Surface Processing Ltd (SPL) is the largest sub-contract chemical cleaning facility of its kind in the UK today. In the automotive sector, SPL offers a range of services including removing corrosion from classic cars and weight from motorsport bodyshells to the removal of paint from support jigs and new components. Lately it is this latter area where the firm has experienced significant growth. Its processes are trusted by OEMs and suppliers as a method to recover parts that would have been previously scrapped. In this interview, Matthew Beecham talked with managing director Adrian McMurray about the firm’s growing OEM activity.
Could you sum-up the process you operate from here in Dudley?
Our process is able to gently remove a range of contamination including paints, sealants, adhesives, noise reduction materials and underseals. In addition, it effectively removes rust without attacking the surface of the substrate, usually steel but we treat other metals including aluminium. After the contaminants are removed, the work piece is completely passivated and neutralised before being coated with a protective finish. For this we can arrange wet painting, electrophoretic coating, galvanising, coating etc.
We understand that you are well known in the classic car industry for removing rust from car bodyshells?
Yes, we offer a fully immersive process and our tanks can take parts ranging from small simple components right through to large complex assemblies such as an entire car body shell. For this sector, we offer a far more effective way of dealing with rust than traditional methods. It is gentler than blasting and because we can immerse a whole shell we can reach areas that are out of sight, meaning we can reach and dissolve out more of the corrosion. We do around 250 car bodyshells a year including more professional motorsport too, including World Rally and British Touring Car teams.
Why do motorsport teams use you?
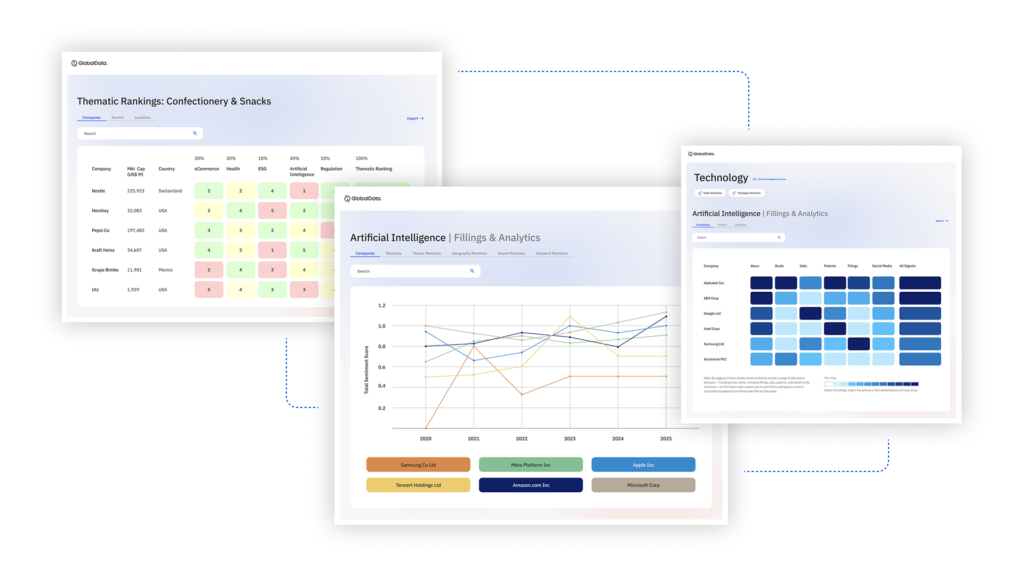
US Tariffs are shifting - will you react or anticipate?
Don’t let policy changes catch you off guard. Stay proactive with real-time data and expert analysis.
By GlobalDataIf you take a bodyshell off the production line it contains a lot of unnecessary weight. Paint, underseal and NVH material, that isn’t needed in a race or rally car, can simply be cleaned away. We can get rid of all this leaving clean metal for the fabricators to work on. From a health and safety point of view it’s much better to weld clean, bare metal than trying to do this through paint. We know we can remove around 30kg of weight from a shell safely without affecting the material thickness. This is a real benefit and enables teams to optimise ballast and strength, etc.
