Although the electrically-assisted steering market is relatively small in North America, manufacturers say this market will grow. Demand on both sides of the Atlantic is being fuelled by a range of factors, not least that electric systems are more economical to run, lighter, recyclable and easier to package and install compared to conventional hydraulic systems. Matthew Beecham talked with Charlie Cregeur, director, global steering product planning for TRW Automotive’s chassis division to find out how the steering market is shaping-up.
just-auto: Could you talk us through TRW’s roadmap for its steering systems?
Charlie Cregeur: The steering system is the first and foremost man-machine interface to the driver. Every review written about a vehicle includes a comment about the steering feel. European vehicles are very demanding in terms of steering and handling performance.
Vehicle designers have four basic options when choosing a steering system.
Going from least to most complex we begin with manual steering. This is the system where there is no power assist and all steering torque [the energy the driver puts into turning the steering wheel] comes from the driver. These systems are rapidly loosing market share and are being replaced with a form of power-assisted steering.
Next in line comes the hydraulic power steering [HPS] which uses fluid flow and pressure from a belt-driven pump off the engine. HPS gears have been around for decades and over time suppliers and OEMs working together have been able to create a remarkable array of “steering feel” that often becomes part of the signature of the vehicle itself. A HPS system uses fluid flow from the pump gated through a precision ground valve to push a piston left and right on the rack, i.e. the bar that actually pushes the wheels left and right. From a cost standpoint, HPS systems cost more than a pure manual steering system given the addition of the pump, hoses, belt, fluid and gear with gating valve.
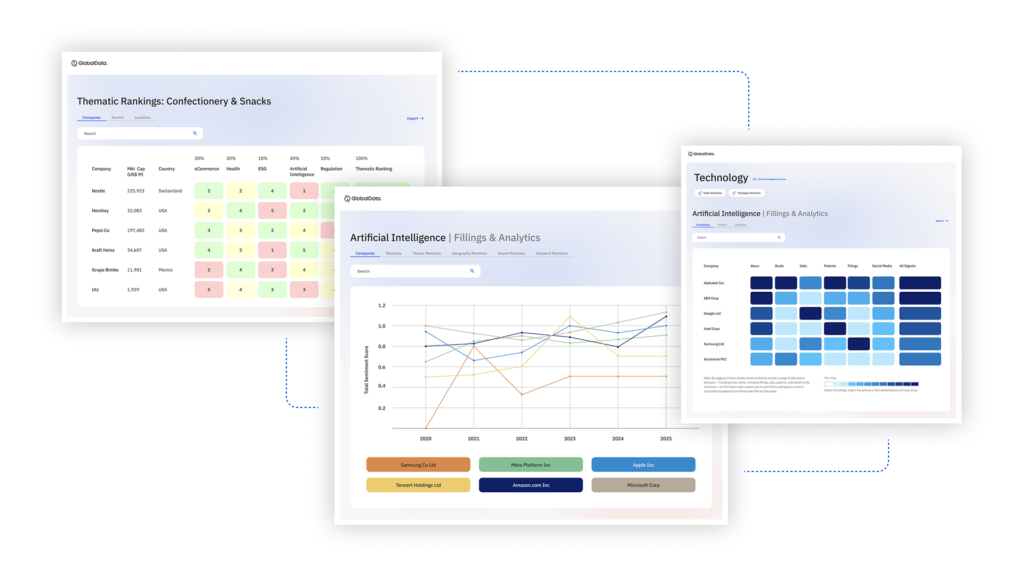
US Tariffs are shifting - will you react or anticipate?
Don’t let policy changes catch you off guard. Stay proactive with real-time data and expert analysis.
By GlobalDataMoving up the scale we find two types of electrically-assisted steering. TRW introduced its Electrically Powered Hydraulic Steering [EPHS] into the market in the late 1990s, replacing the mechanical pump and belt with a motor driven pump under software control. There are several important advantages of EPHS to consider. First, it removes the pulley and belt from the engine providing a much greater degree of freedom to the vehicle designer under the hood on pump placement. Second, the EPHS provides CO2 emission reductions that can range up to 3% as well as the associated fuel savings as compared to a conventional HPS system. With the ever increasing strictness of CO2 regulations in Europe, this is a very attractive option for vehicle makers since they can retain the HPS gear and steering feel they have identified with a given vehicle. Third, the EPHS makes it possible to convert a standard vehicle to a hybrid where there is no pump to pull power off the vehicle engine or, in the case of the emerging start-stop vehicles, the EPHS can still provide power assist when the vehicle engine is turned off, say at traffic lights. Fourth, an EPHS provides a feature called ‘speed proportional steering’ whereby as the vehicle speed increases, the pressure and flow from the pump can be decreased under software control to reduce energy consumption. Fifth, an EPHS system can be configured where the pump and gear as one unit arrive at the OEM assembly plant fully filled, tested and ready to be bolted into the vehicle saving time on the assembly line.
