Jim Queen is in charge of global vehicle engineering at General Motors. Dave Leggett recently talked to him about the challenges facing GM, it’s global vehicle engineering process and the Chevrolet Volt plug-in.
DL: What do you see as the biggest engineering challenges facing GM currently?
JQ: Right now the issue of energy diversity and how we’re going to provide – in this environment – the kind of vehicles that people want and be able to make a profit along the way.
There’s a lack of harmonisation of standards around the world which is a huge issue for every manufacturer. But the whole energy diversity issue is a huge technical opportunity for us – very, very challenging. It’s complicated by the lack of harmony from a regulatory standpoint around the world.
A year ago I may not have said that, but very clearly the world is converging on a real heightened sensitivity and whether you describe it as energy diversity or care for the environment, it’s going to be a huge technical challenge.
DL: Are you seeing much progress on this harmonisation issue?
How well do you really know your competitors?
Access the most comprehensive Company Profiles on the market, powered by GlobalData. Save hours of research. Gain competitive edge.
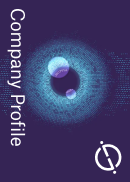
Thank you!
Your download email will arrive shortly
Not ready to buy yet? Download a free sample
We are confident about the unique quality of our Company Profiles. However, we want you to make the most beneficial decision for your business, so we offer a free sample that you can download by submitting the below form
By GlobalDataJQ: For regulatory issues already on the books, it’s not going to happen. Pedestrian protection is an example where getting ahead of that we were able to evolve with different agencies and governments around the world to a global standard. There was an interest in getting the initial standard a bit more stringent and in that process the industry, governments etc converged on a global pedestrian impact standard which is good.
Moving forward there’s opportunity, but there’s so much on the books right now, in the safety area, different frontal impacts, different energies required that it would be very difficult to converge on things that are already on the books. Moving forward I think there’s at least an awareness that convergence would be a good thing. Whether that view prevails or not is another issue, but a good example is, as I say, pedestrian protection.
DL: Can you explain the basics of how GM’s global vehicle development programme works – I’m thinking in terms of what vehicle programmes are assigned where?
JQ: We have these things called ‘Architectural Development Teams’ and over the period of the last couple of years, we have assigned a particular physical location, which invariably is one of our engineering centres, as the centroid of all of our technical activity around a particular architecture, on behalf of General Motors.
I want to compare and contrast that with the way some manufacturers are still doing this and the way General Motors did this previously in a project centre kind of environment, where each of the user regions of North America wanted to use a compact vehicle. They would each send their own representation into a project centre kind of environment and then we’d all try and impose our will or preferences and try and come to a solution.
That’s very, very difficult – command and control is lousy and invariably you walk away from the project centre environment and I describe it as the vehicles start walking away from the common opportunity millimetre by millimetre, just because you can, you’ve got different suppliers etcetera.
So we failed in that regard in the 1990s and now I have, in each of these Architectural Development Teams, what I call a Global Vehicle Chief Engineer for General Motors. They are responsible for all of the vehicles that will come off of this architecture.
That Chief Engineer is responsible for establishing the bandwidth of this architecture. And so all subsequent vehicle variants, wherever executed, must be consistent with the predetermined bandwidth on that architecture.
Now, what is an architecture?
The fundamental underbody is very, very important because its lead times are long and it’s investment intensive; there are significant manufacturing implications in a bodyshop. The bandwidth of this is very important.
You can stretch the wheelbase, make the track wider etcetera and if you spend enough money, have got a big enough plant, you can accommodate all the flexibility that you want. So there’s a sweet spot in all of this and the sweet spot could vary if you’ve got a bunch of legacy plants around and you can’t invest in new plant – that could be a constraint that you have to consider in the bandwidth of this architecture.
And then there are a bunch of vehicle variants, different wheelbases etcetera – SUVs, convertibles, sedans whatever, that could come off of this architectural set.
