A team of researchers at Nottingham University, led by Professor Steve Pickering, Hives Professor of Mechanical Engineering, are developing processes to recycle carbon fibre composite materials, including developing applications for use of the recycled carbon fibre. Matthew Beecham talked to the Professor to find out how these processes can be applied to the automotive industry.
It appears that processes to manufacture carbon fibre have moved faster than those for recycling it. As we understand it, your team has developed ways to recycle carbon fibre composites. Could you explain how your process works?
We have investigated a couple of processes for recycling carbon fibre composites.
A fluidised bed process in which pieces of scrap composite are fed into a bed of sand particles fluidised with air. At a temperature of around 550°C the epoxy resin form the composite decomposes. This releases the carbon fibres which are carried out of the fluidised bed in the air flow. They can then be separated from the air. The fluidised bed process produces good quality clean fibres and has the advantage of being tolerant of contamination as it can separate metallic materials from the carbon fibre. But the epoxy resin is recovered as energy.
A process in which a supercritical fluid is used to effectively dissolve the epoxy resin from the composite leaving good quality carbon fibre. We have investigated propanol as the fluid at a temperature and pressure above the critical point at which it has very good solvent properties. The advantage of this process is that it can recover useful chemical products form the epoxy resin in addition to carbon fibre.
Both of these processes have been developed to laboratory scale.
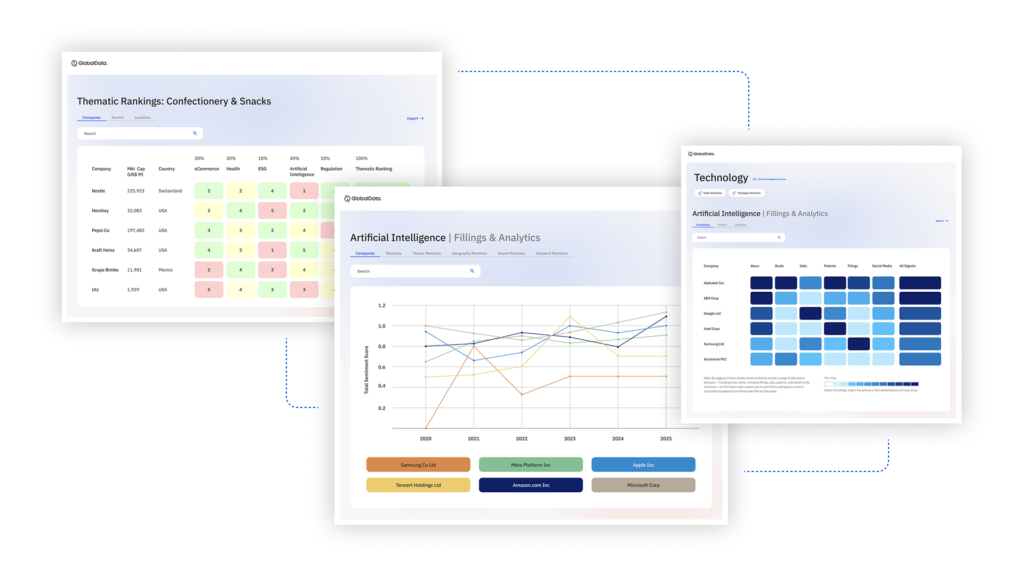
US Tariffs are shifting - will you react or anticipate?
Don’t let policy changes catch you off guard. Stay proactive with real-time data and expert analysis.
By GlobalDataWhat sort of applications can use such recycled material?
The recycled fibres are short individual filaments in a fluffy form. They can be used for a range of applications, including:
- Milled to <1mm for use as a conducting filler for anti-static applications or other specialist applications requiring a high stiffness low density filler.
- Reinforcement in bulk moulding compounds.
- Reinforcement in thermoplastics – but the fluffy fibres must be turned into pellets or some other form that can easily be fed into injection moulding machines.
- Composite applications requiring greater proportions of carbon fibre require intermediate processes. Wet lay, papermaking type processes can be used to produce a non-woven mat that could be used for intermediate grades of composite. But fibre alignment is required in order to produce composites with the highest proportions of carbon fibre that might compete with virgin carbon fibre in some non-structural aerospace applications and other high grade applications in the automotive industry.
Are there still challenges?
The main challenge is to be able to process mixed and contaminated end of life composites. Most of the R&D done so far has focused on relatively clean waste.
Your team has worked closely with Boeing yet what are the prospects for transferring this technology to the automotive industry?
The technology that we are working on with Boeing would generally be applicable to recycling carbon fibre from any industry and so could be applied to the automotive industry if viable applications were identified.
Where do you see the greatest opportunities/ applications for carbon fibre in mass produced cars?
Carbon fibre has unique structural properties that mean that it can be used to make the lightest structural materials. So it has the potential to make very lightweight cars that could help to reduce fuel consumption and carbon emissions. So there are great opportunities to use it in the vehicle structure.
Do you think that carbon fibre automotive parts will remain an under the hood niche or could the material be used for medium to large production automotive parts?
Carbon fibre is already used extensively in Formula 1 and other low volume cars as a structural material. Given greater emphasis on reducing fuel consumption it is likely that more carbon fibre will be used in larger volume in the future in vehicle structures.
Why do you think it has taken so long for the automotive industry to embrace carbon fibre?
The remainder of this interview is available on just-auto’s QUBE research service