Yazaki Corp manufactures and markets a wide range of products, most prominent among them being the automotive wiring harness. Yazaki is the world’s largest manufacturer of wire harnesses, supplying harnesses to the major vehicle makers worldwide. In June 2006 Matthew Beecham talked with Doug Burcicki, senior manager of marketing and product management and Fawaz Baltaji, product manager of data links, about how the company is pushing back the technical boundaries in the vehicle electrical and electronic distribution systems arena.
just-auto: While cost pressure is surely driving the industry to more creative solutions, what other factors are driving changes in the vehicle electrical and electronic distribution systems market?
Doug Burcicki: Cost pressures are driving many decisions today – some OEMs are doing a better job of analyzing the entire value chain and its impact upon the total vehicle cost, while others are focusing more on piece price analysis and thus are missing overall cost reduction opportunities. Other factors that are impacting our market is the increasing complexity requirements, as well as a reduced amount of time to design and develop a given product or technology. Both of these issues are forcing us to become more innovative in every aspect of our business, which means technology, manufacturing footprint, logistics flows and validation techniques must all be revisited and improved upon in the search for increased efficiencies and waste elimination.
just-auto: Although conventional round wire harnesses continue to evolve to support additional electronic content in vehicles, the technology has remained much the same over the last 50 years. Going forward with steer-by-wire and brake-by-wire technologies emerging, can the current wiring harnesses technology cope?
Doug Burcicki: While there is a continuous flow of alternative technologies into the vehicle that allow for reduced circuitry per feature, it can’t keep pace with the number and complexity of features being introduced into today’s cars. Several years ago, navigation was a high-end option with a less than 5% take rate on 10% of the luxury vehicle market. Today you can get this option on cars that sell for well under US$20,000. The same can be said of tire pressure monitoring systems, which was a high-end option and is now a mandated feature for the cars we are designing and developing. Examples like this are endless – there will always be alternatives to traditional wiring, but it is hard for those alternatives to compete on cost, quality, reliability, etc. on a regular basis. For these reasons, the wiring harness will continue to grow in complexity. Of course there are limits to what can physically be packaged in a vehicle, so we must be aware of alternative technologies to address those application specific situations that necessitate alternative solutions. However, many of the solutions come from system level improvements – like multiplexing, partitioning, and routing — not necessarily from unique technologies.
just-auto: As the complexity of the wiring harness design moves into uncharted territory, how does that impact on Yazaki’s design and development capabilities?
How well do you really know your competitors?
Access the most comprehensive Company Profiles on the market, powered by GlobalData. Save hours of research. Gain competitive edge.
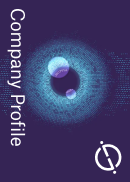
Thank you!
Your download email will arrive shortly
Not ready to buy yet? Download a free sample
We are confident about the unique quality of our Company Profiles. However, we want you to make the most beneficial decision for your business, so we offer a free sample that you can download by submitting the below form
By GlobalDataDoug Burcicki: The best way to address the increasing complexity of a new vehicle is to be involved with the OEM from day one. This enables us to understand their priorities, goals and objectives, which ultimately are the drivers behind the designs. Many times the engineers at the OEMs are required to implement unforecast requirements late in the development phase. This drives revalidation of the subsystem and even the vehicle in some cases. Besides being costly, this situation is prone to allow for ‘shortcuts’ in the process, which will ultimately result in potential quality and performance issues. Yazaki has developed multiple solutions that range from component-level parts all the way through the value chain to manufacturing and logistics, which ultimately allow for increased flexibility and OEM customer satisfaction. We pull from our vast experience in component development, product validation techniques, software analysis and design tools as well as our strong logistic and manufacturing capabilities to provide a flexible and adept supply chain to our customers. Some of our techniques have been piloted in highly complex environments such as commercial truck and are now being applied to the mass market of automobiles.
just-auto: When we think about the conventional wiring system architecture, presumably adding a device means adding a new wire. Or does it? Are you now seeing more and more inter-connects which are basically protocol based? What are the implications?