One of the dangers of this is the ‘world car’ – same vehicle used everywhere. So, how do you prevent that because that was one of our learnings in the mid-nineties?
You’ve got some flexibility here with physical dimensions…
The example I like to use is: fundamental seat structure. Not the seat complete with foam and trim, but the actual structure of the seat.
We have designed a lego-set of seat structure that we have sourced through a couple of suppliers around the world so that the volume is obscene. The leverage associated with that is tremendous.
And then, depending on what vehicle comes off this architecture or another like-size architecture, you can plug and play different parts of this lego-set to get a seat back height that’s higher or wider etcetera and the customer would never know that it’s come from a common lego-set because you’ve got some flexibility in there.
And then we trim it up with foam and put the different trims on consistent with the brand needs around the world – whether it’s Vauxhall, Opel, Chevrolet or whatever.
There’s a sweet spot in this where you provide the associated leverage to the supply base and yet you’ve got flexibility to provide for brand differentiation.
I suspect that we will continue to learn what the sweet spot is. We’ll make some mistakes, we’ll overshoot on being common or maybe not common enough working with the supply base – it’s an iterative process.
So, the Architectural Development Team sets up the architecture and associated bandwidth. The actual execution of the vehicles and taking them into production can be done anywhere in the world.
And so what we’ve done is assign responsibility for each of these architectures. Small cars – mini and small – are developed in Korea where there’s a good skill set for small cars. Europe does more mid-size cars very well, good driving dynamics. Australia has always done magnificent RWD muscle cars etcetera – so there’s a skill set there that you take advantage of. Large SUVs are in North America; mid-size trucks in Brazil.
I had a conversation with our Board of Directors three and a half years ago on different business models we could apply on how we would execute our vehicle programmes around the world. We’ve settled on a business model that has a distribution of expertise around the world and the primary reason we decided to do that was that we wanted ears and eyes on the ground that really understood markets, and technical people that could take that and translate that sense or preference from the customer into technical requirements in the architecture.
Once the architecture and the bandwidth are established, the decision-making becomes very crisp.
DL: You said that, in the case of seats, the volumes are ‘obscene’ with two suppliers. Wouldn’t they be even more obscene if you had just one? Could you have gone with just one main supplier?
JQ: Having all your eggs in one basket could be attractive but potential risk on the other side is prohibitive.
DL: With two suppliers can you load the volume, say, 70:30?
JQ: Absolutely, yes. Also, we’re very interested in keeping competitive pressure on suppliers for a whole number of reasons. But seat structure is not rocket science; you can afford to have two suppliers pounding it out. There are some other areas where the technology is evolving where we would want to have even more suppliers, regardless of the leveraged opportunity with the volume.
Again, it comes down to where the sweet spot is. I suspect the sweet spot dithers and is also dependent on what manufacturer you talk to, what the givens are, what the manufacturing footprint is like, how you weigh the supply base in to support that, where the technology is – where it resides. For example, some of our entertainment stuff is moving more towards China, Korea. It depends on the part, the sub-system.
We negotiate that very carefully – our purchasing people working with technical people on this footprint issue.
In general it would be a bad thing to have, for a manufacturer the size of GM, a single supplier. Now there are some other manufacturers – you could go to BMW or whatever – and they’d tell you they’ve got one and I’d say ‘good, you’ve got a different situation to the one GM has’.
But some of these architectures generate big volumes – on the car side as much as 1.7m, several around the 1-1.2m level. So, if you ask a supplier if I could get them to 400,000 and any more and there’s not a benefit from a volume leveraging standpoint, so they’re kind of done in modules.
DL: You said that it was three and a half years ago that GM’s board decided to go with this global vehicle programme development strategy. What sort of cost savings are being achieved, in terms of materials and engineering?
