Continuing just-auto’s series of Q&As with tier one component suppliers, Matthew Beecham talked to Dr.-Ing. Wolfgang Reuter, vice president, sales and engineering, Tenneco Emission Control International, Geschäftsführer Heinrich Gillet GmbH.
Headquartered in Lake Forest, Illinois, Tenneco is one of the world’s largest manufacturers of emission control and ride control products. Some of the company’s recent launch successes include the Toyota Tundra in North America and the Suzuki Swift in Japan and Europe. Tenneco is one of 18 on-site suppliers to Toyota’s Tundra, which is assembled in the automaker’s new truck plant San Antonio, Texas. The company invested in two new facilities to supply the full exhaust system on the vehicle and introduced a new advanced laser welding technology designed to reduce muffler weight and lower material costs. During 2006 and 2007, Tenneco expanded its competence in diesel particulate filters in Europe and won business in North America on these same applications.
just-auto: Could we start by asking for some general observations of the forces driving the automotive emission technologies and how Tenneco is responding?
Wolfgang Reuter: The automotive emission technology is mainly driven by increasingly stringent emissions regulations globally. Concurrently, the emerging CO2 debate requires fuel-efficient engines like diesel or lean-burn gasoline engines with high demands in particulate emissions reduction and especially in NOx reduction technology. Tenneco is responding to increasingly stringent emissions regulations worldwide with highly-engineered emissions control systems for diesel and gasoline engine applications. For diesel aftertreatment, Tenneco is well-known as a pioneer in supplying particulate filters for automotive applications, currently supplying more than 20 passenger car models as well as medium-duty vehicles. In addition, the company recently acquired the ELIM-NOx technology, which advances Tenneco’s existing Selective Catalytic Reduction technology by offering a fully-integrated emissions control system that is designed to reduce NOx emissions by 70-90%. Globally, Tenneco has won production or development contracts on 13 emission-control platforms for SCR NOx abatement systems.
just-auto: Inevitably, the increasing complexity of exhaust systems introduces new challenges. Yet, adding a NOx absorber or SCR to diesel-powered vehicles adds significant costs. How do you see OE diesel exhaust content evolving through this decade?
How well do you really know your competitors?
Access the most comprehensive Company Profiles on the market, powered by GlobalData. Save hours of research. Gain competitive edge.
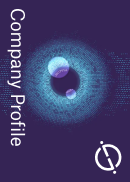
Thank you!
Your download email will arrive shortly
Not ready to buy yet? Download a free sample
We are confident about the unique quality of our Company Profiles. However, we want you to make the most beneficial decision for your business, so we offer a free sample that you can download by submitting the below form
By GlobalDataWolfgang Reuter: More stringent emissions control regulations worldwide are increasing the demand for more sophisticated emissions control solutions, which does increase the cost. However, Tenneco, like other suppliers, will continue to look for cost-effective ways to help OEMs meet the new emissions requirements. As volume increases on diesel aftertreatment, some economies of scale will be realised. We are also actively developing new materials, which offer cost reduction potential.
just-auto: Could you see gasoline engines going lean for fuel economy reasons?
Wolfgang Reuter: For getting full fuel economy benefits, direct injection gasoline engines should go lean. In this case, DeNOx technology such as Lean NOx traps (LNT) or SCR technology is required to meet the NOx emission limits. LNT and SCR technologies are currently under development for direct injection gasoline engines. However, today, most direct injection (GDI) engines are running stoichiometrics so that emission limits can be met with conventional three-way catalysts, making especially small GDI engines a cost-efficient alternative to small diesel engines.
just-auto: In the run-up to the introduction of Euro 5 in 2009, how do you see the particulate filter technology evolving? That is, do you see close-coupled filters as the preferred position versus the under-floor position? What about coated filters versus uncoated using additives; do you see strong OEM preferences?
Wolfgang Reuter: Clearly, the current trend in Europe is toward coated filters. Certainly, improving the thermal management of filters to improve regeneration characteristics, while minimising the fuel usage for active regeneration, is a priority and will lead to greater use of close coupled filters. Additive-based systems remain a useful technology for low temperature regeneration and may gain popularity in the non-road segment as regulations take effect.
just-auto: Are there cost implications, too? That is, do you see cordierite substrates becoming the main alternative to more expensive siliciumcarbid substrates?
Wolfgang Reuter: Cordierite filters require a very precise regeneration process as well as increased regeneration frequencies. These costs will have to be considered in moving toward cordierite. Demands for more precise and efficient regeneration technology such as hydrocarbon injection or hydrocarbon vaporisation directly into the exhaust stream will grow as a result.
just-auto: Are there moves being made to reduce the size of the filter itself through, say, a change in materials?
