Two years ago, Bugatti unveiled details of its revolutionary seven-speed twin-clutch DSG gearbox, subsequently launched in its Veyron car. Developed by Ricardo, the unit handles the massive torque produced by the Veyron’s 1001bhp 16-cylinder engine. Since then, Ricardo has been pushing back the technical boundaries of dual-clutch systems. Matthew Beecham talked to Ricardo’s Lee Sykes, Global Product Group Director, Transmissions and Drivelines, Jim Hey, Chief Programme Engineer, Transmissions and Drivelines, and Jon Wheals, Chief Engineer, Innovation, about what we could expect to see emerging from the development house.
just-auto: Could you cast your minds back to recall the key technology advances which made the production of the dual-clutch transmission [DCT] possible?
Lee Sykes: If we go back five or six years, the first dual-clutch development programmes for passenger cars were led by Volkswagen and Ricardo. Although both systems at one level were radically different, particularly in terms of vehicle type, in many respects they were extremely similar in that they were both wet clutch technologies and fully hydraulically actuated. So fundamentally it was almost like two AMTs [Automated Manual Transmissions] added together without any great leap forward on any sub-system technology. Going forward, however, there is still a huge development opportunity that should be explored. Although a DCT is more efficient than any planetary automatic transmissions, it is not as efficient as, say, an AMT. So we feel that there are major development opportunities to substantially improve efficiency, packaging, weight and production cost.
Jim Hey: The current production state-of-the-art DCT uses hydraulics which dominate its architecture, resulting in knock-on efficiency penalties. Hydraulic systems use lots of components which increase packaging space and cost. As we work on the second generation DCT — due in the 2010 – 2012 timeframe — hydraulics may or may not feature in that technology. We are aiming to propose a better solution.
Jon Wheals: The actuator we have invented and developed for application to the next wave of electrically actuated DCT is based upon some PhD research about four years ago. That has now come to fruition. Called a Linear Motor, it generates high forces without the requirement for gearing. It is multiplexed within the transmission to control gear selection and to operate one of the two clutches. Just two devices are required to control a twin clutch transmission with up to seven gears. A conservative estimate shows a 22% cost saving over DQ250 (VW’s DCT) and a fuel economy saving approaching 6.5% using a unique nested dry clutch arrangement rather than concentric wet clutches. We have anticipated the limitations of current dry clutches for the sustained slip required for creep driving and hill holding – our patented solutions support our claim of a viable product derived from our next demonstration vehicle, rather than an interesting technical showcase.
just-auto: I guess the popularity of diesels in Europe is giving the DCT system a boost, given it can save up to 15% fuel on a diesel car and up to 5% on a gasoline powered car. In addition though, what is the impact of direct injection gasoline engines in combination with turbochargers on your DCT?
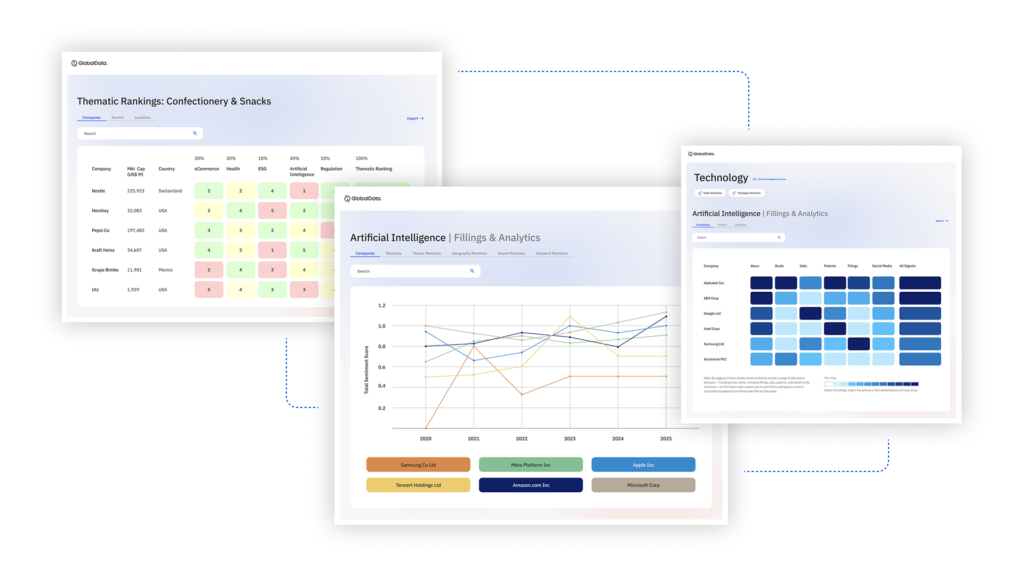
US Tariffs are shifting - will you react or anticipate?
Don’t let policy changes catch you off guard. Stay proactive with real-time data and expert analysis.
By GlobalDataLee Sykes: I drive a turbo diesel DSG. In my opinion, currently one of the weaknesses of the DCT product relates to its launch performance compared to, say, a torque converter automatic transmission. With any sort of turbo lag effect that I see in my car, that tends to limit the launch characteristics of current generation DCT. So turbocharging, at the moment, is an integration challenge which needs to be overcome in next generation products. From my understanding, I think it is a little too simplistic to say that it is purely an engine problem. It is an integration problem.
Jim Hey: While the European market is currently dependent on manual transmission technology, the driver for automation is essentially emissions legislation. We see a future where manual transmission may even be legislated against. That could create an environment where you need automated manual transmissions, whether that is a DCT or a smarter AMT or something in between. Clearly, there is a big difference between an AMT and a DCT so what is really required is the drivability of a DCT but with the parts count and cost closer to an AMT.
