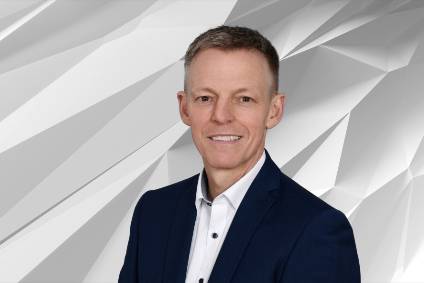
As the auto industry shifts from ICE power to EVs, manufacturers face opportunities and challenges on a number of levels. To learn more about the ins and outs, and how existing vehicle production lines can be adapted to suit, we spoke to Joerg Reger of robotics and automation specialist ABB.
How does the move to EVs affect manufacturing plants?
The obvious difference is the switch from IC engines to electric motors but there are a host of related changes that affect vehicle architecture and assembly. EVs have battery packs but no fuel tank; there is no intake or exhaust; an EV typically has no conventional transmission. These differences affect not only the assembly procedures and factory footprint but can also change the preferred supply arrangements, for example, whereas an IC engine plant could supply multiple vehicle plants, battery packs may be too large and too heavily integrated into the chassis for this to be practical.
Do any of the manufacturing changes have relevance for vehicles with ICE powertrains?
Oh yes. To reduce the high purchase price of current EVs, manufacturers are devising new and imaginative ways to cut costs throughout the vehicle, such as increasing the use of cast components and reducing pressing and welding operations or reducing painting costs through automated systems such as our PixelPaint process. Some are also automating what were traditionally highly manual activities, such as final assembly and trim, through automation. Typically, one automated cell can replace five manual stations, reducing factory footprint and freeing space for other purposes. In most cases, these developments carry back to ICE vehicle assembly just as effectively.
Is it better to start with a greenfield site for EV manufacture than convert an existing plant?
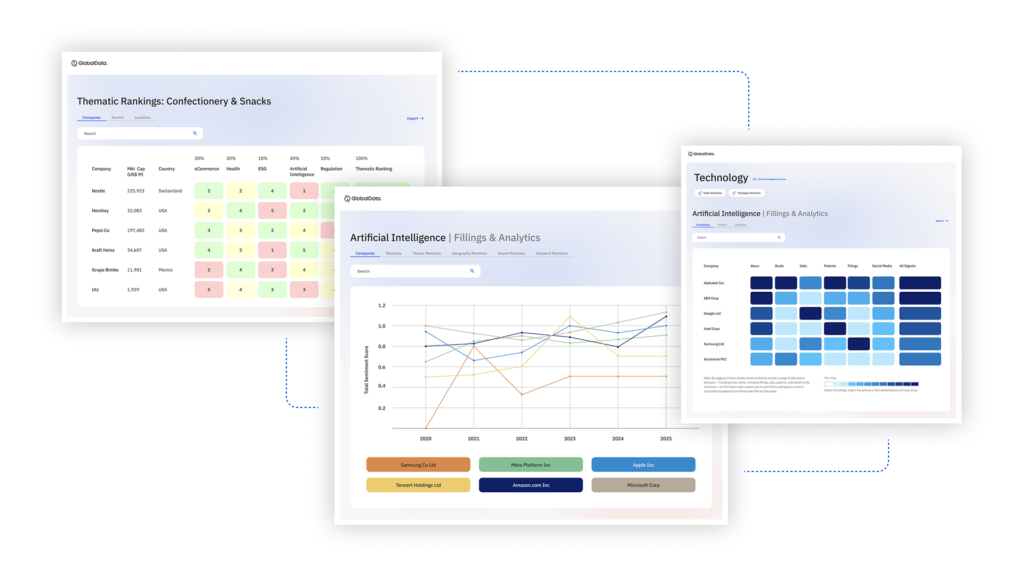
US Tariffs are shifting - will you react or anticipate?
Don’t let policy changes catch you off guard. Stay proactive with real-time data and expert analysis.
By GlobalDataGreenfield sites allow greater scope for optimization with fewer constraints, which is especially important for the logistics of parts supply into the plant when, for example, hybrids, battery EVs and ICE vehicles are assembled in the same facility. They do, however, require a major investment in new plant and infrastructure, and bring the challenge of the re-location of key suppliers and skilled workers.
With brownfield sites, the situation is reversed; much of the legacy investment in facilities can be retained provided any compromise to assembly efficiency is minimized. Existing suppliers and labour skills in the immediate vicinity are already available, assuming they remain relevant to the powertrain technologies employed.
EV technology is constantly changing, how do automakers future proof their facilities?
Ensuring the facility is flexible may be the difference between staying in business or not. Technology is changing so fast that the best solution today may not be the ideal one for the future. Product mix must vary to meet consumer demand, which is liable to change unpredictably, responding to developments in EV range, battery costs, government legislation and purchase incentives.
Even fundamentals like battery technology are changing rapidly. For example, current battery packs are assembled from modules, which themselves contain multiple cells. Manufacturers are divided over whether or not to buy in cells or modules from suppliers. Future batteries are expected to evolve from being replaceable items to becoming sealed for life, just as happened with smartphones. As cell-to-pack technology becomes established, modules will no longer be required, reducing cost and accelerating the move towards battery assembly in-house, within the vehicle assembly plant.
The industry is seeking 'zero loss' re-tools, whereby a line can be re-tooled for a model change without any loss of production.
So a truly flexible facility can accommodate not only changes in volume and product mix but also changes in operations and sequence, as new propulsion technologies emerge that affect the design of the vehicle. Conventional 'long line' assembly lines are badly disrupted by such changes. The industry is seeking 'zero loss' re-tools, whereby a line can be re-tooled for a model change without any loss of production.
How can such a level of flexibility be built into any manufacturing facility, while remaining efficient?
Automated cells using robots can offer the flexibility required if they are carefully designed. Having optimized the efficiency and manufacturing quality of the first cell, additional cells can be added in parallel to reliably increase production capacity. As EVs are frequently manufactured in small volumes initially, ramping up production rates by this approach is a very effective means to expand without any disruption to existing production.
Equally, when demand reduces for a particular variant of a vehicle, some cells can be re-purposed without affecting the others, enabling the switch to production of more popular products. This approach provides consistent product quality and maximum facility utilization yet accommodates the most challenging fluctuations in the product mix.
The pace of change in electrified powertrains is relentless. How is this affecting manufacturing?
The evolution of EV technology is so rapid that today's optimum powertrain may become uncompetitive within just a year or two. The manufacturing solutions chosen for that powertrain may have to be re-visited as the vehicles themselves are re-designed. Fundamental decisions, such as 'kitting' assemblies at suppliers or completing them in-house may be reversed.
To help manufacturers cope with the continual reduction in new product lead times, at ABB we make extensive use of 'digital twins' of our manufacturing cells. This means we simulate every aspect of their operation in a virtual environment, to validate the consistency and quality of their output. This accelerates the process of calibrating a new facility, shortens the commissioning time and allows the customer to bring their product on stream quickly and seamlessly. In the past, automakers endeavoured to get it 'right first time'; nowadays, they have to be 'right first time' and 'fast to market' as well. In becoming their production partner, we believe we're helping them to do just that.