Virtualisation takes planning for all processes to a new level, by enabling collaboration in real time between different locations and across different time zones.
“This opens up entirely new possibilities for us to implement both extensive new planning and smaller-scale remodelling of existing structures in a highly efficient, precise and flexible manner,” says Michele Melchiorre, head of Production System, Planning, Tool Shop, Plant Construction at the BMW Group.
“Production planning can integrate the virtual product into the virtual factory at an early stage. This reduces planning effort and capital expenditure and, at the same time, ensures processes are more efficient and more stable during ramp-up,” he says.
For completely new future production structures, the BMW Group will rely on cooperation with NVIDIA and its Omniverse software platform. “We are entering a new dimension of factory planning,” says Melchiorre.
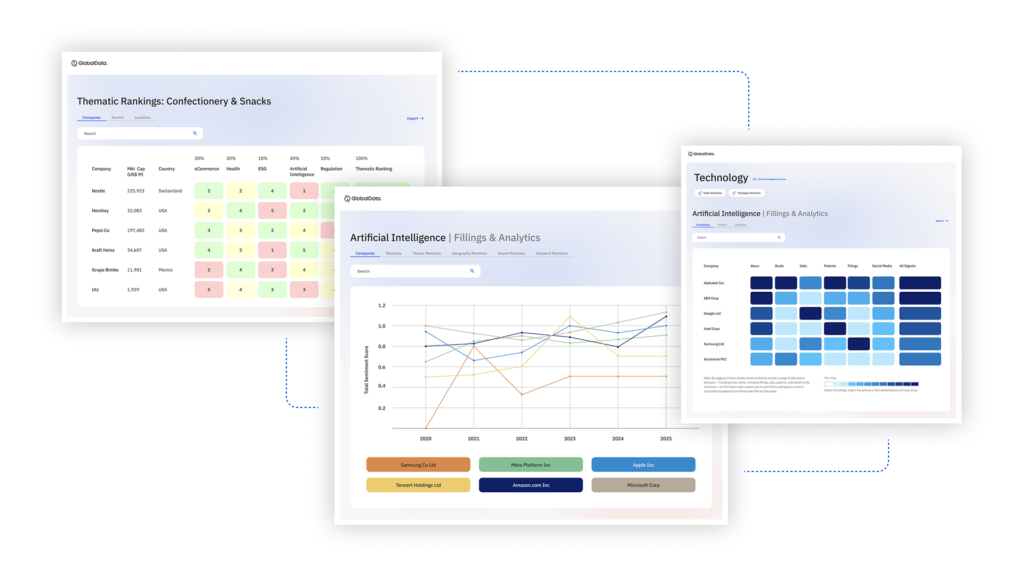
US Tariffs are shifting - will you react or anticipate?
Don’t let policy changes catch you off guard. Stay proactive with real-time data and expert analysis.
By GlobalDataThe digital twin means planners can conduct a virtual walk-through of BMW Group plants at any time, from anywhere. They can also develop production systems together in the simulated world, compare best practices and share information quickly and easily within the network. “This forms the basis for planning and developing our new vehicle plant in Debrecen in Hungary,” adds Melchiorre. “Today, around three years before the series launch, we are already able to simulate core processes at our future plant virtually.”
The BMW Group is digitalising its existing plants in cooperation with NavVis. The Munich startup is a provider of technology in the field of reality capture and digital twins. Mobile 3D laser scanners will be used to create photorealistic panoramic images, floor plans and scatter plots for all BMW Group vehicle plants, by early 2023, that are accurate down to the last detail, including all building structures, facilities and outdoor areas.
Since November 2020, around four million square metres of indoor space and nine million square metres of outdoor space at BMW Group plants have been scanned using portable mobile scanning systems and drone systems. As a result, digital twins are already available for the US plant in Spartanburg, the main plant in Munich and Plant Regensburg. Plants Dingolfing, Leipzig and Tiexi in China will also be captured by September of this year. By spring of 2023, digital data will also be available for the BMW Group plants in Mexico, South Africa, the UK and Dadong, China. The NavVis IVION Enterprise platform will then create a digital image of reality – the Digital Twin – from these huge data volumes.
Around 15,000 BMW employees are already working with this data, using a cloud- and web-browser-based software called the BMW Factory Viewer. With the help of this software and with just a few clicks, existing plants can be virtually inspected, specific points in production found via points of interest (POIs) and highly precise measurements carried out.
The system also allows individual sections of the 3D scans to be cut out and made available to external suppliers. BMW says this saves time and effort during production planning, improves collaboration with internal and external interfaces and eliminates planning errors.
3D scanning technology also allows both smaller and larger-scale remodelling projects at BMW plants to be transferred quickly and easily to the digital world, using the so-called re-scan process. The company is working in this area on developing its own autonomous scanning robots to keep the digital master data current in the long term, without requiring additional personnel effort. For this purpose, the BMW Group is using in-house solutions, such as the Smart Transport Robot (STR) developed by BMW Group subsidiary IDEALWORKS.