Finally, we reach the last steering type called electric power steering [EPS]. In an EPS system, the assist is provided by an electric motor coupled somewhere along the steering column or on the gear itself. In this system, the pump, belt, pulleys, hoses and fluid are eliminated from the steering system. An EPS system is able to provide all the features of an EPHS and reduces CO2 up to 3.5% based on TRW tests on a 1.6-litre engine. In addition to the physical differences between EPHS and EPS products, the EPS can provide a function called Torque Overlay that allows the EPS to take in a signal from somewhere else in the vehicle. This signal can be programmed in the EPS to either “coach” the driver by putting a gentle torque on the steering wheel or allows the vehicle to be steered completely by remote control without the driver turning the steering wheel in the case of semi-automatic parking. Torque Overlay is becoming a highly desired feature as it allows for integration of steering, braking and passive restraint systems.
An example of this integration is when the ESC system detects the vehicle is going into a skid, ESC can gently apply one rear brake plus coach the steering to correct the trajectory of the vehicle. When the ESC senses the unstable condition it can also notify the TRW Active Control Retractor [a motorised seatbelt retractor] to snug down the drivers belt and, if the vehicle is stabilised again, return the belt to the pre-event tension automatically. If the instability cannot be corrected, the ESC control unit can then notify the airbag control unit and pre-arm the airbag firing algorithms that can provide additional milliseconds of warning before deployment. TRW is unique in that we are one of only a very few tier one suppliers in the world that has the ability to do this three-way integration. We call this ability Cognitive Safety because we have the skill base plus the technology to sense the world around the vehicle and help the driver respond to various driving hazards.
Taking all of the above into consideration, the vehicle designer has a wide array of choices when specifying the type and performance of the steering system for a particular vehicle. Weight, packaging, performance and cost can all be traded off. As a full service supplier, TRW has opted to include all four of these product types in our portfolio.
just-auto: As we understand it, there are basically four types of EPS (electric power steering) EPHS (electro-hydraulic pump steering); RD EPS (Rack Drive EPS); PDEPS (Pinion Drive EPS); and CD EPS (Column Drive EPS). Which segment is showing the highest growth these days?
Charlie Cregeur: EPS Rack Drive which uses a belt to connect the electric motor to the steering rack is the fastest growing system in the market today. EPS CD has the highest application rate. TRW has been producing EPS CD for over four years and we will launch our first EPS BD system later this year. Over time TRW has developed and tested EPS pinion drive and concentric rack type products but we have found the CD and RD belt drive to be the most application friendly and cost-effective products. Fitment of EPS on A through C segment cars has been growing steadily in the last few years but we see the D and larger segment vehicles seeking EPS solutions so these larger vehicles are not outperformed by their smaller segment counterparts.
just-auto: In the early days of EPS, customers and reviewers criticised the poor steering feel, especially vagueness around the centre position. I guess these issues have now been cleared-up?
Charlie Cregeur: There are many articles in the press referring to the great strides that have been made in improving the performance of EPS systems to match the overall handling and feel compared to hydraulic systems. One of the big advantages of EPS is that the actual tuning of the steering system can be done when the car is on the test track through tunable software parameters versus having to take the car back to the garage, remove the steering gear and physically make changes to the valve shape which can sometimes take several days or weeks to achieve.
just-auto: The electrical power required for EPS has limited the system’s usage mainly to smaller vehicles, i.e. part of the issue with a 12-volt system is getting enough instantaneous power to have a full electric power steering for a large car. Forsaking the emergence of 42 volts, are there any advancements being made in respect of applying EPS to large vehicles?
Charlie Cregeur: There are many parameters that define the ‘signature’ of a steering system, but in terms of system type selection the “C” factor is one of the most critical. C-factor is the ratio of how far the ground wheels move in relation to one full revolution of the hand-wheel. The higher the C-factor the more energy it takes to create the necessary force to move the ground wheels rapidly. As the front axle weight of the vehicle increases, so does the amount of energy to maintain a given C-factor. When an electric motor is trying to drive a large load with a typical 12-volt power system, the current draw from the battery and alternator can reach well over 100-amps. If not properly managed this can lead to voltage drops on the vehicle causing dimming of lights or other noticeable impacts. By increasing the supply voltage to the EPS, the current draw can be reduced accordingly and thereby reduce or eliminate these impacts. Some vehicles have been put in the market where the steering system creates or is supplied with an artificially higher voltage like 24- or 42-volts to provide the extra power. The downside to this is the cost of the voltage converter itself.
There is a second trade-off the OEM needs to make when choosing between EPS CD and EPS RD. When CD is fitted to a vehicle it changes the cross car beam structure and safety strategy of the vehicle. As the size of the CD system increases, it causes the components of the system like the gearbox, motor and intermediate shaft to grow in size and weight. This changes how the crash structure of the instrument panel is handled. One key advantages of the CD is that it is physically housed in the passenger compartment of the vehicle away from the high heat and harsh under-hood environment.
By comparison, a rack drive system is typically positioned between the engine/transmission and the forward passenger cabin wall. In this configuration, the beefing-up of the cross car beam is not required as with a CD system. Space, however, is a premium behind the engine causing the vehicle and steering system designers to have to trade-off how best to fit the RD system in the available space and yet keep the electronics away from the extreme temperature environment of the catalytic converter and exhaust system.
just-auto: What is the interest in EPHS systems for hybrid vehicles?
