Continuing our series of interviews with global component manufacturers, Matthew Beecham talked with Nigel Seeds – Technical Fellow, Powertrain Cooling, Visteon and Bernd Kirmse – Marketing, Climate Control Systems, Visteon about trends in powertrain cooling systems.
In what ways has the scope of thermal management changed over the past decade?
Nigel Seeds: We are all probably aware of the trend over past years of downsizing for fuel economy benefits. This has paved the way for an increased use of boosting technology using turbochargers, superchargers or a combination of both to compress the intake air and increase power outputs from smaller displacement engines. The downside of compressing the intake air is the resulting increase in temperature and this requires a Charge Air Cooler (CAC) to reduce the temperature whilst trying to minimise pressure loss and maintain density. Whereas ten years ago, CACs were only really seen on some of the higher output diesel and performance vehicles, mainstream passenger vehicles are now requiring some form of charge air cooling, either using an air-cooled or water-cooled CAC. In either case there are additional heat exchangers that need to be packaged in the vehicle compared to a normally aspirated powertrain. Extra heat exchangers imply larger package envelopes, making the front end cooling pack larger and heavier. This is in contrast with the requirement to reduce package for front end crash and pedestrian impact and reduce weight for fuel economy improvements. All these factors need to be considered in the design scope when sizing a new cooling module for an OEM.
The thermal management of the engine is also receiving a lot more attention recently. The acceptable levels of emission (CO2, NOx etc) are constantly being driven lower by legislation. Using higher rates of EGR, both High Pressure (HP-EGR) and Low Pressure (LP-EGR) is one way of achieving the target emissions. With LP-EGR the gas is fed back through the CAC and the acidic content of the condensate presents new challenges to the materials used in this heat exchanger.
Visteon launched the first generation EGR cooler in 2004 and since that time has seen the volumes increase. In April 2012 a major milestone was passed when the ten millionth HP-EGR cooler was manufactured and delivered. Over these eight years the yearly volumes have continued to grow and Visteon has recently been sourced on two new EGR products due for launch in 2014.
Another area that is being considered recently is that of heat recovery. Visteon has been working on methods of using the waste heat from the exhaust system to replace PTC elements in the HVAC for improved cabin comfort and accelerate engine warm-up using an Exhaust Heat Recovery System (EHRS). This could be used in combination with a Heat Storage Unit (HSU) that has been in development since 2010. This simple and cost effective latent HSU, which can also be fitted as a stand-alone unit, uses phase change material to store heat which is then used to reduce the engine cold-start period considerably and hence improve fuel economy and emissions. Tests have demonstrated a potential 3g CO2 reduction per km and fuel efficiency improvements of 0.1L/100km could be realised.
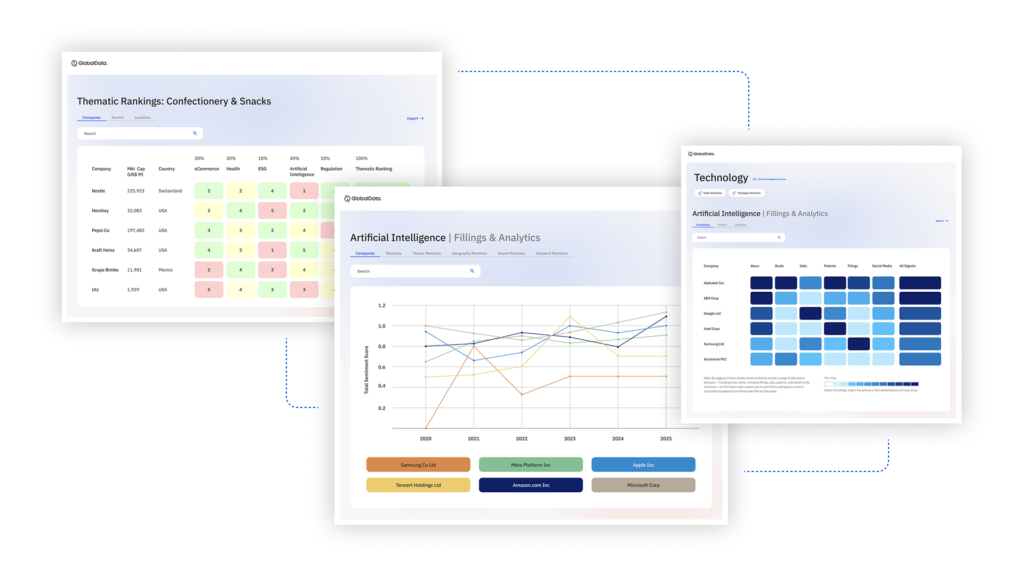
US Tariffs are shifting - will you react or anticipate?
Don’t let policy changes catch you off guard. Stay proactive with real-time data and expert analysis.
By GlobalDataDespite the stricter requirements being applied to internal combustion engines to make them more fuel efficient it appears that diesel and gasoline powertrains will still continue to power a large percentage of passenger vehicles over the next ten years. However, alternative methods such as hybrid, EV and fuel cell technologies will certainly continue to grow. These alternative powertrains provide a different set of challenges in terms of thermal management and it is important for Visteon to provide cooling solutions for both internal combustion and alternative fuel powertrains.
