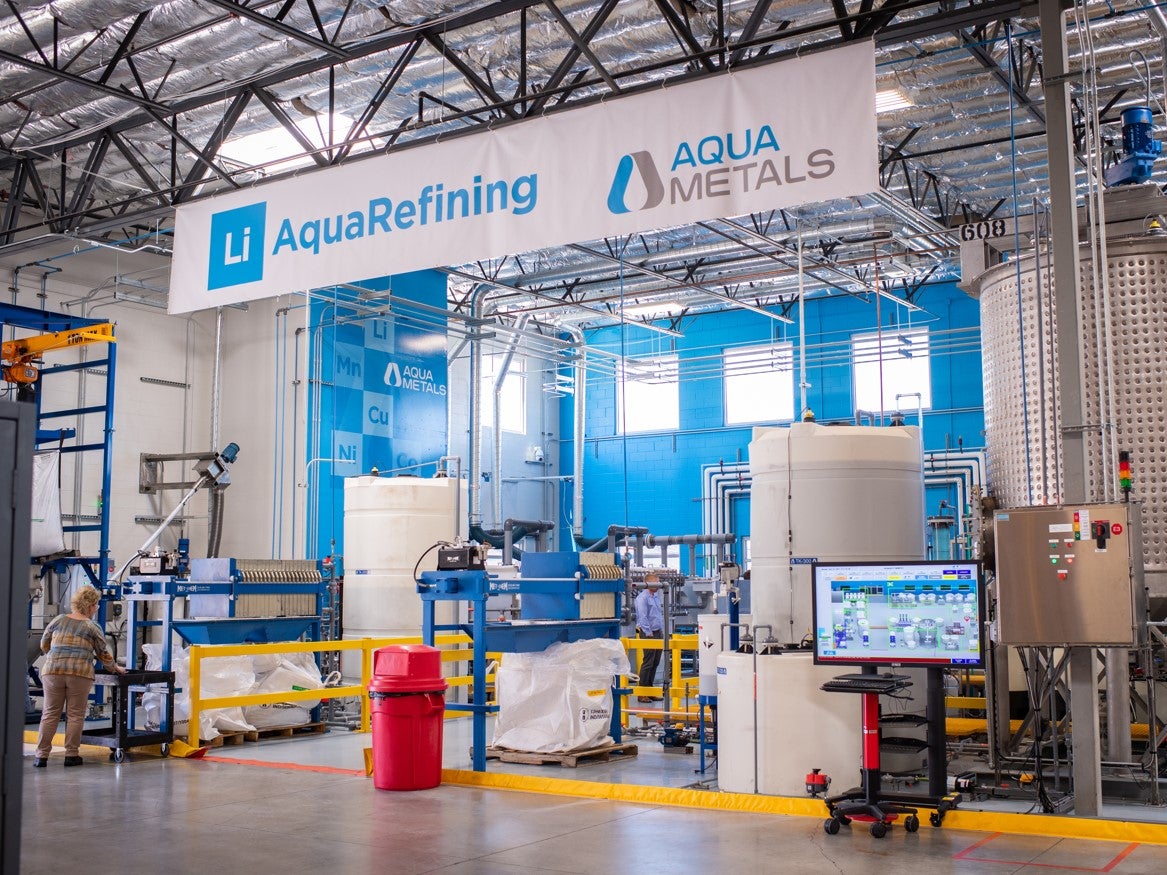
The electric vehicle (EV) industry is facing emerging challenges in the shape of lithium battery recycling capacity and China announcing that it will limit the export of graphite needed for EV batteries.
In light of this, sustainable battery recycling is attracting more attention.
Clean recycling innovator, Aqua Metals, says it is pioneering with its sustainable battery recycling process. The company operates what it describes as the first-ever sustainable battery recycling facility and is in the process of developing a commercial-scale ‘recycling campus’.
We spoke to David Regan, VP of commercial, Aqua Metals, to learn more about the recycling process and its benefits.
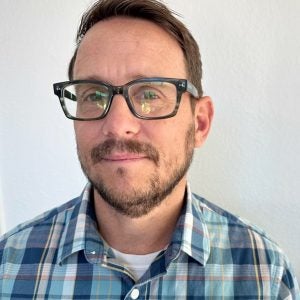
Just Auto (JA): Could you provide a little bit of the background on the company?