Charlie Cregeur: EPHS allows a standard HPS fitted vehicle to be converted to a hybrid vehicle with minimal impact to the steering system. If properly configured, the same steering gear can be used for both EPHS and conventional mechanical pump HPS systems. Since many hybrid vehicles are run in low volumes, it is a much quicker and less costly route to market for OEMs to convert a HPS fitted vehicle to become a hybrid. TRW has EPHS on a hybrid production vehicle in North America this year and other platforms under going performance testing in the US and Asia.
just-auto: Despite early predictions of electro-hydraulic steering being a transitional technology, it looks as if it is here to stay, albeit for the foreseeable future.
Charlie Cregeur: For larger vehicles to achieve CO2 reductions, EPHS is one of the best value options for OEMs. Until the time EPS systems are able to achieve the same range of rack loads as EPHS, there will be an EPHS market. Delivery vehicles are one of the emerging markets for EPHS to meet CO2 requirements.
just-auto: Is there an appetite for EPS in the emerging countries?
Charlie Cregeur: Emerging countries do like to leap straight to the state-of-the-art but are tempered by affordability. As EPS technologies mature and volumes increase we expect to see the price of EPS systems decline and become increasingly more affordable for emerging countries.
just-auto: To some extent, EPS systems are pushing hydraulic steering-assist systems off the road. How do you see the hydraulic steering sector evolving over the next few years?
Charlie Cregeur: Our market estimates indicate that by 2011 EPS fitment in Europe will surpass HPS. CO2 regulations will play a major role in the speed of that transition. There is likely to be an HPS market in Europe for many years to come albeit the size of the market will be influenced by many factors.
just-auto: We’ve seen how your EPS system has become very popular among automakers. Technically speaking though, what’s in the pipeline, i.e. next generation?
Charlie Cregeur: For the next decade the market will continue to increase fitment of EPS and will strive to have large segment vehicles matching the performance of the lower end B and C segments. OEMs will add more functionality to steering systems thru software algorithms that can for example help offset the effects of side-wind forces on the vehicle, suppress some hand-wheel vibrations due to chassis components and enable higher fitment rates of marketable features like park assist.
just-auto: Do you foresee drivers being able to adjust steering like current suspension settings?
Charlie Cregeur: It is quite easy to adjust the steering system to the driver’s preference. Vehicles can be fitted with a switch on the dash to set the steering feel and in some premium level vehicles with keyless entry, the security system can identify the driver and tell the steering system how to set the steering feel. This is all possible today.
just-auto: Could we see more design integration of braking, steering and suspension? Do you see an even stronger link with advanced driver assistance systems?
Charlie Cregeur: There will be more and more integration between steering, braking and passive restraints as time goes by. For this reason TRW began its Cognitive Safety programme to lead the market in multiple system integration. We see further opportunity on the vehicle to incorporate features like blind spot detection and lane guide to help the driver operate the vehicle with a higher degree of safety and confidence. TRW’s Adaptive Cruise Control [radar] and forward-looking camera technologies are additional integration options that are being fitted by leading OEMs. It’s clear the OEMs do not want to add more ‘black boxes’ to the vehicle but prefer to figure out how to get more functions by the existing subsystems working together.
just-auto: Are there other approaches being developed that use advanced electronic techniques? What about rear wheel steering perhaps supplemented by ultra-capacitors coupled with improvements in sensors, power and control?
Charlie Cregeur: Rear wheel steering is a technology that is known in the market and to TRW. While an interesting feature in the passenger car market, rear wheel steering has never really reached critical mass anywhere in the world. TRW also has experience with rear wheel steer on large over the road commercial vehicles. In fact, we are seeing the migration of light vehicle steering products into the heavy truck market. For example, TRW is supplying its EPS CD to recreational vehicle manufacturers to have the ability to improve the comfort and handling of these types of vehicles in high wind situations. The EPS system in these vehicles is in addition to the standard heavy duty truck steering system.
TRW and the rest of the steering supply market are continuously looking for ways to reduce cost and increase functionality in our products. Higher levels of integration between subsystems and within the subsystems themselves will be a trend that will not reverse.
About TRW Automotive
TRW Automotive is one of the world’s largest suppliers of electric steering systems. The company currently supplies more than 30 vehicle models worldwide with millions of systems shipped annually. The company operates three business segments: Chassis Systems, Occupant Safety Systems and Automotive Components. The company’s steering system business falls under the auspices of its Chassis Systems segment. This segment generated sales of US$7,997 million in 2007, or 54% of total sales. In addition to steering systems for passenger cars and commercial vehicles, TRW Automotive designs and produces braking systems, driver assist systems, inflatable restraint systems, steering wheels, seatbelts, safety electronics, tyre pressure monitoring systems, security electronics, engine components, fasteners and body control systems. The company also serves the aftermarket with a variety of products. More specifically, TRW’s steering system product range includes power and manual rack and pinion steering gears, linkage systems and components, electrically assisted steering systems, such as electrically powered hydraulic steering and electrically powered column and belt drive steering systems. The company serves the OE and aftermarket.