As we understand it, there has been a shift in emphasis from the previously predominant direct charge air cooling to indirect charge air cooling assisted by the coolant. What has driven this change and what are the benefits?
Nigel Seeds: Indirect charge air cooling assisted by coolant – or water-cooled charge air cooling, WCAC, as we call it – has been around for a long time but it was only really considered on high performance vehicles. Whilst it is still the case that a WCAC system is common on high performance vehicles, it is also gaining acceptance for use in mainstream vehicles shifting away from a direct air-cooled CAC which would be mounted in the front end air stream of the vehicle.
One of the original drivers for WCAC was the improved throttle response and drivability of the vehicle. By placing the WCAC close to the compressor outlet and intake manifold (in some cases physically integrating the heat exchanger in the manifold) this removes the large diameter and lengthy charge air ducts that would have been used to transport the charge air to an air-cooled CAC mounted in the front end. This means the WCAC system has a lower compressed volume of air and also lower pressure loss.
The package space that an air-cooled CAC occupies in the front end cooling pack can result in restricting the cooling air flow and therefore having a negative effect on other heat exchangers such as the radiator or air-conditioning condenser. This often means that all the components have to use deeper cores or larger face areas to provide the levels of performance required. This opposes the latest crash and pedestrian impact requirements which are calling for smaller heat exchanger modules that occupy less depth in the engine bay. By using an indirect WCAC system a low temperature radiator (LTR) is still required to be mounted in the front end airflow. However, the LTR is typically not as deep as an air-cooled CAC so offers packaging advantages, particularly when it enables the use of a full face LTR which will offer higher thermal efficiencies at low vehicle speeds.
The important thing to note is that a WCAC needs to be sized and matched with a suitable low temperature radiator design in order to optimise the performance and package. Visteon’s portfolio of heat exchangers includes a large range of standard core thicknesses that provide design flexibility to best meet customer requirements and we have also developed tools that enable the WCAC and LTR system to be sized and optimised.
There are certain drawbacks associated with indirect charge air cooling compared to a direct system. As a 2-stage heat transfer system it does require an additional heat exchanger. It also requires a coolant circuit which subsequently needs a coolant pump. These are sometimes viewed as expensive items and result in an OEM continuing with the more traditional air cooled CAC. However, Visteon has seen a significant growth in WCAC business over the past five years and it is estimated that indirect charge air cooling systems will continue to grow steadily over the next few years.
In terms of commercial vehicles, what are the challenges there as far as powertrain cooling is concerned?
Nigel Seeds: The typical usage profile of a commercial vehicle means it spends a lot of time on the road and in the case of a delivery truck spends a large amount of time at low speed or idle. The severity of these duty cycles and minimal air flow presents a challenge in terms of powertrain cooling although they are not too different from what is now being seen on some passenger vehicles. The durability requirements of components such as the radiator and CAC are typically more severe with design verification tests being specified at higher pressures with increased number of cycles to failure.
Commercial vehicles do not escape the challenges associated with legislations and EU6 applies to new light commercial vehicles from September 2014 (September 2015 for those above 1305kg). To meet the tougher emission requirements manufacturers tend to adopt one of two systems: Selective Catalytic Reduction (SCR) or Low Pressure Exhaust Gas Recirculation (LP-EGR). Whilst the SCR reduces the NOx after it has been produced, the LP-EGR reduces the levels of NOx being produced. LP-EGR does offer challenges for some of the other components in the system in particular the charge air cooler (CAC). Because the LP-EGR gas is fed back upstream of the CAC this heat exchanger is now exposed to the acidic environment associated with the gas. The CAC core development team at Visteon has been investigating and carrying out tests as well as working with both OEMs and material suppliers to understand the effects of acidic corrosion on the component parts of the CAC and ensure the parts offered are robust.
Moving away from the internal combustion engine to the electrified powertrain and lithium-ion batteries, what is the trend there?
Bernd Kirmse: Powertrain electrification (hybrids, plug-in hybrids, electric vehicles with or without range extender) are important elements to reduce overall fleet average CO2 emissions. The key enabler is the battery technology to allow compact and powerful electrical storage devices which are easy to use (e.g. charge time, drive range) and come at affordable cost.
Which cooling concept will gain acceptance for lithium-ion batteries? Cooling based on refrigerant or coolant or air?
Bernd Kirmse: The different types of lithium batteries are today the battery technology of choice with numerous advantages over the NiMH (nickel metal hydrate) batteries of earlier electrified vehicles. The downside is the temperature sensitivity – for optimum performance and durability lithium batteries require good thermal management at peak temperatures below those of hot summer days. A/C cooled air is an option but by using contact heat exchangers we find we can control the battery cell temperature more precisely and in a more compact system. Heat transfer is done here via conductivity in direct contact.
It is depending on multiple factors on the vehicle and battery system level if this contact heat exchanger is directly part of the refrigerant system (where refrigerant runs through the heat exchanger) or if it is indirectly connected – using a chiller to cool a water/glycol mix which then runs through the contact heat exchanger.
It is necessary to know the engine in order to cool it. Does the same principle apply to battery cooling?
The remainder of this interview is available on just-auto’s QUBE research service