Doug Burcicki: There is a constant migration of alternative technologies into the vehicle – fibre optic, wireless, multiplexed systems, etc. All of these, in conjunction with ever-increasing amounts of integration, mean that the EDS supplier has to have a broad understanding of the vehicle environment and the performance requirements. Being an EEDDS (Electrical Electronic Distribution & Display Systems) supplier allows for Yazaki to gain access to all aspects of the vehicle electrical system, which enables us to implement innovative solutions. Recently, one of our customers requested that we develop a CAN termination device due to bussed module additions and the CAN branch length requirements. Rather than simply responding to the request, we analyzed the design and the feature complexities and recommended a routing and partitioning change that allowed for the additional module and met the CAN requirements, without the addition of the CAN termination device. This solution saved more than US$10 per vehicle and reduced part numbers over the OEM’s primary direction.
just-auto: Although wireless systems are still costly, do you see them playing a major role in the future?
Doug Burcicki: Yes, wireless content will gradually continue to grow in the vehicle, but it will be slow growth due to the cost benchmark (wiring) being so low. One area that will grow at a faster rate will be that of sensors and their respective inputs to various modules. The number of sensors continues to increase and will continue to do so due to emission and safety requirements for the newer vehicles. Many of these additional circuits need to be packaged in and around the engine block and underbody, in these locations the wiring benchmark increases due to higher temp requirements, protective provisionals as well as requiring pass through components (grommets & seals). Obviously there are also packaging and weight savings to wireless systems that, for some OEMs, offset some of the cost penalties, thus making wireless solutions a potentially attractive option.
just-auto: As we understand it, Yazaki is heavily involved in developing multiplexes systems. How do you approach design and development of such systems?
Doug Burcicki: Multiplexing in the vehicle environment is a difficult thing. However, once again, because Yazaki is an EEDDS supplier we have years of development experience in regards to the physical layer, electronics and the software that enables us to deliver efficient and reliable multiplexed subsystems or enabling components.
just-auto: What other solutions are you currently working on?
Doug Burcicki: The auto industry is going through some tough times right now, and for an innovative company like Yazaki, institutional discomfort is not necessarily a bad thing. In order to remain competitive in this environment, we are forced to re-evaluate all aspects of our value chain including design, development, purchasing, manufacturing, logistics, IT, strategic roadmap development and deployment – just to name a few. For Yazaki to continue to be the market leader, we need to continue to innovate product, process and business models on all fronts.
just-auto: Could you compare and contrast the North American market for multiplexing with Europe and Japan?
Doug Burcicki: When comparing the three regions there are historically three distinctly different approaches. To summarize, Europe likes to collaborate via consortiums (CAN/LIN/MOST/Flexray) and standardize protocols and even physical requirements. The advantages are obvious: the suppliers compete with each other early in the development in the hopes of securing large chunks of business, while the OEMs ensure that the supply base is diverse and capable, thus increasing sourcing flexibility and driving cost down while providing reliable systems. In North America, the OEMs tend to take the output of these EU-developed protocols and adapt them to their own needs (CAN/LIN), with each application adhering to the spec with some OEM specific nuances which prohibit cross utilization amongst the vehicle makers. This is usually the result of different development priorities (ex – reuse, cost, performance) or focusing on cost reduction in a particular area (ex – wiring vs. module). The North American OEMs do benefit, though, from using relatively ‘mature’ protocols, and there is an ample supply base to pull from. In Japan the approach has typically been to develop proprietary protocols (BEAN, M2M) that meet the OEMs needs perfectly. These protocols are often developed in house, which allows for system optimization and integrity – representing a value apart from piece price. However, this trend has recently been changing with many of the Japanese OEMs utilizing CAN and being actively involved in the AUTOSAR standardization activities.
just-auto: What about other alternatives to the traditional wire harness, such as fibre optics?
