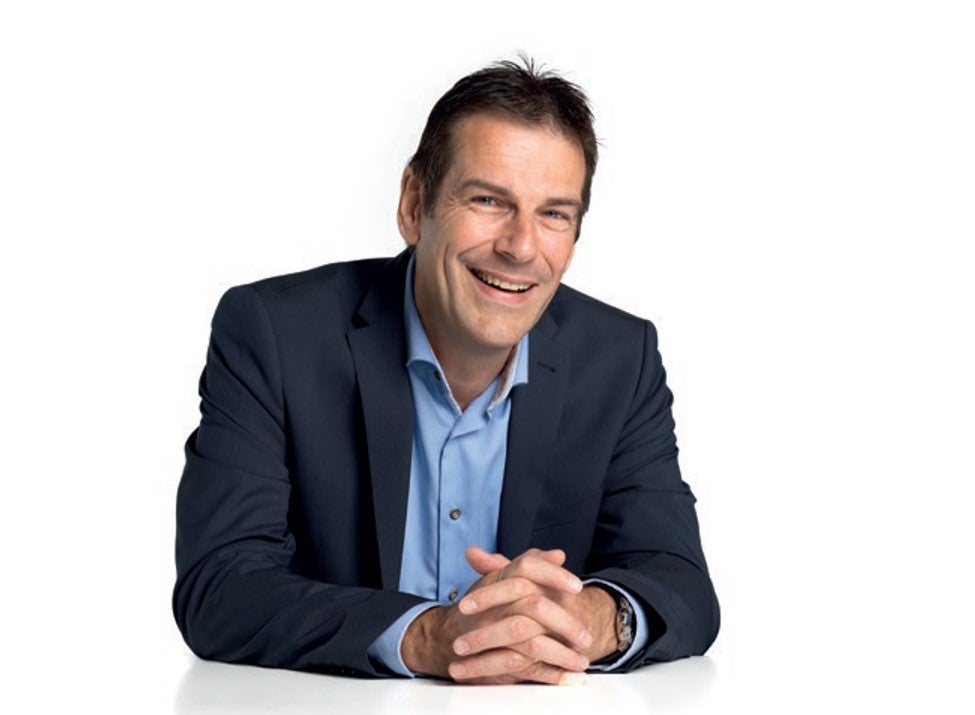
Just Auto: 2021 was another memorable year for everyone and for all sorts of reasons. We had a bumpy recovery from the worst of the Covid pandemic, but the automotive industry was also hammered by a shortage of semiconductor parts. In your business, what stand out as the biggest challenges you faced last year?
LG: We saw a rising demand from the automotive value chain bringing new opportunities for specialty materials. The shortage of incumbent materials creates opportunities for high performance thermoplastics that can meet complex thermal, mechanical, electrical and optical requirements. However, in an environment that is changing so rapidly, it is crucial that we understand the critical technical requirements for emerging applications. We have world-class predictive engineering capabilities to identify how our materials can successfully support new designs, meet stringent regulatory demands, and replace metals. These solutions are especially present in areas related to enabling a lower carbon footprint, accelerating electrification and building a reliable charging infrastructure. Additionally, we are working to support the automotive industry in implementing regulatory changes requiring new sensor technologies for ADAS components, increased fire resistance and other improvements in vehicle safety.
JA: Any high spots or particular successes you’d like to share?
LG: We do have multiple success stories to share:
- In the EV segment, our contributions come from specialty solutions that deliver enhanced properties and contain recycled or bio-renewable feedstock.
- In the area of sensors, we developed LNP™ THERMOCOMP™ WFC06I and WFC06IXP compounds to help designers of Advanced Driver Assistance Systems (ADAS), such as radar units, meet goals related to size and weight reduction, signal transmission accuracy and reliability improvements, and seamless integration with vehicles.
- In terms of fire safety, our new NORYL™ NHP6011 and NHP6012 resins provide best-in-class, non-chlorinated/non-brominated flame retardancy to achieve strict UL 94 V-0 ratings at 1.5 mm while enabling EV batteries to be built with high stiffness and impact strength for crash protection.
- Another highlight is SABIC’s newly introduced portfolio of bio-based ULTEM™ resins, the world’s first certified renewable high-performance amorphous thermoplastics with International Sustainability and Carbon Certification Plus (ISCC+) accreditation. These sustainability driven specialty materials are a drop-in solution for manufacturers still using PEI made from virgin feedstock. They offer a seamless means of reducing the carbon footprint of automotive applications where high temperature, dimensional stability or demanding mechanical performance is required, without the need to invest in new tooling.
- We collaborated with EconCore, a global leader in honeycomb technologies, who has developed new honeycomb cores for laminated sandwich panels made with SABIC’s NORYL™ GTX™ resin, a polyphenylene ether (PPE) blend. The new cores offer higher heat performance, better dimensional stability and lower water absorption compared to honeycomb structures made with traditional thermoplastics. These properties enable the new core material to be used in demanding applications such as certain automotive, e-mobility and photovoltaic components. Furthermore, end-of-life recycling can be facilitated by combining this new honeycomb core technology with thermoplastic composite skins to produce all-thermoplastic sandwich panels.
