
Lightweighting remains the holy grail of the automotive industry. Legacy materials such as high strength steels, aluminium alloys and carbon fibre all have their limitations and despite the promises made of hybrid composite metals, they haven't yet managed to break into the mainstream. But perhaps that is all about to change. Recent breakthroughs in aluminium matrix composites (AMCs), coupled with a real push from the industry to reduce weight, especially in electric vehicles, could see the potential for this family of materials to finally be relevant and crucially, viable for automotive uses. That's according to Richard Thompson, commercial director at AMC manufacturer, Alvant, who claims AMCs could hold particular relevance to electric vehicle (EV) manufacturers.
What are AMCs and what are their benefits over the legacy materials currently in use?
AMCs are an advanced class of metal matrix composites in which the aluminium is reinforced with high-performance ceramics. Made from a combination of aluminium alloy mixed with particles or long or short fibres, AMCs are stronger than steel and less than half the weight, up to 50 per cent stiffer and almost 300 per cent stronger than carbon fibre. Capable of withstanding severe damage, AMCs are suitable for applications where conventional metals are expected to approach or exceed their performance limits.
But haven't we heard about metal matrix composites before? What has changed since they were promoted as a major step in lightweighting 30 years ago?
There has been a huge amount of R&D into the manufacturing of MMCs, which has resulted in game-changing progress.
When Metal Matrix Composites (MMCs) first entered the market in the 1980s – primarily for use in automotive components – their properties were largely unproven and sometimes over-sold. Therefore, their reputation suffered, and manufacturers turned to carbon composite. Since then, there has been a huge amount of research and development into the manufacturing of MMCs, which has resulted in game-changing progress. We are now receiving several serious enquiries for projects with OEMs. That has been a big shift in the last 12 months as we have started to reveal the progress Alvant has made with AMCs both on technology and the cost side.
It sounds as though the technical challenges have been overcome but what about the cost element?
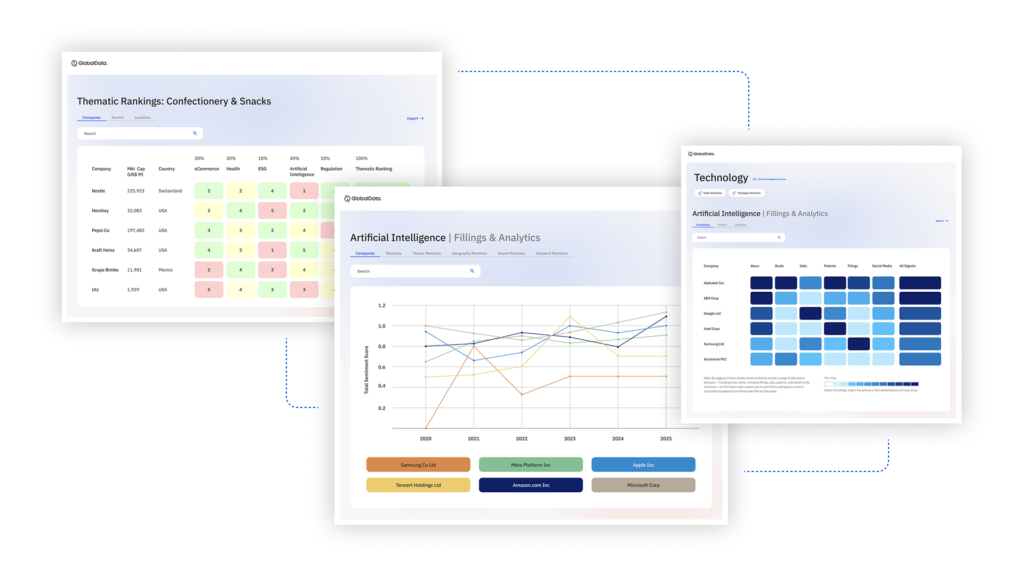
US Tariffs are shifting - will you react or anticipate?
Don’t let policy changes catch you off guard. Stay proactive with real-time data and expert analysis.
By GlobalDataCrucially we have made progress there. For cost-sensitive applications such as automotive, we are now capable of precisely tailoring for stiffness, strength, density as well as thermal and electrical properties. Let me give you an example. It's now possible to selectively reinforce areas of a mechanical component such as in body-in-white component. Alternatively, AMCs can be cost-effectively applied as a separate and discrete insert into a component, meaning you only need it in the zones where the gains are needed. That has opened up the applications where we can now compete.
What sectors or applications are the most relevant?
AMCs can play a role to help engineers achieve their targets. From body-in-white structures through to engine components, there are lots of applications that we can see would benefit. But the biggest interest is in applications for EVs and it's these OEMs that need the weight savings that we can offer.
In the automotive industry, electric vehicles are typically 125 per cent heavier than their combustion engine variant. A six per cent weight reduction in a typical electric vehicle chassis can equate to ~3km increase in range. Also, by increasing range capacity, carmakers are given the option of reducing the battery size, while maintaining range. So, a smaller battery could lead to a ~£300 reduction in battery production costs and ~£450 per annum reduction in ownership costs.
We understand that you have worked on using the materials in motors. What are the benefits to using AMCs for this application?
Yes, we have been working on a number of motor applications including radial flux electric motors and generators. We have demonstrated that weight reduction and increase in strength and stiffness can unlock performance in motors for automotive applications. Rotor speed can be increased which, in turn, increases power density by a massive 225 to 300 per cent (a factor of two to three) as well as reducing mass and inertia.
We found that if the rotors in axial flux motors were made from AMCs rather than steel, mass and inertia would be reduced by between 45 to 73 per cent and overall motor weight could be reduced by 19kg to 25kg.
Independent research commissioned by Alvant, found that if the rotors in axial flux motors (AFMs), the type suitable for passenger cars applications, were made from AMCs rather than steel, mass and inertia would be reduced by between 45 to 73 per cent and overall motor weight could be reduced by 19kg to 25kg.
During simulated tests, we also saw transient response improve when typical torque available at 8,000 rpm was applied to the rotor. Due to the higher specific strength and stiffness of AMCs, as well as their high damage tolerance, speeds of 15,000 rpm would, we think, also be reliably sustainable.
Those gains appear significant. Can you be more precise on those figures?
Of course, the precise extent of the weight savings depends on the three common types of axial flux motor used. In AFMs with electrical steel cores, the weight saving would be 45 per cent per motor; in AFMs with soft magnetic cores the saving is 50 per cent; and in AFMs with a Halbach Array the saving is 73 per cent.
What are the benefits for AMC applications in body-in-white (BiW)?
BiW constitutes around 27 per cent of a car's total kerb weight. OEMs are searching for a holy grail material which offers high tensile strength and stiffness as well as being lightweight and highly resistant to damage. Due to environmental concerns, it is also now expected to be recyclable, something that pure composites struggle with.
AMCs offer all these benefits and the stiffness makes them ideal not just for increasing structural integrity but also for reducing noise vibration and harshness. Being highly tolerant to abrasion and ballistic impacts also means greater safety and lower repair costs. Chassis legs, sill and cross car beams are good potential applications and we've also looked at even simpler applications such as hinges for a bonnet.
Are you also looking beyond the automotive industry?
Yes, we are already involved in several projects in aircraft from airframe and engine components through to creating lighter landing gear assemblies. We also believe there is great potential for other rotational components, such as wind turbines, where manufacturers are looking for efficiency gains, rotational dynamics and ways to lower the inertia of components, just as we have demonstrated in EVs.