Malcom Powell is VP Vehicle Integration at Tesla Motors, the California-based technology firm developing an electric sports car that will be contract manufactured by Lotus in Hethel. He is responsible for the engineering of the car and ensuring that it meets all the necessary standards prior to entering production. just-auto’s Dave Leggett interviewed him in January on behalf of the Lotus Engineering magazine proActive where this article first appeared.
DL. When will those Tesla customers who have already put money down receive their cars?
MP: We’re still on plan for the first customer to get his car in the first quarter of this year.
DL. So when does series production start then?
MP: It depends what you call production. We’re doing a very controlled ramp rate, a prudent and sensible thing to do. We want to make absolutely sure that the production cars are working as anticipated and that the whole process and supply chain is working before we ramp up production further.
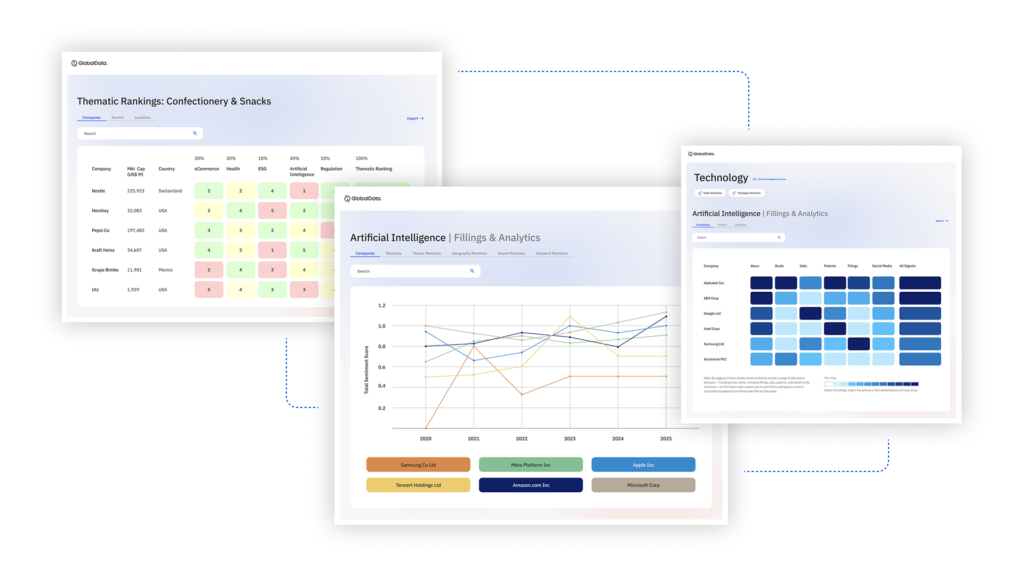
US Tariffs are shifting - will you react or anticipate?
Don’t let policy changes catch you off guard. Stay proactive with real-time data and expert analysis.
By GlobalDataThere is a danger when you ramp that you keep an eye on the big balls, but it needs all the balls to build the car; it’s no good having just 99% of the parts because you can’t build it. So we will control our ramp rate carefully. We will start producing the cars this quarter and we will monitor and ramp as quickly as we can, but under control.
DL. And what sort of volume are we looking at for the first year of production?
MP: It will be some hundreds of cars this calendar year – we should be running at around 600 for the Model Year.
DL. And building up to what level?
MP: We have always targeted the capacity to be able to build 2,000 cars a year. That’s because we have to have targets to choose appropriate tooling investment for the components. If the demand is absolutely extraordinary then we could choose to make more. It’s very difficult to predict exactly where demand will be on a new product such as this. We had to set a level that was achievable to fix our investment – and that was 2,000 a year.
DL: I understand the Tesla Roadster’s transmission has been a major source of delays to the programme schedule. What has been behind the problems in that area and how are the problems being overcome?
MP: You might think that a transmission is a known technology, particularly when viewed against all the new technology being incorporated into the car, but it’s not that simple.
As a new company it was difficult, initially, to get major manufacturers to even talk to us, never mind commit any resource to actually help design, engineer and build systems. We started off going down a particular route with a transmissions supplier and we got to the point where we realised that the way that particular programme was headed, it wasn’t really going to meet our performance targets for the car.
We chose, pretty late in the programme, to change course and go with an alternative supplier with a different approach.
The transmission sounds simple: two-speed transmission and therefore you depopulate a regular transmission, but if you think about it, our gear shift between first and second is a factor of two and the motor spins up to 13,000 rpm, so first gear takes you to over 60 mph and second takes you to over 125 mph so that is a huge ratio step against which we don’t have a conventional clutch. There’s a rotor with a very high inertia and we have to change the speed of that rotor very, very quickly to give us a performance shift.
There are also issues about electrical isolation because of the way we use the charging system and the motor.
So, it isn’t straightforward. It isn’t ‘just another transmission’ and some issues have been thrown up that weren’t anticipated and have taken longer than we had hoped to resolve.
With change of supplier, change of design concept and with some of these unforeseen technical issues to overcome, delays have been the result.
