Compared to the shape limitations of glass, polycarbonate glazing is highly versatile. It is also lighter by as much as 50% and has high impact resistance. In this interview, Matthew Beecham talked with V. Umamaheswaran (also known as “UV”), global director of automotive products, marketing and technology, for SABIC’s Innovative Plastics strategic business unit. Innovative Plastics is a strategic business unit of Saudi Basic Industries Corporation (SABIC).
In terms of applications, where do you see the opportunities for plastic glazing on passenger cars?
Opportunities abound across various applications, from rear quarter and front quarter windows to roofs and spoilers. These applications are already demonstrated in production around the world.
Backlites represent the next greatest opportunity because this is an application where automakers can take full advantage of the many benefits made possible by PC glazing.
Whether it’s styling, the need to take weight out of the car, or the wish to achieve greater parts integration for reduced costs, PC glazing is a strong candidate.
How does polycarbonate compare to glass in terms of long term durability, particularly with regard to UV degradation? Does PC absorb UV energy? If so, to what extent does it change the material chemistry over time?
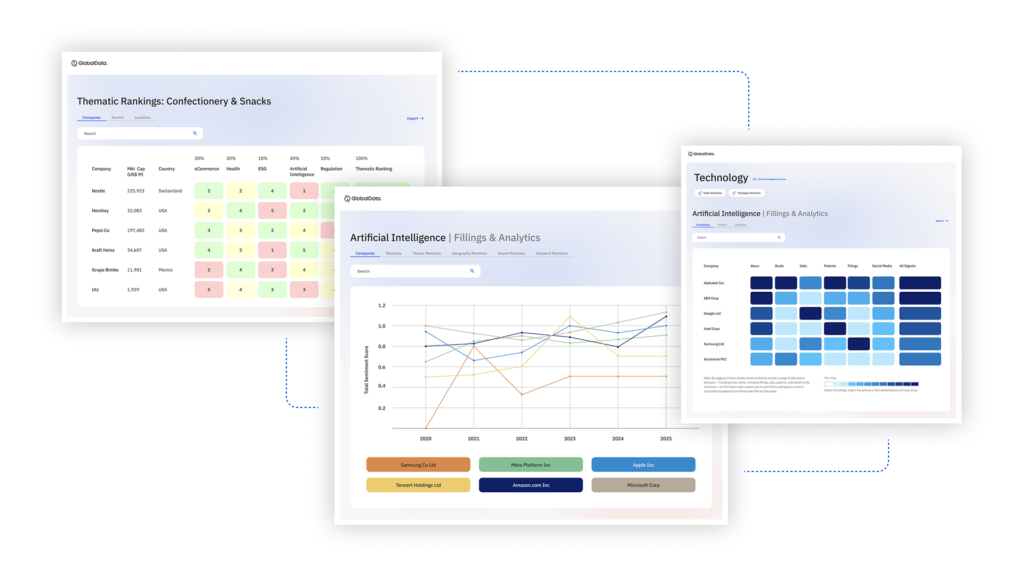
US Tariffs are shifting - will you react or anticipate?
Don’t let policy changes catch you off guard. Stay proactive with real-time data and expert analysis.
By GlobalDataPolycarbonate is well established for many decades in use for exterior applications ranging from clear headlamp lenses to high gloss black trim. These applications have polymeric or organo silicone coatings that enhance PC’s exterior weatherability and durability and that protect it from UV degradation.
SABIC’s EXATEC PC coating systems, such as our E900 product series, delivers glass-like scratch and UV resistance and provides the performance to meet global regulatory requirements for glazing applications.
The exciting development is that PC glazing technology continues to evolve. We just announced with ULVAC, who is a world leader in mass-production vacuum technologies, the launch of the ULGLAZE system. This technology makes possible high-volume production of plasma-coated PC components for automotive glazing applications. This is a significant milestone in equipping the automotive industry with the tools to adopt PC glazing cost-effectively and on a broad scale. This is very important because PC glazing represents a tremendous opportunity for automakers and tiers to replace heavier glass windows in the every-gram-counts environment that they find themselves in today.
PC suffers from a lower stiffness compared to glass. How does SABIC deal with this problem?
In general, a glazing design that incorporates a flat piece of glass is never directly replaced by a glazing application designed with PC resin. PC glazing can deliver the needed stiffness for glazing applications with adequate styling, feature integration and parts consolidation through second shot moulding.
Can PC glazing be used to meet the increasingly stringent EC regulations, for example concerning pedestrian safety?
In a word, yes. We are exploring concepts and the potential for PC glazing to help address pedestrian safety concerns, which certainly is a growing challenge for automakers.
This is an area where plastics can make a major difference and it is an area where SABIC has significant experience, know-how and capability. Materials like our high-impact XENOY resin are increasingly used in energy management systems on vehicles. A recent example would be the Range Rover Evoque, which uses XENOY iQ resin for its pedestrian energy absorber. This material provides efficient energy-absorption countermeasures to meet pedestrian protection and low-speed damageability requirements. SABIC has a great deal of knowledge, experience and proprietary design, engineering and predictive tools to help our customers reach their goals in this space.
What are the technical challenges that SABIC still face with PC glazing?
Over the years, SABIC has consistently invested in developing LEXAN resin glazing solutions and has solved a variety of technical challenges with innovative solutions both by itself and in conjunction with industry partners. PC glazing has now been put into production by several OEMs who see the clear benefits and value proposition. The industry has progressed much in understanding the key benefits in weight reduction, styling, design freedom and parts consolidation versus tradeoffs in stiffness, noise transmission, etc.
Presumably the relative cost of plastic glazing compared to glass is still a major concern for carmakers when considering its widespread adoption?
Cost is an important consideration for everyone in the industry, absolutely. That said, we think the cost of glass versus PC glazing is not an apples-to-apples comparison. PC glazing can do so much more than glass. In fact, PC glazing is almost in its own category for all that it can offer: significant parts integration, reduced weight, increased aerodynamic efficiency, insulation and thermal management benefits and, of course, styling and design freedom. Cost should always be considered at the system level with value attributed to the additional benefits PC glazing brings.
Are you aware of any moves to develop special coatings (such as polysiloxanes applied by chemical vapour deposition) to give polycarbonate sufficient scratch resistance to compete with glass in tomorrow’s windscreen applications?
The remainder of this interview is available on just-auto’s QUBE research service