JQ: What is planned to come off one architecture today previously came off five and that will avoid a billion dollars of cost around the world and we will also be able to deliver three additional vehicle variants off that single architecture than off the previous approach. We have a decision to make with that cost avoidance – whether to plough that back in or take it to the bottom line. For the most part we’re deciding to pour the coals to the portfolio and re-invest.
DL: How have the changes you talk about been received in the company and how has GM’s internal culture been impacted? Has there been a headcount reduction in engineering?
JQ: It depends on who you talk to. We are redistributing our resource around the world right now. The other thing we said when we talked about this to the board is that wherever we have a significant emerging market or a mature market, we are going to have a strong technical presence. If you have an emerging market, by definition there’s no-one there.
So the question was, three years ago, are you moving everything to India? No. But they are going to grow technical talent in India because it is a fabulous potential emerging market. We’ll start evolving the skill set there, putting more engineers in there.
At the same time, we’re distributing work to these Architectural Development Teams around the world. So, there’s a plus and minus thing that’s going on around the world right now. The growth centres are Korea, Brazil, India, China. At the same time we will continue to rightsize North America and Europe and we can do this through attrition.
We kind of have a glide path on how fast we can responsibly grow Brazil and these other places and we’ve got people retiring in North America who we simply do not replace – same thing in Europe.
So there is a redistribution of resource. The savings in cost avoidance we could take to the bottom line, but with the challenges we talked about – energy diversity, our global growth – if you look across the world we’re going to continue to maintain our resource level. There’s just going to be a redistribution consistent with these Architectural Development Teams and the emergence of some markets.
DL: How many engineers are we talking about, globally?
JQ: We’ve got roughly 20,000 technical people around the world – including engineers, designers and so on.
DL: What about the danger that with your globally based architectures, product is less attuned to local market requirements?
JQ: That’s a huge concern. Let’s use GM-DAT as an example. It develops the architecture for Corsa-sized vehicles – Gamma. I mentioned already that one GM person there is doing work on behalf of all of GM. The vehicle line executive responsible cross-functionally – engineering, manufacturing, bringing that all together around this architecture – is a German. The Chief Engineer, resident in Korea and working with him is Brazilian. The designer is a Korean. The manufacturing lead comes from the US.
So, when we populate these Architectural Development Teams, there is a cultural and customer diversity to begin with. First of all the leadership representation on these teams has a lot of diversity associated with it. So you don’t have ‘groupthink’.
The working level people in these Architectural Development Teams come from all over the world. So, if I’m a chassis engineer, I could come from Europe. I imagine we would have a strong technical presence in each of our mature or emerging markets – part of the reason is understanding customer preferences.
There’s a requirement setting and understanding process that goes back and forth between these architectural development teams from the technical people that are resident in each of these markets. And so coming into this bandwidth discussion are the interests and the preferences…
A couple of examples that are difficult to manage; I’ll give you a big one and a little one that’s important.
The big one is the dissimilarity in the way steel is processed around the world and associated coatings and so on. They form differently, they bend differently. You’ve got to comprehend those differences, work with steel companies to converge… it requires investment, there’s legacy and that’s a journey. You’ve got to deal with those dissimilarities.
The small example: horns. The requirements on horns. If you’ve been to China or India there are people just laying on their horns. You go to a couple of other places and people don’t even know where they are.
So if I were talking to a supplier for horns for GM, and if I were an engineer coming from North America, I’d specify a horn that would not live in China or India. And so that input into these Architectural Development Teams from around the world is critical because there are different customer usages and preferences.
And the Architectural Development Teams have to process all of that and find the sweet spot. You can’t accommodate everything. At the end of the day doing vehicles is tough and there are compromises to be made, but at least you have the benefit of knowing what you’ve got to integrate and work with.
There is a very real danger that some of these vehicles and architectures have a bias to a particular region or market, that’s dangerous. If that happens the bandwidth I’m talking about can’t be utilised. And I’ll tell you that in some cases we’re not doing as good a job as we ultimately need to, because people are learning and we’re a couple of years into this. It’s a very real concern.
