This year marks a step change in the F1 regulations. A raft of aero and powertrain rules are set to create a more efficient race car with more direct links to road car technologies. V8s, used since 2006, will be replaced by all new 1.6 litre turbo charged V6. Engines are now also referred to as ‘power units’ thanks to the increased hybrid nature of their power generation. As track testing of this new ‘turbo’ and what some describe as an ‘energy efficient’ era, one supplier to the F1 teams talks about the impact of the rules on its business and how it is responding to the challenges. In this interview, Matthew Beecham spoke to Terry Graham, managing director of Zircotec, a supplier of thermal management products and heat protective coatings.
We have just witnessed the first race for the new cars. Can you summarise some of the key changes for the power unit?
Yes, the key change in that respect is the power unit architecture. Out go the 2.4 litre naturally aspirated V8s, replaced by a smaller capacity 1.6 turbocharged V6 engine with a fuel limit of 100kg, that’s about 130 litres. Eight speed transmissions are to be introduced, partly to cope with the rises in torque with the hybrid aspects of the unit. KERS, the kinetic energy recovery system used since in the sport since 2009, is now called ERS-K (Energy Recovery System Kinetic). It now has twice the power output and five times the energy storage of the previous system. In addition to this we have a new system called ERS-H. This stands for Energy Recovery System – Heat) and it is mounted to the engine’s turbocharger. The ERS-H can spin the turbo up itself to reduce lag or deliver recovered energy back to the engine via the ERS-K. The complexity and heat aspects of the new power units make this extremely relevant to Zircotec and our technologies to manage heat in harsh environments.
We have been working closely with F1 designers and engineers to find solutions for a period of time but once the cars hit the track, then other issues tend to appear. We are ready for this and have a night shift ready for the past few months to be able to turn parts around in the same day. In fact up to the first race, our work for F1 teams has doubled compared to last year. With the cars now running on track in the races, more technical challenges are coming to light and we are working with the teams to help them claw back reliability.
Why are coatings such as those from Zircotec favoured in F1?
We continue to offer a robust, lightweight coating that offers a competitive blend of weight and thermal protection. As a plasma-sprayed coating we can be installed where heatshields or lagging cannot be fitted because they are simply too bulky. By being much thinner, typically 300-400 microns, we can offer engineers an air gap around the part too. Packaging is one area where the teams have had to work really hard for this year and going back to the road car analogy; this has been equally a driver in more recent projects.
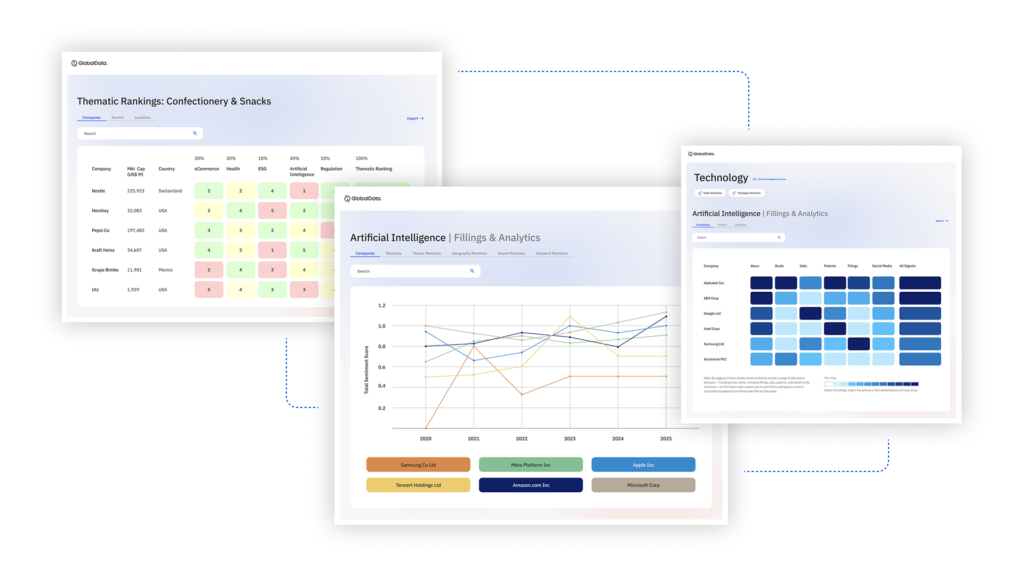
US Tariffs are shifting - will you react or anticipate?
Don’t let policy changes catch you off guard. Stay proactive with real-time data and expert analysis.
By GlobalDataGoing back to F1 though, previously the original ERS-K was fitted to the front of the engine. The 2014 unit is around twice the size and so has to fit alongside the engine, close to the exhausts. We can offer protection from the heat in this instance by either coating the exhaust or the ERS-K parts. The ERS-H on the other hand sits close to the hot turbo. We already coat turbos for performance road cars to keep heat inside. Keeping the turbo hot improves responsiveness and reduces lag as well as the thermal protection afforded, though we feel the issue of lag is not going to be a problem in F1 because the ERS-H can be used to solve this. By coating the turbo, we can make the most use of the heat for the ERS-H. It’s going to be a challenge; the turbo spins at around 100,000-125,000rpm. There are lots of heat issues to consider with that level of friction. We don’t have all the answers but we do have technologies we know can help.
Will all of these devices result in more power or more efficiency than we have today?
Both are the aspiration. The ERS-K produce around 150kw for 30 seconds and the energy recovered from the waste heat is currently unlimited. Estimations suggest overall power will be around the same level as 2013 but nobody is saying exactly what power they are getting yet! Certainly the aim with the limit of fuel is that cars will burn less fuel than in previous seasons.
You are known for your exhaust coatings and as I understand this is core part of your road car business. Will you be coating exhausts in F1 this year?
Exhausts are now much more strictly controlled but our experience of keeping heat inside the pipe is still very relevant and we do have some work for these parts. Whilst the demand to keep gasses hot to blow through the diffuser, you may remember this as a key performance gain on 2009 and subsequent seasons, has now gone with a central exhaust position mandated, a coated exhaust can help reduce heat transfer to other sensitive locations such as bodywork. We can coat ‘patches’ of the exhaust, perhaps where it runs close to a sensitive component or the bodywork. By coating only sections of the pipe or by varying the thickness of the coating, we keep the weight down to a minimum too.
Motorsport is often cited as a breeding ground for new technology or the starting point for technology transfer to road cars. Is this the case with these technologies?
Yes, our patent protected ThermoHold for Composites coating has already been used with success on the Aston Martin One-77 and we have another composites road car project at the moment. F1 has been an extremely robust environment to prove our technologies – providing a compelling application for our OEM customers. Our ZircoFlex flexible heatshield, used by many F1 teams is now being used by a volume manufacturer to solve a heat issue in a mainstream vehicle. This strategy is successful and our next innovation that has come from our F1 work that may well interest OEM customers. With the growing use of carbon fibre in electronics systems, we have been helping teams to improve their EMC (electro-magnetic compatibility) interference. We can now produce a highly conductive surface coating for both composite materials and plastics. This coating improves the EMC performance for items such as junction boxes and enclosures.
Do you see an OEM use for such a technology?
The remainder of this interview is available on just-auto’s QUBE materials research service