Tenneco’s advances in exhaust heat recovery technologies include thermoelectric generators (TEGs) and Rankine systems for powering electrical accessories, recharging batteries and supporting vehicle propulsion without reducing engine performance. Tenneco reckons that the same trends that are causing the vehicle powertrain to become electrified are indeed causing its after-treatment systems to become electrified. Matthew Beecham spoke to Marcel Womann, Supervisor, Advanced Cold End Products, Advanced Engineering, Tenneco Clean Air Division about TEGs.
As we understand it, cylinder deactivation is an old approach to improving fuel economy that is currently undergoing a renaissance thanks to more sophisticated electronics and mechatronics being available on the market. What is particularly novel about your exhaust valve technology for both cylinder deactivation and acoustics? And in what ways does it address the new cold start legislation?
Electric valves provide a compact, lightweight and cost-effective solution for precise sound design and noise control in tailpipe applications, as well as adaptive exhaust control in vehicles featuring cylinder deactivation. Tenneco’s acoustic valve offers a unique functionality feature, where in the event of a power failure, the valve opens automatically via a return spring, mitigating any engine damage. This is the only electric acoustic valve in the market to feature such functionality.
In 2013, Tenneco’s electric valve was launched in an acoustic tuning application on the all-new 2014 Chevrolet Corvette Stingray and will be featured on three additional vehicle platforms by 2015.
We have heard it said that the last remaining major challenge for powertrain engineers is to do something about recovering the 30 percent of fuel that disappears as hot gases down the exhaust pipe. Is that correct? What is / can be done about this?
A major challenge for powertrain engineers is to gain more efficiency to meet future requirements like the 95gCO2/km request in Europe. In real numbers this means cutting the fuel consumption by approximately 30%. There are numerous technologies under development, which should help to increase the overall power train efficiency.
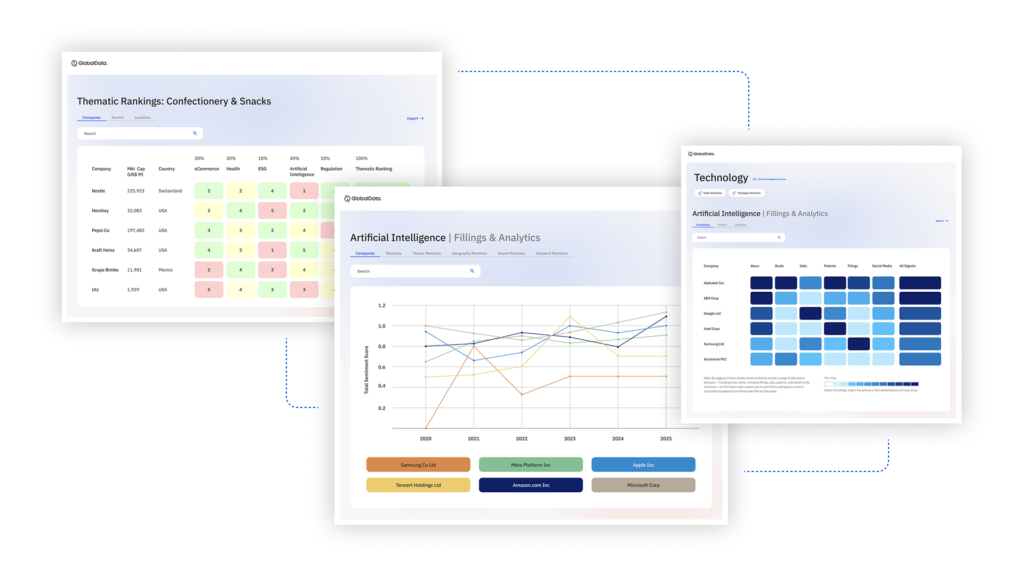
US Tariffs are shifting - will you react or anticipate?
Don’t let policy changes catch you off guard. Stay proactive with real-time data and expert analysis.
By GlobalDataWaste heat recovery is one of the approaches that presents a significant opportunity and will play an important role in the future. There are several waste heat recovery technologies in development that could be used to capture a portion of the lost energy and convert it to electrical or mechanical energy and redistribute it to the vehicle system, which can ultimately support improved fuel efficiency.
Tenneco is actively developing several solutions for waste heat recovery. Working with an industry consortium, Tenneco has applied its expertise in heat recovery technology and thermal management to optimise the design, validation and testing of thermoelectric generators for light vehicles. Partnering with Tenneco is Gentherm, a global developer of thermal management technologies for the automotive industry, and two global vehicle manufacturers. Tenneco recently showcased a prototype system last year at the Frankfurt motor show.
Rankine systems represent another technology that shows promise especially for commercial vehicle applications. Tenneco is currently in the process of integrating key components into a complete aftertreatment module to offer customers a compact and efficient solution.
I guess one solution is a thermoelectric generator (TEG) which can use virtually any heat source, including waste exhaust heat, to produce electricity using the thermoelectric effect. Given the infancy of the TEG market, there are a number of unknowns. But, in general terms, how do you foresee the market acceptance for TEGs in Europe?
There are many different technologies that range from improved aerodynamics and weight reduction via waste heat recovery and brake energy recovery to improved gear systems and hybridisation currently in development that can help to make vehicles more efficient.
Waste heat recovery technologies like thermoelectric generators and Rankine systems are promising technologies that could be ready for mobile applications after 2018 in the case of Rankine systems and after 2020 in the case of thermoelectric generators. As is common when new technologies are introduced, the operational performance criteria need to be addressed. For thermoelectric generators, the challenges for a broad application include improved efficiency in a wide temperature range, stabilisation of material properties to meet vehicle life time expectations and development of series manufacturing processes for thermo-electric material and modules that allows production at competitive costs.
Are TEGs likely to suit certain vehicle segments than others? What path do you see it following?
For passenger cars, it is reasonable to expect TEGs to be initially featured in the luxury vehicle segment, where the cost model and the customer expectations often support the adoption of new technologies. At the same time, waste heat recovery technologies like TEGs have a great potential benefit for future small- and mid-size vehicles to help meet future emissions requirements like the European 95g/km goal for 2021.
For heavy-duty vehicles, the principal benefits for utilising waste heat recovery technologies can be seen in fuel cost. This is one reason that Rankine systems show great promise for commercial vehicle applications.
Are there dimensional constraints / space limitations for a TEG in a vehicle?
Packaging is always a key consideration for vehicle OEMs. TEGs are designed to fit in a compact environment, similar to the size of a muffler. In addition, a TEG can reduce the exhaust gas temperature and provide some acoustic functionality, resulting in the potential reduction of the downstream exhaust system.
We understand that Tenneco is part of a consortium developing a TEG solution. Could you tell us a little more about your company’s role and the stage it is at?
Tenneco is responsible for the overall system layout and integration, including validation testing for the project. TEGs must undergo rigorous durability testing, using a wide range of exhaust gas temperatures. The test process must also simulate harsh operating conditions on the underbody of the vehicle, such as road bumps, salt corrosion and other examples of severe conditions. Tenneco will enter the system testing phase at the end of this year, after finalising virtual optimisation loops and component level testing.
Do you see Turbosteamers following a similar path to a TEG?
We see “Turbosteamers,” also known as Rankine system technology, following a similar path. We expect this to be first marketed for heavy-duty applications, with TEGs following closely behind.
Given that both a TEG is new relatively new technology, its price path is not yet mapped out. What direction do you think each will follow?
The remainder of this interview is available on just-auto’s QUBE diesel technologies research service