Wolfgang Reuter: Basically, the size of a filter is generally defined by the amount of ash it has to store during its lifetime. This depends on the engine oil consumption as well as on the expected useful lifetime, e.g. 240,000km. A change in material would not resolve this issue. Tenneco is working on improved filter structures that would reduce filter size significantly since ash storage would no longer be the deciding factor in filter sizing. Lower thermal mass and lower backpressure, both benefiting fuel economy, would be important ancillary benefits.
just-auto: Tenneco has expanded its capabilities in diesel particulate filters and won new business in Europe. What are your business targets for this market?
Wolfgang Reuter: We are always looking for new opportunities, but cannot elaborate on specific plans. We have recently announced that our global production of particulate filters will expand to approximately 2.8m units by 2012.
just-auto: How do you see the retrofit market for particulate filters evolving in Europe?
Wolfgang Reuter: The retrofit market will be driven by legislation in various countries mandating these systems on vehicles, as well as by government incentives to encourage consumers to retrofit their vehicles with diesel particulate filters.
just-auto: How do you think that governments should subsidise the cost of retrofitting DPFs? What are your business targets for this market?
Wolfgang Reuter: Those are decisions that must be made by the regulators. However, the environmental benefits of retrofitting DPFs have been made clear by many independent studies. We view actions that increase retrofit rates as beneficial to society.
just-auto: To what extent is the particulate filter technology different for retrofit applications?
OE filters are highly efficient filters, typically wall flow filters, removing more than 95% of particulates from emissions. The soot loading status of the filter is controlled by a variety of sensors and soot loading models integrated in the vehicle’s ECU. When a critical soot loading limit is achieved, a soot regeneration process is initiated by increasing the exhaust gas temperature to above 600° C independent of the vehicle’s operating condition. This is done by means of late- and post-injection, controlled by the ECU.
When retrofitting vehicles in use with filters, there is no sensor for soot loading control or the possibility of increasing the exhaust gas temperature by engine means. As a result, retrofit filters control the soot loading status, requiring open filter structures. This logically reduces the filtration efficiency to below 50%.
just-auto: The increasing number of catalytic converters inevitably leads to an increasing demand for noble metals. I guess that limited resources and correspondingly high prices are prompting the development of converters with higher efficiency and lower catalyst ageing. Is that correct?
Wolfgang Reuter: Yes. Noble metal costs, especially platinum and rhodium, have increased substantially in the last years. Improvements in the washcoat technologies have allowed a reduction of noble metal content per catalyst.
just-auto: As we see it, manufacturers are working toward positioning the catalytic converter as close to the manifold as possible, thereby making the catalyst smaller. Catalytic converters are also becoming more and more integrated into the manifold. Is this correct? What trends are occurring in the positioning of catalytic converters?
Wolfgang Reuter: Positioning the catalyst close to the engine is reducing the thermal inertia and thus accelerating the catalyst light-off. This results in a significant reduction of cold-start emissions. The better efficiency justifies the use of slightly smaller converters. Thus, whenever space limitations allow, a catalyst will be placed as close as possible to the engine. Many naturally aspirated gasoline applications have catalysts directly welded to the manifolds – the so-called ‘mani-verter’.
just-auto: What technical developments are occurring in the aftermarket for catalysts? How fast is this aftermarket growing?
Wolfgang Reuter: Over the last several years, the main technical developments in the aftermarket relating to catalysts have been made in the washcoat technology, which has resulted in increased durability and lifetime of the converter.
Another technology related to the converter industry is the tubular converter. This converter is produced with a system of different thickness and without welding. The result is a lighter-weight converter, which helps reduce the overall weight of the vehicle.
In general, the converter aftermarket business has increased substantially between 2004 and 2007.
just-auto: I guess recycling of used catalytic converters is another important challenge. How is the automotive industry addressing this?
Wolfgang Reuter: The collection and recycling of used catalysts is organised according to the rules and practices of each country. In some countries, there are specific companies that recycle the remaining metals out of used converters. After cleaning the metals and adding the acid, the metals can be re-used for other non-related automotive products.
just-auto: Although, on the face of it, fuel cell technology presents potential threats to catalyst technology, what is the reality/outlook for the catalytic converter? What do you see as the major challenge for vehicle catalysts over the next five years?
Wolfgang Reuter: Looking at the current development status of fuel cells, it in very unlikely that we will see fuel cells as serious powertrain alternatives available within the next five years. Thus, there is no threat to catalytic converters as the most efficient aftertreatment technology for combustion engines. In fact, the market for catalytic converters will grow as emission standards become even more stringent in the future. Higher content catalytic converters that achieve energy recuperation for lower CO2 emissions are an opportunity. The only segment that may see alternate technology is the non-road vehicles, where thermal regeneration devices may be used in lieu of diesel oxidation catalytic converters due to the low operating temperature of the associated duty cycles.
just-auto: Finally, do you see any other trends emerging in the automotive exhaust systems industry?
Wolfgang Reuter: OEMs are requesting more development support from system suppliers like Tenneco as the emissions control systems become more complex. Traditional emissions control suppliers have gone from being component suppliers to full system suppliers and now full technology suppliers.