DL: Just following on from that, the first Tesla Roadsters are being fitted with an ‘interim transmission’ that can be upgraded later on. What are the performance implications of that? Will the first cars off the line be capable of doing 0-60mph in under four seconds?
MP: The point about the interim transmissions is that they will effectively be locked in second gear. A lot of the prototypes have been running like that for some time and the vast majority of customer drives have been done like that and the feedback has actually been that the car hits performance expectations in that state – it still does 0-60 in something like six seconds. So you’ve now got a rather interesting car that you can drive very rapidly from zero up to its top speed in one gear. I don’t think customers will be too disappointed.
The reason for the two-speed set-up was because the torque capacity of the motor and the power system was ‘X’ and to be able to say to the world ‘electric cars aren’t just golf buggies’ we needed the ratio to give us the four seconds and the top speed. In a single gear to begin with it would have done 0-60 in say 5.5 seconds with a top speed of 100 mph. That would have been fine, but we wanted to make it clear that we could deliver this sort of supercar acceleration and an acceptable top speed. That means two-speed shift – which is doable but it’s just a question of time and money.
It’s important to stress that we have had very positive feedback from customers about the second gear and that’s the only reason we’re doing this: many customers have said they would rather have the car now with the single gear and current level of performance than wait any longer. This is about satisfying customer demands to deliver before we get the full performance of the vehicle.
DL: Can Tesla’s lithium-ion battery fully meet acceptable performance parameters and will the battery last 100,000 miles – does it degrade over the lifecycle?
MP: Sure, they do degrade and it’s all about charge cycles. The battery manufacturers do the testing to determine what the battery capacity is. They fully charge, then fully discharge and keep doing that – it’s actually pretty abusive to a lithium-ion battery.
In the case of lithium-ion, keeping it charged up is actually a good thing to do – you don’t need to fully discharge them the way you need to with some other batteries.
The other thing is temperature control. That charge-discharge cycle that the battery manufacturers have to do is pretty abusive to the battery because of the temperature the battery gets to.
We are aware of all these things and we pay very detailed attention to the management of the batteries because that is so critical to what we’re trying to achieve.
How we charge them and what capacity we charge them to, and how we maintain temperature – because they are actively cooled within the car – is all about preserving battery life.
Most people don’t drive many miles on average each day – and we know this is not a road trip car – meaning they won’t be using a huge percentage of the battery pack each day. So, we say, when you get home just put the battery on charge and that will keep it in good condition.
If we take the standard fairly abusive battery charge cycles the battery manufacturers carry out, that implies driving say 200 miles in one stretch before recharging each time and that works out at 100,000 miles of life. And that’s with that rather unrealistic implied usage pattern. In reality, the battery should be good for more than 100,000 miles.
Also, the battery makers say that the battery life is over when it only achieves 80% of its original performance capacity.
So, there will be some degradation of range over the life of the battery. When new you will get over 200 miles range on a full charge but over time you will notice some degradation on that. But it will be a slow process and even under the extreme battery testing regime of full charge-discharge, that yields 100,000 miles with end of life deemed at 80% of original capability. Performance will also tail off slightly but when you start with 0-60 mph in 4 seconds, you’ll still have a pretty amazing car.
DL: In terms of readying the Tesla Roadster for production, what has been your experience in meeting US federal regulations in areas such as safety?
MP: It’s frightening and scary in terms of all the things you have to do, but it is also fairly straightforward. I’ve been in the industry a long time now and it’s a case of knowing what needs to be done and getting on with it. From the outset we knew we were designing for the federal market so things like headlamp design, crash testing and so on, were known factors. We just had to go through the process.
We have had to run certain rig tests on certain parts of the car because it does carry more weight than the Lotus Elise – the Tesla is significantly heavier. The uninitiated look at the car and say it’s the same as the Elise, where is all that additional weight?
Actually it’s not the same car. For example the crash structure at the front has new components in it that add load bearing paths and we have changed the aluminium chassis as well. Although the chassis is based on Elise technology it had to be changed in many respects, such as the fundamental siderails – these are a unique extrusion for the Tesla. The chassis is different. We have had to build significant reinforcement and strength in to those parts to control the mass of the battery pack as it is restrained during impact. The pack weighs over 900lbs – it’s a significant lump of mass.
The motor and transmission are relatively light and we don’t have to carry a fuel system, but fundamentally the car is a lot heavier than an Elise. The important thing is: we know all that and we have designed accordingly and have recently completed all the required safety and crash tests. We’re just getting all the final certificates in place that enable us to ship production cars.
DL: How does the supply chain work on the Tesla Roaster?
MP: Having chosen to work with Lotus as the contract manufacturer, we decided that there was no point in reinventing the wheel. We’re using the Elise structural concept, so anything we can carry over from the Elise makes a lot of sense. We, at Tesla, have enough to worry about with the new technology, without having to also worry about a lot of the other stuff that goes into making a car.
We have three categories of parts:
- Some parts are 100% Lotus carryover, things like the windscreen wiper. So we simply tap into the Lotus supply chain for them.
