Advanced surface treatment specialist Zircotec, formerly formally part of the UK’s Atomic Energy Association, offers a wide selection of coating services to protect components against the effects of heat, wear, abrasion and oxidation. Matthew Beecham talked to Terry Graham, managing director of Zircotec about the ways in which the company is increasing its activity in the automotive market.
Originally developed by the British government laboratory at Harwell for the nuclear energy industry, Zircotec’s coatings allow engineers to optimise material performance in a range of demanding applications. The technology is being increasingly used by OEMs to solve heat issues in automotive applications. Later this year, the company will launch a new range that will offer vehicle designers and engineers novel finishes for thermal barrier and other applications.
just-auto: How did Zircotec enter the automotive market?
Terry Graham: “Zircotec’s automotive business has evolved from the activities of the former Race Engineering Division of AEA Technology plc. The technology was first applied to the exhaust of a rally Subaru to reduce cabin temperatures. The success in controlling temperatures led to the technology being used on a variety of applications including exhaust systems, turbo housings, gearbox covers, and engine components. Depending on the application, this brings a wide range of benefits including increased durability, protecting nearby components from heat, reducing cockpit temperatures and improving engine performance.”
just-auto: What is driving OEMs to use thermal barriers such as Zircotec?
Terry Graham: “OEM package engineers are finding it harder to package an increasing number of components under the bonnet. Traffic conditions and increased combustion also lead to higher underbonnet temperatures. The heat has to be removed. Zircotec is maintenance-free and is less than 500 microns thick so it has minimal impact on package space. In fact, in some instances it is possible to remove existing heatshields which reduces complexity and weight. For example, on Koenigsegg’s CCX supercar, the engineers decided that exhaust wrap was infeasible and also unsightly so they approached us to achieve a robust and effective solution that satisfies rigorous OEM quality standards.”
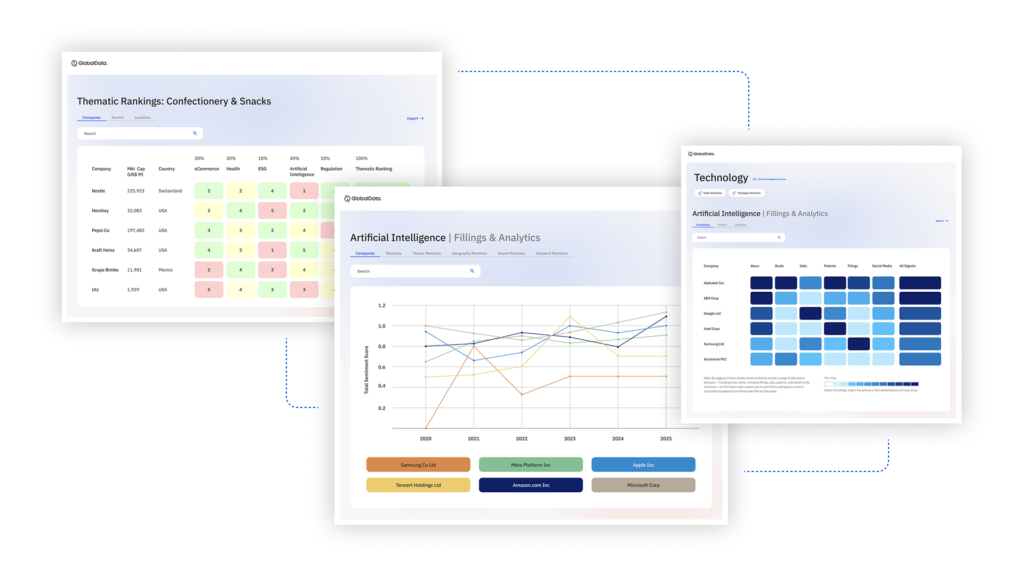
US Tariffs are shifting - will you react or anticipate?
Don’t let policy changes catch you off guard. Stay proactive with real-time data and expert analysis.
By GlobalDatajust-auto: Have you been able to quantify the heat reduction for OEMs?
Terry Graham: “This has been the key to gaining interest from the OEMs. We have recently released independent test data proving that the surface temperature can be reduced by 173ºC, that’s a 30% reduction on the V8 test engine manifold coated. Without this data and the accelerated lifetime testing that showed how effective the coating was against thermal shock, salt test and temperature cycling, it would have taken longer to gain a foothold in the market.”
just-auto: Does the coating offer any other benefits?
Terry Graham: “Our product is popular in the aftermarket and tuning sector. Keeping the exhaust gases hot is very relevant to turbocharged cars where the use of the coating makes the turbo spool up quicker, reducing turbo-lag and increasing responsiveness. This is a simple way to improve performance and driver enjoyment. Also, the bond coat is Nickel so we increase the anti-corrosive properties of metal.”
just-auto: Why should OEMs consider this technology instead of wraps or heatshields?
Terry Graham: “Wraps just aren’t durable over extended periods. With engine dressing also an area of focus we can offer a solution that keeps parts looking good over extended periods, including those that experience heat cycling. If heatshields are deleted, then we could offer a lighter solution and one that is less complex to assemble on a production line.”
just-auto: Is all your manufacturing done in house?
Terry Graham: “Currently yes, but should volumes increase we would consider licensing some of the technology to an exhaust manufacturer or appropriate tier one supplier. We have recently expanded capacity and robotised much of the spraying process to improve efficiency, but for very high volumes we would be open to work with partners.”
just-auto: Are there other applications that could be relevant to the technology?
Terry Graham: “The technology is suited to exhaust gas recycling [EGR] components in commercial vehicles to help vehicle and engine manufacturers achieve more stringent emission standards. Zircotec’s coating retains high exhaust gas temperatures which reduces warm-up times for after treatment systems, eliminating the need for close coupling and allowing more consistent control of exhaust gas temperatures. The same could be applied to catalysts to improve light-off time. Outside of automotive, we are working on some military and aerospace applications where again there is an increasing desire to effectively manage heat.”
just-auto: Is there ongoing development of the technology?
Terry Graham: “Zircotec is launching is a new range of coating finishes, the result of many months of research and development. These new coatings will offer innovative surface treatments and colours which can be tuned to the application. We will be able to adjust wear resistance, thermal barrier performance, colours and surface finish. These could be used for novel surface finishes on exterior or interior trim.”