David Regan (DR): Aqua Metals is a pioneer in sustainable battery recycling technology and has developed an electrified approach to recovering the valuable metals and minerals that make up various types of batteries.
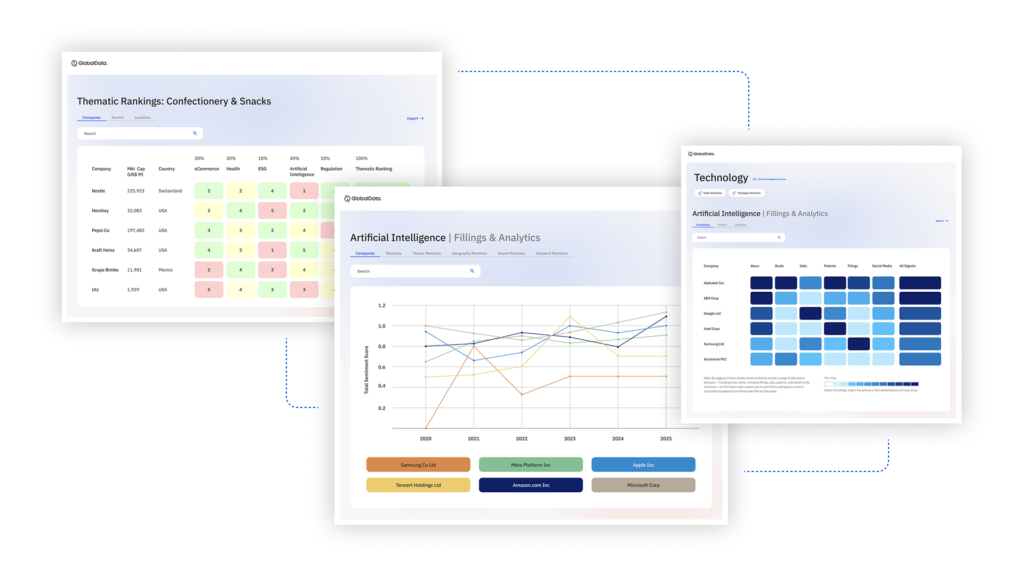
US Tariffs are shifting - will you react or anticipate?
Don’t let policy changes catch you off guard. Stay proactive with real-time data and expert analysis.
By GlobalDataThe company was initially focused on sustainably recovering materials from spent lead acid batteries using electricity in an innovative process similar to electroplating.
We found great opportunity, however, in the relatively nascent lithium battery recycling sector and quickly pivoted before a similar immoveable infrastructure might take effect. We’ve refined our technology to meet the needs of automotive and other customers and help set what we hope will be a standard of excellence in truly sustainable EV battery recycling technology.
How does the battery recycling process carried out by the company work?
Unlike any other available process, we use clean electricity to extract metals, instead of melting down batteries in polluting furnaces or extracting them using trainloads of consumable chemicals.
The basic steps of recycling lithium batteries using Aqua Metals’ proprietary AquaRefining process go like this:
Batteries are collected, discharged, and shredded into a mixture of metals the industry calls ‘black mass.’
Unlike any other available process, we use clean electricity to extract metals
Aqua Metals then receives that material, and dissolves the valuable metals into a solution of roughly 85% water and 15% acid (with a pH similar to cola).
Graphite and other materials (like aluminium, steel) are recovered from the solution with a filter press for further processing.
That solution is then passed through a series of electrochemical cells tuned to harvest a specific metal (nickel, cobalt, manganese, copper) using electricity to electroplate it out of the solution.
Lithium is recovered as either lithium hydroxide or lithium carbonate to suit the specific manufacturer’s specifications.
Each metal is recovered at high purity, without the need for high temperatures and without generating multiple tonnes of waste that must be sent to a landfill. This dramatically reduces emissions associated with recycling. Since it is powered by electricity, we can source carbon-free energy and drive towards net-zero lithium battery recycling.
What are the benefits of this process?
AquaRefining enables a more economical recycling process due to its ability to produce high purity metals from which battery precursor materials can be made, and the closed-loop use of chemicals reduces costs and eliminates waste run-off.
Current recycling methods create far more climate pollution and waste than valuable recovered material – which can hardly be called recycling, when the primary thing produced is pollution. Removing the emissions and waste burden from recycling is critical to creating a truly circular supply chain for critical minerals, and that is why Aqua Metals developed an electrified solution.
Our approach delivers raw materials back into the manufacturing supply chain and can effectively keep the same metal in circulation for generations.
