UK-based rFactor Pro focuses on simulators for engineering development of vehicle dynamics and the control systems and active safety systems that affect vehicle dynamics. The company is moving into the automotive sector and has developed new ultra fast response software which allows automakers to simulate vehicle dynamics in a way that has not been possible before. Normally, simulation is restricted to tasks such as driver fatigue and cabin ergonomic development. rFactor Pro’s technology allows automakers to accurately simulate active safety systems (such as SUV rollover), NVH, ride and handling. To find out a little more, Matthew Beecham talked with rFactor Pro’s technical director, Chris Hoyle.
Could you tell us more about your ultra fast response simulator software?
It extends the scope of vehicle simulation by reducing the time between inputs from the driver and responses from the system during what is called ‘driver-in-the-loop’ (DIL) simulation. The software is based on closing the loop through the driver as quickly as possible while providing very high bandwidth video and audio feeds to him or her, and high bandwidth road surface detail to the vehicle model.
This facilitates the accurate simulation of handling, active safety systems, ride, NVH, control system integrity and much more. The leading vehicle modelling tools used to study vehicle dynamics are already at the necessary level to allow DIL simulation. The missing links have been suitable high-bandwidth software to close the loop quickly enough through the driver, and motion platforms with sufficiently low inertia to provide quick enough responses.
This enables vehicle manufacturers to identify a whole range of potential issues very early in the engineering programme when they are relatively easy and cheap to fix. The alternative is to wait until prototype vehicles are available for test and the consequences of any changes are more serious.
What is unique about your technology?
How well do you really know your competitors?
Access the most comprehensive Company Profiles on the market, powered by GlobalData. Save hours of research. Gain competitive edge.
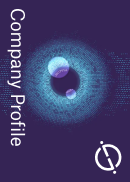
Thank you!
Your download email will arrive shortly
Not ready to buy yet? Download a free sample
We are confident about the unique quality of our Company Profiles. However, we want you to make the most beneficial decision for your business, so we offer a free sample that you can download by submitting the below form
By GlobalDataFor the first time, vehicle manufacturers can simulate vehicle dynamics with sufficient realism to develop chassis systems with a human driver in a virtual environment. The complex interactions between dynamic systems, such as passive chassis behaviour, electronic stability control and driver workload management can be studied more effectively, in complete safety, with a level of repeatability not possible in ‘real world’ testing. For example, the evaluation of active safety systems is transformed by the ability to repeat limit manoeuvres, time after time, without variations in tyre grip, cross wind and other conditions.
Previously, simulators were too slow to respond to driver input due to a combination of hardware and software limitations. This restricted their use to human factor studies or man-machine interface development, such as driver fatigue research and the development of cabin ergonomics.
Who are your key development partners and what do they bring?
We work in partnership with the major motion platform producers, such as McLaren, Moog and Ansible Motion, who act as full systems integrators and can deliver complete turn-key systems if required. McLaren and Ansible, in particular, offer light, fast, high-bandwidth motion platforms that are very appropriate for vehicle dynamics applications.
In terms of vehicle modelling, rFactor Pro wraps around all the main tools, including Dymola, SIMPACK, Simulink, AVL-VSM, CarSim, CarMaker, LMS AMESim and VI-Grade. Over the last year we have been working with most of these vendors implementing native interfaces to our new TerrainServer product. The industry standard for simulated road surfaces is too slow so we had to develop our own, TerrainServer. It offers road surface data in a real-time, very high bandwidth, feed to the simulation’s tyre model. This is essential for driver-in-the-loop applications as we have to be able to run real-time, yet to deliver good quality feedback in the upper frequencies, e.g. for ride and impact harshness, we need to be feeding large volumes of very accurate data into the vehicle model.
Regarding software platforms, we have also been working very closely with Concurrent Real-Time over the last year, and we now have native rFactor Pro builds that run on Concurrent’s RedHawk real-time Linux and SIMulation Workbench. Concurrent has done a lot to raise the bar in the area of real-time performance and our customers are now starting to see the benefits of a software-platform that runs on very high performance, off-the-shelf hardware – all under the control of Concurrent’s SIMulation Workbench. Platforms like Concurrent are making it increasingly easy for us to leverage the benefits of multi-core systems, with multiple models in a hard-real-time environment.
What have you learnt from using such technology in the F1 arena?
In F1, the only consideration for a driving simulator is its value as an engineering tool for vehicle dynamics applications. There are no requirements for ergonomics or human factors studies, and given the level of experience of most of the drivers there is very limited use for driver training. What matters is that you can use the simulator to evaluate new designs with a real driver in control.
Our six years in F1 have taught us that there are two crucial areas to focus on for vehicle dynamics applications: low-latency and achieving high-bandwidths while running real-time. We need high-bandwidth data from the road surface into the tyre models and we need high bandwidth video fed back to the driver to create a detailed, realistic and immersive environment. Over the last two years, as we have implemented similar systems at automotive OEMs and Tier 1 suppliers around the world, we’ve learned that these two fundamentals are just as critical to the success of their simulators, so in that regard, we genuinely are seeing technology transfer from F1 that directly benefits large scale automotive manufacturers.
We understand that simulators used for auto applications are typically heavy units but this is changing?
Simulator technology evolved from the aerospace industry and, because even a fighter plane has a much slower rate of turn than a car, the inertia of the platform was not an issue so traditional simulators can weigh thousands of kilos. New designs using rFactor Pro software can weigh as little as 250kg, allowing them to move faster and respond more quickly. Vehicle dynamics simulators, used for example for chassis development, active safety and control systems development need small, light, stiff platforms capable of more immediate response to provide good handling and ride cues – our requirements are very different to those of traditional procedural simulators which are often massive and relatively slow.
The reduction in weight has also been helped by removing the entire graphics system from the motion platform, using optically correct images projected onto cylindrical screens. This is made possible by our high bandwidth, low-latency vision system using multiple image-generator PCs.
To reduce latency, we use direct hardware interfaces for the audio and video pipelines, with no graphics buffering. Our video pipeline is about 1.5 frames faster than the industry standard Open/GL, while maintaining channel synchronisation across all the projectors to within 100µs. Our direct audio pipeline shaves 60ms from the standard Windows drivers.
Where is simulator technology going next?
The remainder of this interview is available on just-auto’s QUBE research service