Carbon fibre reinforced plastics have been drawing industry attention as their lightness and strength can help the fuel efficiency of vehicles, but the time-consuming work required to produce the materials is a drawback. Here, Matthew Beecham talked with Gary White, engineering manager, Prodrive Composites about the use of carbon fibre in vehicle manufacture.
For some time, carbon fibre has been used in F1, aerospace and marine applications and appears to be making its way into vehicle manufacture. Where do you see the greatest opportunities/ applications for carbon fibre in mass produced cars?
Cosmetic enhancements are an obvious opportunity, where the customer would be willing to spend a reasonable, additional expense to upgrade his/her vehicle with interior and external trim components. In addition OEM’s are looking at the weight saving advantages of carbon fibre for suspension components and body panels, using RTM, press and thermosetting technologies to make the processing cost element cheaper, with higher volume capability. We are currently refining a process that will help substantially reduce the cost of certain carbon trim parts making carbon a more attractive option for a wider range of cars.
Do you think that carbon fibre automotive parts will remain an under the hood niche or could the material be used for medium to large production automotive parts?
The stumbling block to this happening has always been high processing and material cost and volume ability, but with advances in processes this is becoming more accessible. At Prodrive, we have already taken a number of intermediate steps, bringing cost down through process optimisation and novel construction techniques.
Why do you think it’s taken so long for the automotive industry to embrace carbon fibre?
How well do you really know your competitors?
Access the most comprehensive Company Profiles on the market, powered by GlobalData. Save hours of research. Gain competitive edge.
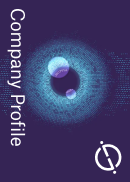
Thank you!
Your download email will arrive shortly
Not ready to buy yet? Download a free sample
We are confident about the unique quality of our Company Profiles. However, we want you to make the most beneficial decision for your business, so we offer a free sample that you can download by submitting the below form
By GlobalDataThe whole cost model has not been appropriate. There have also been issues with repairability. This is less critical in very expensive cars that can be returned to the manufacturer, but in volume applications there has to be a local solution that accommodates the fixing systems with the accuracy needed to ensure original crash performance is returned.
Carbon fibre has clear advantages over steel thanks to its lightness and strength yet the time-consuming work to produce materials is a drawback. What’s your view?
This is exactly the case; one other drawback is also the recyclability which is still a potential stumbling block, however there are a number of people looking into effective ways of recycling carbon and I am sure that as was the case with tyres an effective solution will be found.
What are the challenges with joining certain lightweight composites?
The main concern is ensuring the consistency and robustness of the process. Any bonding operation is dependent on correct preparation and application of the system used. Any testing requirement to give confidence in the process would have prohibitive cost and capacity implications.
Can you envisage cheaper, easier-to-form alternatives to carbon fibre?
Materials are constantly being developed and refined, but carbon fibre remains the most available, light-weight, high-strength alternative to metal. The next light-weight, easier-to-form alternatives to steel will most likely be derivatives of carbon fibre that allow faster, fully-automated processing.
It appears that processes to manufacture carbon fibre have moved faster than those for recycling it. Are there still challenges when it comes end of life recycling of carbon fibre parts?
Absolutely, this is also the case for aerospace when you consider large commercial aircraft are now manufactured using carbon composite. There is a lot of research into the recycling of carbon fibre and I am sure it will not be long before an effective process is established. With the dramatic increase in the use of carbon I am sure someone will make a very profitable business from it.