Lee Sykes: To summarise our development targets for next generation DCT, we are aiming to have a sub-system of technologies and an architecture that can applied to AMT and DCT in a modular way to potentially add upgraded parts all with a view to improving efficiency compared to current systems by 5 – 10%, substantially improve packaging and improve cost at least 25%. At a paper study level, we believe that we shall be approaching those targets. But as a company we need to go beyond paper and in one year’s time, certainly on the DCT side, we are looking to have running vehicles. We want to be able to go to the market not with what we think can be done but what can actually be done. We should have a driveable vehicle in one year.
just-auto: At an industry level, what are your ambitions for fitment of the dual-clutch transmission in Europe?
Jim Hey: At the moment, we see DCT at about 1% of the market which is on a par with CVTs. By 2015, however, we expect 10% of the market will be DCT, mainly driven by the B- and C-segment vehicles.
Lee Sykes: The market will be fairly diverse by 2015. There will be planetary automatics, DCTs and maybe a modest resurgence of AMTs as well. DCT will be a sizeable part of the market but I don’t think that it will dominate.
just-auto: How do you see the future for continuously variable transmission?
Jon Wheals: In overseas markets, particularly Japan, there is a strong liking for CVTs. In the UK and Europe people have tried to introduce a stepped characteristic DCT in order to overcome what is perceived to be a very negative lack of connection between the driver and the vehicle’s response. Indeed, Ricardo developed control software for the BMW Mini to introduce stepped ratios for the auto variant that used a CVT.
Lee Sykes: If we had this conversation about eight years ago, we were certainly postulating then that CVTs would be a bigger part of the market than they are presently and would be much more of on an upward path. I guess the issue is that over the last four or five years there has been a marked reluctance from the customer base to accept the functionality and performance of CVTs other than in certain markets such as Japan. There is enough evidence to suggest that CVTs will not become a dominant product but will probably remain a strong niche product in certain key markets.
just-auto: What stage of development is your torque vectoring technology at?
Jim Hey: Torque vectoring is a technology that we are developing to influence the vehicle dynamics using the driveline. For the last five years, we have been looking at what would be the next differentiator in driveline technologies. In the last ten years, we have seen a rise in the number of four wheel drive products and performance products available from manufacturers. As more and more volume automakers enter that segment, the premium automakers have to stay ahead. So essentially with torque vectoring, what we are trying to do is create speed differences between output shaft of a different differential. In 2003, we modified a BMW X5 SUV that used an electric motor to drive a gearset in the transfer case and send torque to the rear. That meant it was able to change the torque split so that we could effectively make the vehicle rear wheel drive, front wheel drive, or any point in between. That in turn allowed us to exploit higher characteristics in order to change the handling response of the vehicle primarily using an electric machine as the main actuator within our system.
just-auto: Was the market ready for it?
Jim Hey: When we finished that particular programme, we had a lot of feedback from the market that it is very interesting technology but the way we had approached it in research terms meant we had not got enough authority to influence handling and the full range of driving manouevres and road surfaces. What we had achieved, however, was a very compact gear and device arrangement that could lend itself to a number of different applications. Since 2003, we have been trying to update that system, replacing the electrical machine with two wet clutch packs. And effectively what we have now built is an Audi A6 Quatro that has this system across the rear axle. That allows the vehicle to more faithfully follow the driver’s requested path without having to have a high degree of skill to make the car go where you need it. We have just demonstrated that vehicle in northern Sweden. It has been very well received by OEMs so far. We are anticipating that the first application for us will be in 2010.
Lee Sykes: As a development house, we were one of the pioneers on 4WD. In fact, we have always had a strong pedigree in all wheel drive systems: the company which has evolved into the Ricardo Driveline and Transmission team invented the viscous coupling, and supported the development of the world’s first 4wd production passenger car (Jensen Interceptor FF); now we’ve invented a unique differential … so we’ve coined the term “torque vectoring” to describe its function – and now that’s accepted automotive terminology. Although these systems have arguably been on a wane in terms of new development, we certainly see a future for torque vectoring both in two wheel drive applications and in certain four wheel drive applications as well.
Jim Hey: A big focus of our business is that the car industry first expects more for the same and then expects more for less. So things like torque vectoring falls into that category. We are able to deliver more features, functions and saleable attributes in the vehicle for an incremental cost over the existing driveline. But in the future, we are going to have to provide all of that for the same money or even less. As we transition that technology to tier ones and OEMs for implementation, our challenge is to find the next technologies that allow that feature content to be maintained with cheaper technologies. So I think that when we did the X5 we were ahead of our time in using an electrical machine to manipulate drive torque. In the future I think that will come back again as we are able to increase the sale proposition of hybrids but by being not only an all wheel drive but by having better handling attributes.
just-auto: How much will this torque vectoring cost the automaker?
Jim Hey: Our target for the system at volumes of 20,000 – 50,000 units annually is under €300. But in terms of how that would translate into a sale price then I think the attributes are saleable from between €2000 – €3000 on the car. So it makes good business sense for the OEM.
Jon Wheals: So the first step is that you will see torque vectoring in the premium brands. The second element of value will come from increased integration with ESP. Brake manufactures are also now starting to see that they now have something that can influence some aspects of dynamics more effectively. Just as we’ve applied unique forms of electrical actuation to DCTs to reduce cost and improve efficiency, the second wave of Torque Vectoring differentials will eliminate hydraulics and use specific electro-magnetic actuation – and we’ll have working concepts within 3 months following client interest for application in 2012.