- Then there is a second category which are new design or modified parts where it still makes sense for us to use the Lotus suppliers. So Tesla has design responsibility but we use the Lotus supply chain to procure those parts and deliver directly to the plant in Hethel.
- And thirdly there are the totally unique Tesla designed and Tesla procured parts. This category includes some simple parts that the supplier can ship to Hethel for final assembly, but also includes more complex elements such as the motor, which we make at our dedicated plant in Taiwan where we do all the manufacturing, testing and then put it in box to ship to Hethel.
DL: How difficult is coordinating the manufacturing and assembly process?
MP: The fundamental logistics is fairly straightforward in terms of things like shipping. But as a new company it’s been a hurdle to get our own systems in place so that we know exactly where we are. We’ve had to develop systems from scratch. Not only have we been designing a fantastic vehicle that uses new technology but at the same time we have been building a company, developing news systems, training people for those systems and making sure that the systems are working correctly – all from a clean sheet of paper. It has been a big challenge.
In terms of what we have done in the time available it has been a very rapid programme.
There’s still engineering change going on now to resolve some final issues and improve the product. Unfortunately it’s engineering change that actually interferes with the supply process. Yes, it’s a challenge.
DL: What’s the current thinking on successor models?
MP: Tesla’s intent has never been just to make the Roadster, but the Roadster acts as a technology pioneer. It has already provoked the industry to take more note of electric cars. Great.
But the Roadster is not our only game. Our game is to get as many electric cars on the road in the world and cut our dependency on oil.
So for us it’s also about making more vehicles – such as a sports sedan so that we can appeal to a broader market. We have got to get the volume up so that we can start getting the price down. We have learnt a lot and we know we can improve still further with future product.
The next car has to appeal to a wider market, as does the car beyond that.
We are also up to talk to OEMs to see where we can help anybody else to do this because we do not intend to be the only people in the world making electric cars because that doesn’t provide a sufficient solution.
DL: For you personally, how has the experience working for Tesla been?
MP: I’d been at Lotus a long time and achieved a lot – and I enjoyed it – but I’d got to a time in my life when I was needing a different sort of challenge.
I never perceived myself as being particularly green. I think, like most people, I cared but wasn’t doing anything proactively about it.
When I got involved in Tesla and the philosophies behind it I was attracted. So many firms produce electric cars that you just don’t want to drive – but Tesla is about turning that on its head and producing a car that delivers performance, that you want to drive and doesn’t burn oil, so it is also good for the environment. And the idea is to force real change.
Technically it was interesting to me and morally I thought ‘yes, I could help to do something and why shouldn’t I get off my backside and actually make a difference?’
I was very lucky to be in a position where this opportunity came up. And I was in a position to help both Lotus and Tesla and act as a bridge between the two companies. Tesla needed somebody from the automotive industry – it was an ideal opportunity for me and a good fit for both companies.
For me it’s been a mixed bag. It’s been incredibly exciting and challenging and has meant working with a totally different group of people – so many of them not automotive, so they would challenge everything. Sometimes I would have to explain how the industry works the way it does, but sometimes the challenges would make me think ‘why do we do it that way?’
Sometimes you need that different set of people with different thought processes to just challenge what you’re doing and look for better ways of doing things.
That has been immensely rewarding.
The other thing I would say is that the nature of my role is to find problems, help teams resolve issues, keep the project on schedule as best we can. That’s my role and you don’t do that by looking at all the things that are going right – you look at the things that aren’t going as well as you’d hoped.
Continually looking at problems can be de-motivating at times and some days are worse than others. But if I sit in a prototype and go for a drive I think ‘this is why I am going through this pain’. It really is such an awesome car to drive and you realise the scale of the opportunity ahead for Tesla and everyone who wants to start thinking about electric drive.
We’ve just got to get there and we will get there – it just hasn’t been an easy road.
————————————-
Malcolm Powell
Throughout his career, Malcolm Powell has had the opportunity to drive some of the world’s most amazing cars – and what he found is that beauty and acceleration are no match for balance and responsiveness. Bringing with him the desire to make the driving experience more physically interactive and less remote, Malcolm oversees the integration of all constituent parts of a Tesla Motors vehicle, including packaging, testing, and legal approvals.
After graduating with a degree in mechanical engineering from the University of Sheffield in the U.K., Malcolm’s first job landed him in the research department of Westland Helicopters, developing a remotely piloted surveillance helicopter. He then moved on to Ford of Europe, where he worked in the Special Vehicle Engineering division on “fun” cars (think small cars, big engines, all-wheel drive). Prior to joining Tesla Motors, Malcolm established an automotive design consultancy and then completed a 17-year stint at Group Lotus PLC, where he managed development of the North American version of the Lotus Elise.
Leaving three adult children behind in the U.K., Malcolm and his wife now live in San Carlos, where they spend weekends hiking and cycling to explore their new environment. That is, once they’ve finished video conferencing with the kids back home.
This article first appeared in Issue 24 of the Lotus Engineering magazine proActive