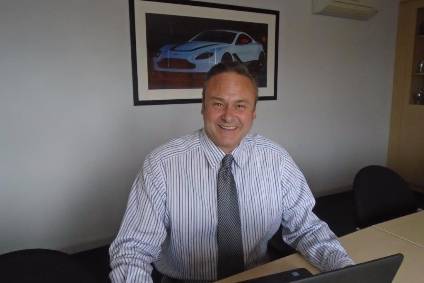
As the application of carbon fibre in car manufacture increases, demand for custom and novel finishes has also soared. UK-based Project 12 develops and supplies finishes and coatings for carbon fibre and composites. just-auto/QUBE spoke to managing director Dave King to learn what automakers are seeking and the direction carbon fibre finishes are taking.
The concept of ‘mass customisation’ is one that is increasingly on the agenda of OEMs. Recent investments in JLR’s SVO department, Aston Martin’s ‘Q’ and Ferrari’s ‘Tailor Made’ are examples of how automakers are responding to the often more nimble tuning and customisers that have risen in prominence. Alongside performance engine enhancements and bespoke interiors, one material that has seen a rise in consumption is carbon fibre. From ‘hot hatches’ through to luxury limousines and SUVs, this composite material is no longer purely reserved for motorsport specials. For luxury cars, it is almost a commodity.
Can you tell us a little about Project 12?
Of course. Project 12 was originally a division of Carbody, one of the leading independent crash repair businesses in the UK. Based in Banbury, that business is repairing 80 cars a week. That’s a lot for a small market town. I’ve been working there since I was 15 so have developed a lot of connections and whenever somebody needed something ‘automotive’ painting, I tended to get the ‘can you just’ requests. One day, I was approached by a company who had created a patented paint swatch displays in the retail dealers. We were able to paint these swatches to a high standard and meet the OE requirements. Doing this job on time and to the right standard provided greater access to the marketing departments of the OEMs and generated more requests. It was during one of these sessions at JLR that I was asked if we could paint carbon fibre. It wasn’t easy but it was such a huge opportunity and this material was so futuristic. At that point I’d only seen it on professional race cars, so we had to make it work.
How has the business developed?
We have now become a trusted coatings supplier and grown to 37 staff in our Banbury facility. In mid-May this year, I sold my shares in Carbody and bought Project 12 from the Group. Today, I am focussed solely on managing the development of the business.
How well do you really know your competitors?
Access the most comprehensive Company Profiles on the market, powered by GlobalData. Save hours of research. Gain competitive edge.
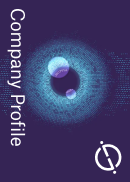
Thank you!
Your download email will arrive shortly
Not ready to buy yet? Download a free sample
We are confident about the unique quality of our Company Profiles. However, we want you to make the most beneficial decision for your business, so we offer a free sample that you can download by submitting the below form
By GlobalDataIs painting carbon fibre so different to other materials?
“We have our own IP and have developed an accreditation with Loughborough University to recognise the skills needed.”
Absolutely. Getting a high-quality finish consistently requires a very deep understanding of the surface structure. We have spent 10 years immersed in developing processes and procedures to achieve this. So much so that we have our own IP and have developed an accreditation with Loughborough University to recognise the skills needed. We have another programme starting with the National Composites Centre too. I’m really proud of how far we have come with the recognition of the skills needed.
But why is it so difficult to coat carbon fibre? Can’t the OEMs just do this in-house?
There are two key factors. First, despite the rise in the use of carbon fibre, it remains almost a cottage or artisan industry. The process for creating parts is very labour intensive and very little is automated, most parts are hand-made. That means the surface structure varies significantly. Secondly, carbon fibre is delicate and the piece part cost is high. Some of the parts we receive are over £20,000 each, some of the most expensive parts on the bill of material. Carbon fibre really needs careful handling, particularly in the preparation of the surface. You simply can’t sand or abrade the surface as you would with plastics or metals, that would damage the fibres and compromise its structural integrity and you are left with expensive scrap. It is almost impossible to rework. To master this, Project 12 has developed specific expertise and IP to create a surface suitable for carbon lacquering. You need trusted and trained operators to do this work and at present, it remains too niche for most OEMs. Each stage of our process has been designed to minimise handling and damage. We have cut process times down so we don’t have stock on site too. We have tailored our entire flow to achieve this minimal work in progress. The end result is that we consistently meet OE quality standards and don’t see returns. For the OEMs, that is a massive cost saving and reduces the risk of additional handling.
