As automakers increasingly use simulation to supplement their vehicle test programmes, Matthew Beecham spoke to Chris Hoyle, technical director at rFpro, the simulator software company which recently won an award for its new approach to producing digital road models.
How does rFpro's digital road modelling service help vehicle manufacturers?
Revisions to a vehicle to suit individual market tastes and conditions late in a development programme are so costly that manufacturers aim to avoid such issues by testing as early as possible. Waiting until representative prototype vehicles are available before validating global platforms against regional differences in road surface characteristics is too risky. Driver-in-the-loop (DIL) simulators help by allowing a human driver to experience the vehicle's behaviour in a virtual environment, long before physical prototypes exist, but to be effective they need a level of road surface detail that has been unavailable until now.
There are also practical and operational benefits for manufacturers even after prototypes exist, by using simulators correlated against physical testing, simulation allows more effective preparation for 'real' tests so vehicle developers can achieve more during their test window, or of course speed up development by testing all year round, 24 hours a day, unaffected by weather or track availability, on a consistent and repeatable road surface.
What level of detail do you have to provide, in order for a simulator to be effective?
See Also:
To assess the dynamic behaviour of a vehicle in a meaningful way, we have to capture and reproduce every aspect of road surface texture and detail; every ripple, bump and break in the surface. This can be as varied as a frost-damaged Detroit highway, an undulating minor road in Wales or a smooth German autobahn. For example, we have replicated the entire Nordschleife circuit, over 20km, with a vertical tolerance of less than 1mm!
How well do you really know your competitors?
Access the most comprehensive Company Profiles on the market, powered by GlobalData. Save hours of research. Gain competitive edge.
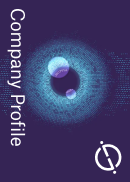
Thank you!
Your download email will arrive shortly
Not ready to buy yet? Download a free sample
We are confident about the unique quality of our Company Profiles. However, we want you to make the most beneficial decision for your business, so we offer a free sample that you can download by submitting the below form
By GlobalDataOf course, to be effective in a simulator, we have to communicate that level of detail in real time to the vehicle model. Our Terrain Server software captures every lidar-scanned data point within the tyre contact patches (usually four), and integrates them all to provide the vehicle model with accurate road input at a refresh rate of up to 1000 times per second.
Isn't the process of capturing road surface detail painfully slow?
We use a breakthrough in scanning technology that involves replacing the usual single pulse laser LIDAR time-of-flight scanning process with a number of separate, phased laser signals. Instead of waiting for each signal to return before firing the next one, the controlled phasing allows the signals to be overlapped, increasing the speed, quantity and quality of data captured. Whereas the scanning vehicle once travelled at a crawl and surveys often had to take place at night, we can now operate at normal road speeds, yet we capture up to 50 times the previous level of detail.
To provide global coverage, we work with a network of regional partners who carry out our road surveys, each using the new phased scanning technology. This is proving the only way to handle growing demand for our services; we expect to build more than 3000km of digital road models during 2015 – compared to 1000km last year.
With the growing workload and increased level of detail, don't you generate unmanageable quantities of data?
We have switched to Cloud-based processing and storage which enables hundreds of CPU cores to work simultaneously on data processing and provides almost limitless scope for further growth. A typical road route will generate 1 Terabyte of data per 10km during processing and the move to cloud based computing has enabled us to scale our data processing far more effectively and reliably.
Does all this mathematical modelling risk taking real drivers farther and farther out of the loop?
We're actually helping to re-introduce human input into the early stages of vehicle engineering when many of the key decisions are made. Virtual modelling has come to predominate this phase of a vehicle programme but our combination of realistic levels of detail and low latency, for fast system response, means DIL simulators can move beyond driver training and man-machine interface studies to allow meaningful human evaluation of the vehicle's dynamic behaviour.
Virtual modelling can also provide a safe and repeatable environment in which drivers with a wide range of different abilities can experience situations which could be hazardous in a real, physical test, such as limit manoeuvres.
Are there any particular industry trends that are driving demand?