
Continuing QUBE/just-auto’s series of interviews with tier one automotive component suppliers, we spoke to Ben Patel, Vice President and Chief Technology Officer, Tenneco.
What are the megatrends in the automotive emissions control industry and how are they shaping the look and feel of tomorrow’s solutions?
We are, of course, continuously monitoring megatrends impacting our industry. For emissions that includes the regulatory environment, powertrain strategies, electrification and lightweighting. We look at how these trends might change our customer product portfolios and the resulting effect on our product offerings. The most significant of these trends is the increasingly stringent emissions regulations for both light and commercial vehicles in every major market around the world.
In the US and Canada, where the Tier 2 passenger car and light truck requirements are already the most stringent in the world, the transition to Tier 3 emissions standards will result in a further 80 percent improvement in NOx emissions by 2025. In Europe, the EU6c and subsequent Real Driving Emissions (RDE) EU6d standards are ensuring that all vehicles provide effective in-use control of emissions. For commercial trucks, the accelerated implementation of advanced emissions controls under the China VI and Indian Bharat Stage VI requirements will improve air quality in these high growth vehicle markets.
More stringent emission requirements will drive new solutions that we, as a supplier, need to offer to make our customers successful. For criteria pollutant emissions such as NOx and particulate matter, in Europe the focus is on RDE to ensure that vehicle emissions targets, which are met in certification laboratories, are also met in real driving situations. Our product portfolio supports OEMs in meeting those requirements. We are continuously shaping our solutions to support our customers in meeting increased fuel efficiency targets, which is the only way to reduce CO2 emissions, with a technology portfolio that encompasses lightweighting and waste heat recovery, to name a few.
What impact has the VW diesel emissions scandal had on Tenneco’s business?
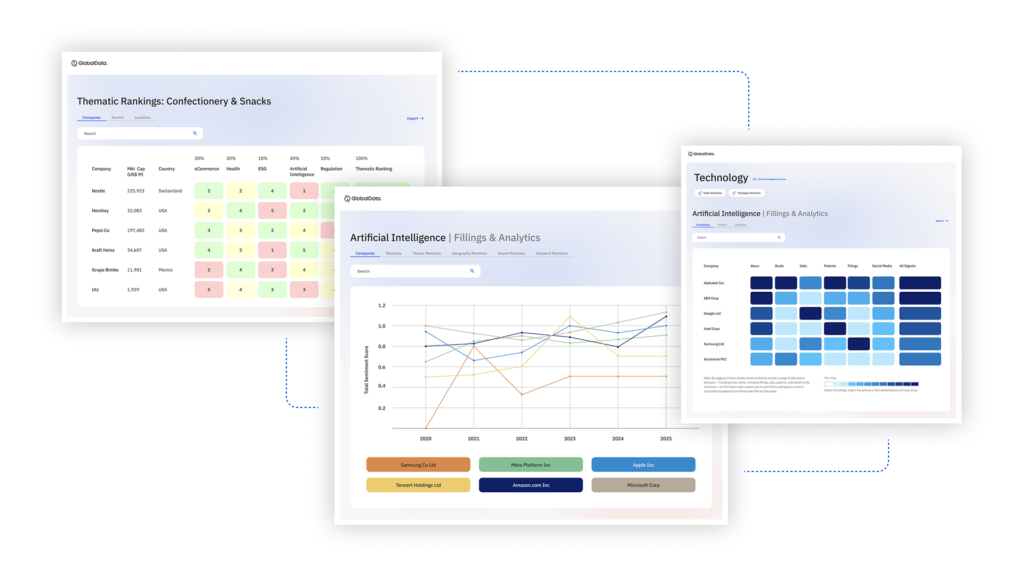
US Tariffs are shifting - will you react or anticipate?
Don’t let policy changes catch you off guard. Stay proactive with real-time data and expert analysis.
By GlobalDataThe issue [VW diesel emissions scandal] has increased sensitivity to the importance of compliance and the need to adhere to emissions targets globally.
The issue has had very little direct impact to Tenneco, as we did not supply the systems involved. Certainly, the issue has increased sensitivity to the importance of compliance and the need to adhere to emissions targets globally. In Europe, implementation of the RDE requirement under Euro 6d regulations supports better transparency and helps ensure compliance. In general, the increased sensitivity on compliance makes Tenneco’s products and our capabilities even more critical to our customers.
How much impact will reduction in the use of ICE have on your business?
There is a lot of attention on electric vehicles and hybrid powertrains, however internal combustion engines (ICE) continue to be the solution for nearly all future powertrain applications.
Industry experts estimate that 96 percent of the light vehicles produced in 2030 will have improved ICEs, including various forms of hybrid vehicles, while only 4 percent of vehicles will be powered solely by battery electric and fuel cell electric drivetrains. It is worth noting that there will be more ICE powertrains produced in 2030 than today even if BEV production is significantly higher than forecast. Additionally, ICEs in 2030 are expected to have 20-30 percent more regulatory content than today as emissions requirements become more stringent.
While we continue to monitor the EV market, we see strong growth opportunities ahead for our business.
Tenneco’s emission control technologies offer solutions for all of these ICE applications. While we continue to monitor the EV market as the technology continues to develop and begins to mature, we see strong growth opportunities ahead for our business.
Could you comment on how developments in aftertreatment are affecting the choice of engine management strategy?
One example that comes to mind is the upcoming EU6d RDE regulation which requires gasoline engines to meet the particle number (PN) limits under most realistic driving conditions. The initial strategy of OEM’s was to meet these targets by adjusting engine combustion and calibration, thus making trade off decisions for fuel efficiency and drivability. The newly developed Gasoline Particle Filter (GPF) technology helps to meet the PN limits while engine combustion and calibration can be optimised for fuel efficiency and driveability.
We have heard it said that the last remaining major challenge for powertrain engineers is to do something about recovering the 30 percent of fuel that disappears as hot gases down the exhaust pipe. What can be done about this?
As a provider of aftertreatment systems, we are working on various ways to harvest the heat from exhaust gas and recycle it back into either mechanical or electrical energy.
In addition to the Rankine cycle, we are also working on thermal-electric generators, as well as thermal-acoustic generators. In thermal-acoustic generators the heat energy from the exhaust gas is converted into sound energy. Put through a transfer fluid like helium, the harvested energy can ultimately drive an electro-mechanical generator.
I guess one solution is a thermoelectric generator (TEG) which can use virtually any heat source, including waste exhaust heat, to produce electricity using the thermoelectric effect. Given the infancy of the TEG market, there are a number of unknowns. But, in general terms, how do you foresee the market acceptance for TEGs in Europe?
We expect TEGs to be part of future exhaust systems.
The TEG is one technical solution to partially recover exhaust heat. Based on the Seebeck effect, specific thermoelectric materials can convert the exhaust heat directly into electricity. While research continues on how to develop the most cost-effective TEG, we expect the technology will be part of future exhaust systems.
Could you comment on some other ways in which the megatrend for lightweighting has influenced your exhaust system designs?
Lightweighting is an ongoing requirement in exhaust system design. Material thickness of gas leading pipes and components is balanced by appropriate decoupling and hanger concepts and architectural optimisation to avoid any compromises in durability or NVH. Heavy, cast iron manifolds are replaced by lightweight fabricated manifolds with low thermal inertia, which also helps to improve emissions. Our advanced technology group is continuously screening and testing alternative materials to remove weight, including titanium, which we have in serial production on some niche applications.