JA: How are you feeling about 2022 – both in terms of business prospects and more generally?
LG: In July, the European Commission announced the Fit for 55 climate package, proposing a CO2 reduction target for cars of 55% by 2030, based on 2021 levels. According to the European Automobile Manufacturers Association, or ACEA, this will be very challenging, and certainly requires a corresponding binding target for member states to build up the required charging and refueling infrastructure.
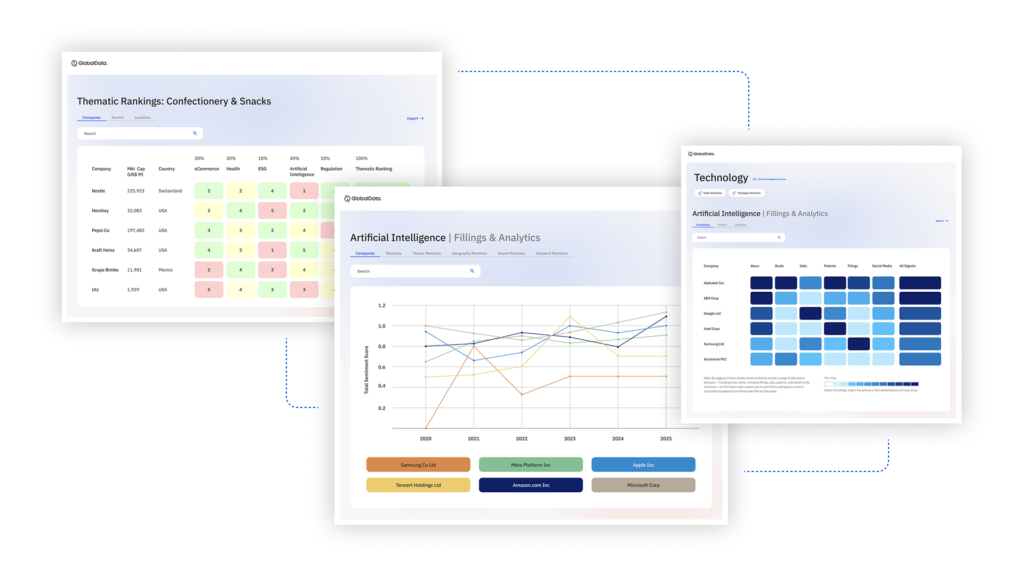
US Tariffs are shifting - will you react or anticipate?
Don’t let policy changes catch you off guard. Stay proactive with real-time data and expert analysis.
By GlobalDataToday, there are approximately 230,000 charging stations in Europe, most of them concentrated in 5 countries. To achieve a 55% CO2 reduction, ACEA estimates that a total of 6 million publicly available charging points need to be distributed across the EU, with significantly increased efforts by all stakeholders – including member states and all involved sectors.
Specialty materials can provide excellent impact performance, weatherability and chemical resistance, helping OEMs create safe and durable energy storage and supply equipment. SABIC is working with leading manufacturers to enable the fast roll out of reliable charging stations, batteries and components for home and public use that can help expand the EV supply equipment network and promote faster consumer adoption of electric vehicles.
Recent studies have revealed that up to 70% of EV owners tend to buy another EV. The number of new EV models will increase from 24 in 2020 up to 168 in 2025. We continue to support manufacturers unleash the advantages of our advanced thermoplastics portfolio and our application development expertise. Our solutions and services allow designers to integrate parts and open design possibilities for new automotive components that can be more efficiently made, assembled and used.
Our technological advantage comes from decades of customer intimacy in Automotive and Electrical industries. The electrification of the automotive market is a convergence of both industries and SABIC brings the knowledge and portfolio to help OEMs achieve energy efficiency, safety, and a differentiated driver’s experience.
JA: Is anything emerging as a particular concern in terms of the outlook?
LG: We acknowledge that we are still living in unprecedented times with this global pandemic, with all the potential disruptions including uncertainties in the global supply chain. Through it all, SABIC’s Specialties business has been a reliable supplier, delivering unique value and solving our customers’ hard challenges.
Travel bans have impacted the personal presence of our customers in our labs. In-person meetings are an important interaction when we support our customers in bringing innovation to their new products. So we established a live streaming service from our labs, through which our customers connect directly with our scientists and view testing in real time. This means they can experience our technology capabilities located in different regions virtually and use them to bring new products faster to market.
JA: Do you have a message for Just Auto’s readers?
LG: Collaboration is fundamental, especially in times of change. Building a carbon neutral future and climate resilience is a challenge to all participants in the value chain of e-mobility. SABIC is committed to delivering the novel material science for future technologies, enabling lower carbon emissions and advancing the circularity of plastics, while improving the way we travel, connect, and live.