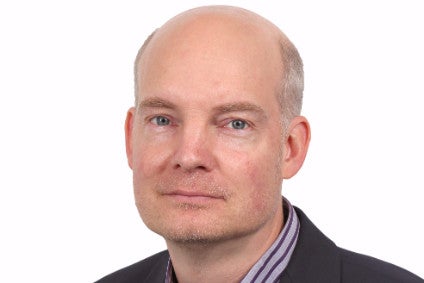
We hear a lot about the increased use of virtual development processes, so it may come as a surprise to hear an expert in simulator software argue the case for the importance of input from a real driver. Chris Hoyle, technical director of UK simulator software company, rFpro explains what a driver can contribute to this process.
The use of virtual development processes seems to be increasing continually. Where does the pressure come from and where will it all end?
With connectivity and digitisation at the top of many industry executives’ agendas, not to mention potential competition from new players such as Google and Apple, the lead time for new product introduction has to be shortened in order to remain successful. As automakers try to reduce their product development lead times and costs, increasing use is being made of computer modelling and simulation in many areas of vehicle design and engineering.
So what can a driver contribute to this process?
Modern CAE methods have become sufficiently well correlated to allow reliable simulation in areas such as powertrain performance, body strength and stiffness, aerodynamic behaviour, and even styling through full-size digital 3D renderings. There are though some areas where only evaluation by a human driver can ensure 100 percent validation of a new design.
The missing element – the final piece of the virtual reality jigsaw – is the capability for a human driver to assess those areas of the vehicle that have a critical influence on how it feels and responds to human input. Obvious areas of interaction include ride comfort, vehicle handling and steering response. The way in which the increasing number of driver assistance functions are perceived by the driver, as a help or a hindrance – is also an important factor, particularly in a highly dynamic situation such as an emergency manoeuvre.
How well do you really know your competitors?
Access the most comprehensive Company Profiles on the market, powered by GlobalData. Save hours of research. Gain competitive edge.
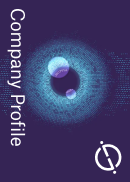
Thank you!
Your download email will arrive shortly
Not ready to buy yet? Download a free sample
We are confident about the unique quality of our Company Profiles. However, we want you to make the most beneficial decision for your business, so we offer a free sample that you can download by submitting the below form
By GlobalDataWhy is this important?
Without this safeguard, tooling investment will always be at risk from engineering changes required late in a vehicle programme to eradicate issues related to the man-machine interaction. Many of the engineering ‘sign off’ criteria for a vehicle, such as refinement, gearshift feel, behaviour of driver assistance systems and ride quality are ranked on the drive appraisal scores from human judges. This makes driver-in-the-loop (DIL) simulation directly relevant; a vehicle-dynamics focused DIL simulator allows evaluation of these criteria while still at the model-based engineering stage, before any hardware has been manufactured.
How big are the potential benefits from this approach?
Besides cutting development lead time, there is the potential to make large financial savings by extending the use of virtual testing to include those areas requiring human driver input. The annual spend on prototype vehicles, across the global car industry, has been estimated at $10bn, so the sums are significant.
One user of our technology, AVL, has estimated that over 30 percent of the costs incurred in the development of a vehicle’s driving attributes can be saved through frontloading the engineering activity on a DIL simulator with subjective feedback, which provides better and more complete information earlier in a vehicle programme.
What has happened to make this feasible?
Driving simulators can allow effective DIL testing provided they meet two fundamental, and related, requirements; a high level of immersion and low latency.
Good immersion means the driver believes he or she is at the controls of a real vehicle; they react exactly as though in real situations. The cues they receive – visual, aural, haptic (by touch) – must be individually convincing and all synchronised to reinforce one another. The response of the system to the driver’s input must be without any perceived delay (latency) in order to provide realistic behaviour and allow useful interpretation of the driver-to-vehicle interaction.
Traditional vehicle simulators which evolved from aircraft industry technology are pretty ineffective for studying dynamic vehicle behaviour with the driver in the loop. They are simply too slow, and in the automotive simulator world speed is the key to accurate results. The overall response of a simulator is driven by both the software speed and the inertia of the motion platform itself.
While platform providers have been successful in reducing mass from as much as four tons to as little as 250Kg. rFpro has developed low latency software that provides video signals 10 times faster and audio signals 20 times faster than was previously possible. These are the developments that have largely contributed to the new levels of realism.