DL: GM in North America has taken quite a pounding over a long period as it has lost share and been perceived as having inferior quality and reliability to, say, Toyota’s. From an engineering standpoint, what steps are being taken to improve GM’s perceived performance in these areas in its home market?
JQ: We’ve been globalising and integrating at a global level. The enabler to do that has been some local work on consolidation and integration. We went through a 10-year journey in North America from the early 1990s to about 2000. Europe went through the same thing with Project Olympia and some fundamental restructuring.
From a quality and reliability point of view, we’re coming from a world where a given number of engineers are trying to get into production and/or improve, for example, 36 different kinds of shifter mechanism around the world. We’re moving to four.
What that means is that if we have 10 engineers working in this space around the world those 10 engineers can bore in on four console shift mechanisms as opposed to 36. Do the math and that means more time per day, more interface with the supplier base, or whatever.
Attacking complexity and proliferation and the QRD impact of that is extremely important, I’d say one of the most fundamental things that we have been working on – not with globalisation, but everyone within their region.
We have tried to find a specialist to lead on shifter mechanisms too, a lead engineer, someone with the right skill set and who knows the ins and outs of shifter mechanisms – then directs activity with the other nine engineers working on shifters. It’s maybe like someone you would recognise in the Toyota system, down in the corner office, the ‘wise one’ who has been working on shifter mechanisms for 20 years and everybody naturally goes to that corner office to have a conversation.
We’re working towards that kind of environment in General Motors. Proliferation and complexity are big, big issues.
In the many years that we have been working on this subject we are convinced, for the most part, by data that we have closed that gap. Look at the JD Power surveys – Cadillac has beaten Lexus and so on. Even the data coming back from customers right now is beginning to help close the gap between perception and reality.
We still have a lot of work to do but I would say that very, very shortly, quality and reliability being a big differentiator is not going to be there.
DL: How do you see progress developing on the Volt plug-in? I know it is very early days, but are you perhaps getting a sense on how specialist suppliers are making technical progress with the battery technology needed?
JQ: The first thing is that the seriousness of intent and passion around developing the Volt is there. This isn’t a PR stunt. This energy diversity theme is real. There is no doubt that executing a vehicle like the Chevy Volt – the battery is lithium-ion – with the kind of range we are talking about, 40 miles, is extremely important.
We have the attention of the supply base. We are interested in diversification and competitive nature of the supply base in this regard.
As I said, in some areas we want 2-3 suppliers but there are other areas where we really want to encourage the juices to flow in the competitive area and this is clearly one of them.
Our observation is that a lot of this technology is tied up with Japan Inc. so strategically our company is very much interested in exercising the supply base differently with this technology than it has been in the past.
We have been very successful with a number of workshops and partnering sessions with different potential suppliers that are outstanding suppliers and are helping us with the lithium-ion battery. We’re very, very pleased with that work.
There’s a lot of very difficult technological sorting-out that has to take place with this. But we’re convinced, with the commitment we have to the Volt, the attention of the supplier base and a lot of very good work has been done in a relatively short space of time. A lot of folks were kind of poking around anyhow, unbeknown to us, and we’ve flushed a lot of that out. But what you find though is that there are very few suppliers who are fully integrated from original cell knowledge – at a battery level – to integrating those cells to produce a workable battery, to manufacturing precision that is required to deliver that integration. Very, very few in the world. One or two can do that. So what we are also trying to do is link some suppliers together so that there is a more integrative approach to delivering the whole package.
That’s the larger issue right now. Cell technology will get sorted out. Integration is a bit tougher. Manufacturing precision and putting these together at high volumes is yet another opportunity.
DL. Your gut feel is that it is going to happen?
Yes. Invariably if we want something to happen in this company it’s got a good shot. We’re very, very committed and the supplier base is working very well with us right now.