There is a practical limit to braking performance, set by the ability of the tyre contact patches to transmit the forces involved without sliding. However, advances in tyre design, soon to be complemented by the ability of electronically controlled braking systems to distribute effort according to wheel load, mean that limit is now potentially very high, at least on dry road surfaces. This is throwing the onus very much back on the braking system developers. In this interview, Matthew Beecham talked with Vince Austin, director, global braking systems for TRW, about foundation braking systems.
j-a: What are the forces driving innovation in foundation braking for passenger cars and light trucks? Are those drivers the same for every car segment?
Vince Austin: There are different forces driving innovation for each car segment. For example, low cost and low drag at acceptable performance are the main drivers for low/small segments. Whereas for medium segment vehicles the key is low drag and best performance at acceptable cost. In terms of the high end segment the focus is on lowest weight, low drag and best performance at acceptable cost.
In addition, ‘low noise’ has become a very important driver and this is the case for all the segments. Even customers who for many years did not consider noise as a point of focus now have very challenging targets to meet in this area.
j-a: To what extent do those drivers change when looking at the developing regions, such as India?
VA: Emerging markets are looking for base technology, and because of the segments and driving habits, high-tech brake performance is not required at this point. Therefore, they are looking for base foundation brake technology such as single front callipers and rear drum brakes. There are some vehicles fitted with ABS, but fitment is expected to remain low in the absence of government regulation.
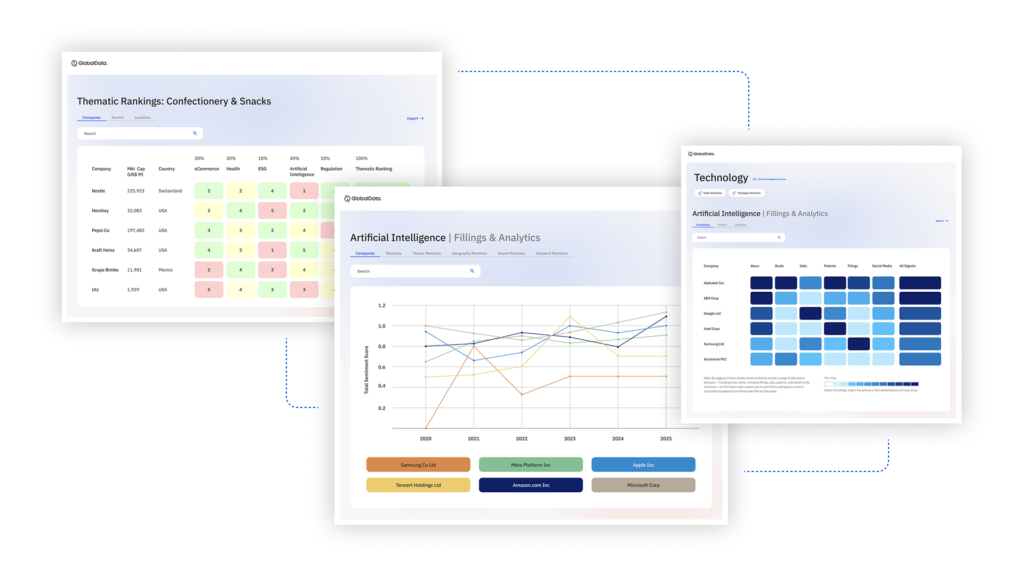
US Tariffs are shifting - will you react or anticipate?
Don’t let policy changes catch you off guard. Stay proactive with real-time data and expert analysis.
By GlobalDataj-a: For reasons of low cost and ease of maintenance, I guess the developing regions still use drum brakes. Is that correct?
VA: Drum brakes remain the preferred ‘rear brake’ technology of choice for the small vehicle segments. We are seeing some drum brakes fitted on the front axle of small, low-cost cars such as the ‘Tata Nano’, but this is a rare exception. The primary path is discs for the front and drum brakes for the rear.
j-a: To what extent is there a focus on providing flexible technology platforms that save time and cost for low and medium-volume applications?
VA: The main focus is on design reuse and standardisation of components and manufacturing equipment.
j-a: In what ways do hybrid and electric vehicles change future braking system requirements?
VA: From a foundation braking perspective, nothing changes. From a brake control perspective, we have to be able to blend friction braking with regenerative braking for strong hybrids. TRW offers two systems – SCB (in production in the US), a vacuum-less hydraulic system; and ESC-R, which can be vacuum-based (for mid-upper segments) or vacuum-less (for small segments). As a hybrid or electric car does not have background noise, which can mask brake noise, there are also new NVH requirements to expect.
j-a: I guess reducing stopping distances and weight reduction will always be a priority when it comes to design and development of braking systems yet to what extent is improving the brake feel important?
VA: For some vehicle manufacturers pedal feel is part of their corporate identity; as such improving and maintaining brake feel is of utmost importance. Usually attention to pedal feel grows with the segment from low to high.
TRW’s FBC calliper on the brake system of the Audi A4/A5 has had very good reviews, with a particular emphasis on the performance and feel of this brake system.
j-a: As I understand it, the use of electronic controls has tended to simplify and modularise the construction of braking hardware. To what extent has the previous mechanical improvements to the brake system hardware now been replaced by firmware or software designed to accomplish the same or better functionality?
VA: The use of electronic controls has not necessarily simplified or helped to modularise the construction of foundation braking hardware. From a braking and stability control perspective, improved electronics has resulted in better performance and it has also led to advanced braking functionality such as automatic emergency braking or adaptive cruise control.
j-a: As far as trucks and buses are concerned, high frequency brake squeals are commonplace. Could you draw on an example where you have made some improvements in that area?
VA: The squeal behaviour of a brake depends strongly on rotor and suspension. That is why each application needs some NVH work, in order to tune the dynamics. Based on vibration analysis and also numeric simulation, carrier and/or housing geometry are modified in order to eliminate brake noise. High frequency noise is strongly related to pad/rotor interaction. Pad chamfers and damping shims are common noise fixes.
j-a: In terms of brake disc materials, in what ways have these materials advanced over the past five years?
VA: In terms of the material of choice, grey cast iron tends to be preferred due to its robustness, thermal performances and cost. There are some high-end ceramic discs on the market today, but these are still considered ‘exotic’ and do not tend to match up on robustness and price.
j-a: I guess there is a practical limit to braking performance, set by the ability of the tyre contact patches to transmit the forces involved without sliding. However, I guess advances in tyre design mean that limit is now potentially very high, at least on dry road surfaces. Is that throwing the onus very much back to the braking system developers? How will tomorrow’s brakes perform?
VA: As long as the brake system has enough stopping power and rotor, and the pads have enough thermal load capacity then the brake system is usually not the limiter for stopping distance – the tyre is.