I must stress that this isn’t the acid dipping used in the 1970s — that used to attack the good metal and was uncontrollable. We think the teams perceive our chemical process as much more effective than bead blasting. Bead blasting inevitably stress relieves the panels leaving rippling resulting in a poor paint finish as well as the problem of how to remove all the debris and cannot reach inside box sections.
What is the process exactly?
Our process follows five key stages.
First is decontamination. Heavy organic coatings including underseal, sealants, anti flutter/NVH materials and adhesives are broken down.
Stage two removes remaining compounds such as paint and grease. This is achieved using an alkaline hydrocarbon solution.
Stage three uses a dilute solution of inhibited hydrochloric acid to remove corrosion. Key is the inhibitor to prevent the acid from attacking the metal.
An alkaline neutralisation and passivation immersion process follows and leaves the work piece in a bright, preserved condition before a final wash and preservative finish.
The part can then be returned to the supplier or as many of our customers request we apply a primer coating, typically electrophoretic aka e-coating.
E-coating is widely used in the car industry offering excellent corrosion resistance and as with the stripping process it’s a multi stage immersion process which is cured at around 185°C leaving a highly uniform finish around 25 microns thick.
So how is your process used by suppliers?
It’s not only suppliers but also the car manufacturers themselves and we work with a growing number around Europe. We believe our process offers a very cost effective method of recovering components such as pressings, castings or sub assemblies. Imagine that many of these are new parts but have been rejected for weld problems, paint defects, rust or other contamination. Historically, the parts would have been scrapped or gone to land fill with the associated costs and environmental charges.
Why is this type of process not more widespread?
Creating a process that is consistently reliable is very difficult. We have been perfecting our processes since 1994 so know what is needed to treat a wide range of metal substrates. We also have the scale and experience to handle larger volumes and units that make it more cost effective. We even have some customers sending parts to us and they have their own stripping facility. However, they like the fact we can cope with large volumes and turnaround batches quickly. We operate around the clock to minimise turnaround times. As supply chains become leaner, it is imperative to recover as many parts as possible quickly. Our location is a benefit with many of the key suppliers and OEMs close by but we receive parts from all over.
What kind of automotive parts do you treat?
It really is a full range of things. In the last few weeks it has included large 20 cylinder generator set engine blocks, pipework and vessels, automotive suspension components, bracketry, subframes, wheels, body panels and of course entire bodyshells. We have a specific process for aluminium too and process a range of underbody and outer panels. We also have batches of many thousands of nuts, rivets, bolts too. We can deal with a real range of parts.
What other automotive work is there other than recovery of parts?
We do a lot of cleaning of tooling, jigs and fixtures. Jigs used to hold painted parts quickly get clogged up making them hard to use and hamper electrical contact. We can remove all the layers of paint quickly and safely. We clean press tools, engine blocks, plant equipment and we’ve even cleaned and painted the factory gates to remove years of paint and corrosion!
Can you indicate the levels of savings that can be achieved?
Aside from the obvious need to scrap reject components we provide cost effective tooling recovery. Through regular cleaning of paint line tooling and equipment such as phosphate pipes, floor grids, jigs and hooks customers can reduce plant down time and subsequent reject rates whilst also delivering improvements in health and safety and environmental impact.
What about the future?
We have a very exciting project underway to investigate the possibility to remove paint from plastic parts. This would enable their recovery and dramatically reduce scrap rates. This is very exciting and we are working with a number of painted plastic parts manufacturers, both interior and exterior to get this up and running. We‘ve also just gained exclusive access to a new, military grade e-coating facility that can take large components, up to seven metres in length. In addition, we are about to launch a range of anti corrosion products, this will enable us to provide many of our customers including the classic car owners with the very latest in safe and effective systems in simple to use and apply kits.