Fawaz Baltaji: Depending on the application, fibre optics and short-range wireless solutions are alternatives to the traditional wire harness; however, copper based wire harnesses remain the most cost effective and robust solution today. We view these alternatives as complementary technologies where fibre optics solves many traditional issues, such as electromagnetic immunity, weight, bandwidth, communication range and provides increased security. Wireless, on the other hand, provides mobility and architecture implementation flexibility.
just-auto: As we understand it, the European market has considerable experience in the application of fibre optics, applying it to multimedia systems. In the US, however, it is extremely rare to find it in cars. North Americans are simply not pumping this kind of data stream around the car requiring that bandwidth. How do you see the future for this technology in North America? Is the position any different to, say, Europe or Japan?
Fawaz Baltaji: Today, European OEMs have been leading in the introduction of high-end infotainment devices that normally demand the most bandwidth around the vehicle. This high-bandwidth connectivity need is predominately driven by the OEM’s choice of architecture implementation, distributed versus centralized (an all-in-one box approach.) For many reasons, European OEMs prefer a distributed approach, and therefore demand a diverse range of high-bandwidth connection systems such as Low Voltage Differential Signal, Optical MOST and others. The North American market has started to demand very similar features, such as large multifunction displays, rear seat entertainment, enhanced HMI, consumer electronics interface ports, and on-board video. The requirement for some of this device-to-device connectivity in a semi-centralized EDS architecture will exceed 1Gbps, and therefore, North American OEMs will soon have to cope with many of the challenges European OEMs faced. By contrast, Japan has not showed any interest in optics; they have opted for different architectures (centralized) that eliminate the need for high bandwidth requirements throughout the vehicle. While the feature content and architectures are evolving to the point that Japan will see high GBit requirements, they are opting for copper based solutions rather than optical.
just-auto: How do you see the outlook for flat flexible cables as an alternative to conventional wire harnesses? Are flexible cable systems still too costly? What are the issues?
Doug Burcicki: At this time it is for niche applications only when there are severe packaging constraints due to the amount of feature content in a particular area, such as a headliner. We have prototyped several subsystems utilizing both FFC and FPC, and the only way they can compete with traditional wiring is through component elimination. For example, the connection system from the conductor to the device must be eliminated, otherwise it is just a substitution for wiring. That won’t compete on a cost level. In the future, there will be possibilities for surface mount switches and lights as well as a ‘component’ level harness assembly. What I mean by this is a FFC/FPC harness would be assembled with the devices as part of the modules; essentially the FPC (an extension of the harness) would replace the PCB in the device. Aside from the technical hurdles with this approach, it would dictate a new business model for most OEMs, where the terminations would be made by the Tier 1 or 2 rather than at the vehicle assembly plant.
just-auto: To what extent does the growing number of sensors carried by vehicles pose challenges to Yazaki’s electrical circuit designers, particularly since the data produced by the sensors may be required by several systems operating in real time, e.g. safety and emission control?
Doug Burcicki: The challenges to Yazaki are multiple. The number of sensors is growing at a tremendous pace and the main drivers of this are safety and emissions. Next would be comfort/convenience features the OEMs are providing. As several of these sensors are part of critical safety subsystems, their signal integrity is of paramount importance. For this reason, Yazaki is constantly experimenting and testing alternative methods of providing reliable signal integrity whether it is through EMI shielding properties or through terminal materials that both meet performance requirements and exceed cost expectations.
just-auto: Is the industry ultimately moving toward ‘plug-and play’, as seen in the computer industry?
Fawaz Baltaji: The industry is definitely interested in a ‘plug-and-play’ approach; however, they have to overcome many challenges before getting there such as agreeing on an open standard for fundamental software system functions that replaces proprietary standards.
just-auto: As we understand it, one of the main initiatives trying to achieve standardisation that allows you do plug and play is AUTOSAR. Although this consortium sets out a noble desire for standardisation, we wonder if the image versus the reality will be the most difficult thing to achieve. What is your opinion of how AUTOSAR could introduce a common standard?
Fawaz Baltaji: We believe that AUTOSAR should focus on demonstrating its effectiveness in the body ECU layer as well as possibly the infotainment layer. Additionally, they should define the most basic levels of software, such as low-level drivers, module and operating systems interface, and create a highly flexible and adaptable infrastructure that suppliers can build on.
Global market review of vehicle electrical wiring systems – forecasts to 2012 (download)