How can the industry build a circular and sustainable supply chain for battery components?
As climate regulations tighten and incentives for low-carbon battery materials continue to grow, we believe the market potential and demand for a circular and sustainable supply chain will continue to expand. Over time, we also expect regulations and standards to continue to increase – not just for one’s own emissions, but also accounting for the emissions of a company’s suppliers and whole supply chain.
As climate regulations tighten and incentives for low-carbon battery materials continue to grow
It cannot be overstressed that sustainable innovation with thoughtful scaling and thoroughly tested technology is imperative to establishing a thriving, circular supply chain for EV battery metals.
In that climate-conscious future, recycled materials will be in highest demand, due to their very low carbon footprint and ability to be ‘urban mined’ or extracted anywhere that is convenient to the battery supply chain.
To create something truly circular and sustainable, battery manufacturers, EV companies, and other OEMs will be looking to purge carbon emissions and waste from their supply chains, and recyclers will need to lead the way in driving down emissions to be successful in the future.
What do you think the future holds for the battery industry?
According to the US Department of Energy (DOE), less than 5% of lithium-ion batteries were collected and recycled in 2019. The DOE estimates that recycled material could “provide one-third of United States cathode material needs for lithium-ion batteries by 2030”. The number of EVs sold in 2019 alone could result in 500,000 tons of battery waste when they reach their end of life.
The global market for lithium-ion batteries is accelerating at a meteoric pace, with demand for new electric vehicles leading the way. Along with that, the availability of end-of-life batteries and manufacturing scrap materials is quickly rising. The global lithium battery recycling market is roughly $5 billion today and is expected to grow five-fold to nearly $25 billion in 2030. The rapid domestic scale-up of battery manufacturing will serve as a primary source of recyclable material for the coming years.
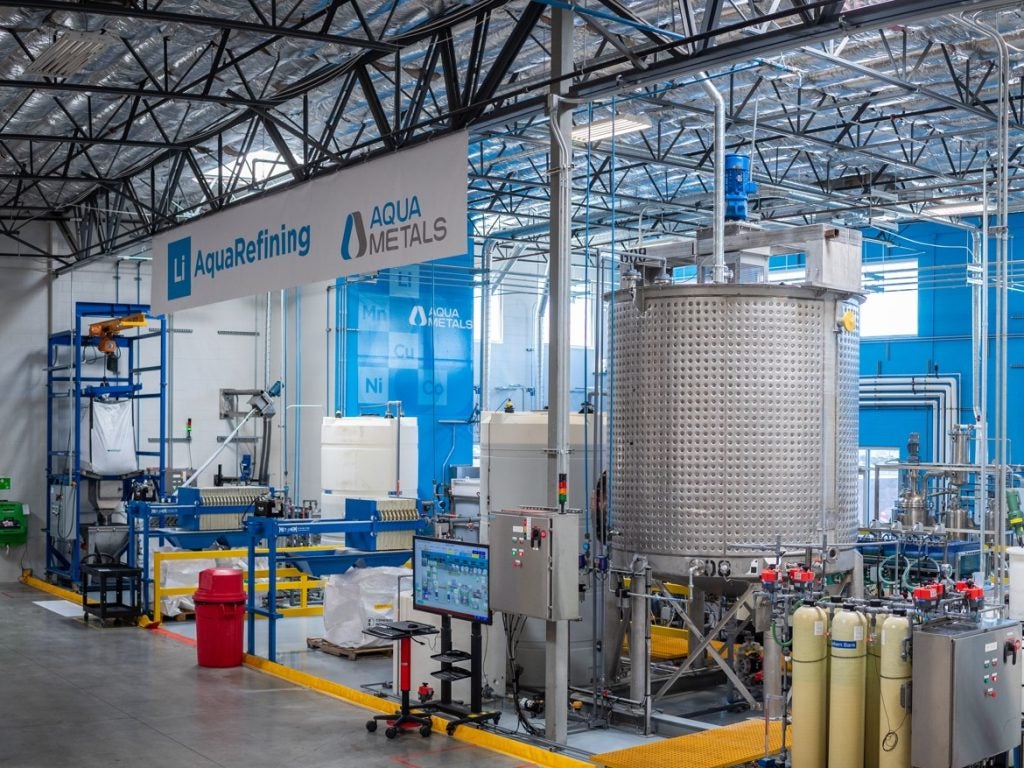