In this interview, Matthew Beecham talked with Robin Coppenrath, global business manager, SABIC Innovative Plastics about the use of the company’s resin, STAMAX, in front-end modules. The Innovative Plastics strategic business unit of SABIC is a major supplier of engineering thermoplastics. In addition to automotive, SABIC serves the electronics, building and construction, and healthcare markets. Its product portfolio includes thermoplastic resins, coatings, specialty compounds, film and sheet.
just-auto: Could we start by asking if you could talk us through your automotive business with respect to front-end modules?
Robin Coppenrath: Front-end modules are a good example of where we can help OEMs and Tiers meet local market needs and achieve global environmental and safety requirements. In this kind of structural application, OEMs are looking for performance comparable to steel in terms of strength, but a lighter weight, improved overall quality and, of course, a lower cost.
To meet this need, we offer STAMAX long glass fiber polypropylene (LGFPP) resins. These resins have been used extensively by European automakers to replace steel in key components like front-end modules as well as door modules, dashboard carriers, underbody shields, tailgates, seating systems and other structural and energy management systems. Compared to short glass fibre PP, STAMAX resins deliver higher impact resistance and stiffness and improved dimensional stability for tight tolerances. These resins have huge potential for the automotive industry worldwide.
As we understand it, your STAMAX LGFPP resin is used on the CX30…
Chang’an chose STAMAX resin for the CX30 model, the first Chinese-developed vehicle with an all-plastic FEM. This application integrates 22 metal components into one injection-molded part. As a result, the front-end structure of the vehicle is greatly simplified for easier assembling and overall cost reduction. Also, by replacing steel, Chang’an was able to cut part weight by up to 40 percent and total vehicle weight by about four kilograms.
How well do you really know your competitors?
Access the most comprehensive Company Profiles on the market, powered by GlobalData. Save hours of research. Gain competitive edge.
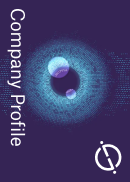
Thank you!
Your download email will arrive shortly
Not ready to buy yet? Download a free sample
We are confident about the unique quality of our Company Profiles. However, we want you to make the most beneficial decision for your business, so we offer a free sample that you can download by submitting the below form
By GlobalDataThis is a significant translation of a proven technology, enabling Chang’an to lighten a vehicle for improved fuel economy, reduced emissions and lower overall costs. All of those benefits are driving factors, but so too is the desire to design with greater freedom, which STAMAX resins allow, and the need to comply with regulations in crash safety and pedestrian protection.
What are the benefits of your material compared to the traditional front-end modules which are usually made from a combination of sheet metal and glass-reinforced plastic components?
The benefits are the following: lower weight (density), thinner walls through best-in-class application design and engineering, lower system cost through functional integration and a significant reduction in the number of parts. The typical reduction is from 25 parts to three parts for assembly. Further optimization could reduce the construction to just one full plastic part. Both solutions streamline the assembly process and achieve significant cost-efficiencies. Engineers like simplicity and that’s what STAMAX resins make possible.
Can you see more use of plastic/metal (or ‘hybrid solutions) for structural applications to help meet these EU rules for pedestrian protection?
Whether it’s the expanding market for small cars or electric and hybrid vehicles, designers and engineers are looking for innovative approaches and materials for greater flexibility and strength, especially with space at a premium. In our view, materials can be seen as complementary, depending on the specific application needs. In some cases, the best solution can be an all-plastic component.
The best designs are full composites, and that’s because you can combine qualities of the materials they are made out of. Composites make possible a wider range of possibilities and allow you to obtain a broader set of specific properties or characteristics. In a composite design using STAMAX, you can use its anisotropic properties and glass fibre orientation to the maximum to obtain the desired performance.
Can you also see more use of plastic only parts to meet the EU rules for pedestrian protection, e.g. for hoods, fenders and lighting systems?
Regulatory compliance in the pedestrian protection area is one of the pressures facing automakers today. Converting from traditional materials to plastics or creating entirely new components from plastics can help OEMs find answers. Pedestrian safety is a very good example of the major difference thermoplastics can make. By increasing the flexibility of fenders compared to steel, high-impact STAMAX resins can help provide excellent head impact energy absorption in pedestrian incidents, as well as the recovery of the fender from minor collisions. STAMAX resins and another lightweight and tough SABIC Innovative Plastics material, Xenoy resin, are increasingly being used in energy management systems such as bumper energy absorbers.
See also: Global market review of front-end modules – forecasts to 2026