What type of coatings are OEMs looking for today?
“Customisation, one-offs, are in high demand, particularly in emerging markets but all over the world.”
We are developing and expanding the range all the time. Our customers, the OEMs, are always looking for something innovative or novel to offer to their end customers, something that will wow them. Customisation, one-offs, are in high demand, particularly in emerging markets but all over the world. These car owners are seeking something unique, bespoke. The customising companies had started to gain real traction but we are seeing the OEMs fight back and doing things that would not have been possible, say five years ago.
Can you be more specific on the coatings?
Yes. We are seeing that for some, even standard carbon fibre has become a commodity. So alongside the gloss clear lacquers, we now offer matte as well as tinted coloured lacquers. Crucially and how we differ from coloured carbons you may have seen, is that we achieve all of our coloured finishes using the standard composite material. The colours are all in the lacquer. That means that the composite manufacturer doesn’t need to keep rolls of all the different coloured carbon in its fridge to offer different coloured parts. Composites materials have a shelf life so we can minimise complexity, storage issues and cost this way and offer a much wider range of colours without the hassle. Designers have said that our approach creates a more vibrant finish with greater depth than the coloured fibres. One designer has cited that we can achieve an almost holographic appearance.
How are these new finishes decided?
The majority of innovation comes from working together. We are privileged to sit on a number of ‘think tanks’ with the designers at the OEMs and these discussions stimulate the creation of new finishes. That said, we also have some very talented people working at Project 12 who have ideas and want to try things. We invest a lot in R&D. Some of our work is similar to the fashion industry. Some of these car owners want their cars to feature the latest colours, finishes or materials or something no-one has. They won’t wait three years for the next model either. They expect things now and that’s a big advantage that we can offer the OEMs. In recent months we collaborated with jewellers and a sculptor with a two-way dialogue of ideas that will ultimately appear on cars.
What automotive components are you coating?
It really depends on the OEM. For example, with one customer we do all the visual carbon parts and that could be the whole exterior, everybody panel. For others, it could be sill finishers or the roof panel. One tuning company customer requires us to paint part of the bonnet in body paint and leave an area in lacquered carbon fibre. And we have to achieve that without any step line or line in the surface. That is extremely challenging but looks stunning and when customers run their fingers over the line and find it is smooth, it’s a great sense of perceived quality and something they can proudly show to their friends. At this level, every detail is key. Of course there is a vast array of interior parts including dashboard, seats and door trims that was traditionally the area where carbon was originally found, purely for decorative purposes.
But what about harsher applications? We are seeing composites in use in all areas of the car.
That is true. We can finish in higher temperature environments such as under bonnet parts including air boxes, cam covers, intakes and I’m very excited about a project we are involved with in the production of full carbon fibre wheels. We’ve got some interesting marine programmes where we are developing coatings to cope with very harsh environments. Automotive is tough but these are another level of aggressive environment.
Who are your customers in the automotive world?
“We are supplying eight European OEMs and five Tier Ones.”
We have the typical restrictions on saying who we work with but I can say we are supplying eight European OEMs, a further five Tier Ones and a multitude of tuning and customisation companies.
If customisation is about the latest thing, what is the next thing?
Expect to see more solutions beyond simple lacquering. Multilayers, the ability to include designs, logos or text within the composites. We can pretty much do any colour but you might have seen some of the clever use of colour variations within the lacquer at the Geneva Motor Show. I counted around 10 cars with our products on display.
Other developments include incorporating diamonds in the lacquer to make it glisten and literally sparkle. We are doing some interesting things with gold at the moment too. We had a lot of interest from the Far East for that concept. These are very exciting times as at one end, the technology becomes more mainstream and at the other end, it is evolving to be more exclusive. OEMs want to be part of this opportunity and not leave it all to the customisers.