The market for electrically-assisted steering systems continues to blossom. Demand is being fuelled by a range of factors, not least that electric systems are more economical to run, lighter, recyclable and easier to package and install compared to conventional hydraulic systems. Continuing just-auto’s series of interviews with global steering manufacturers, Matthew Beecham talked with Paul Poirel, Chief Product Engineer, Europe, Nexteer Automotive.
What are the issues affecting the speed at which the car industry phases out hydraulic power steering and phases in electric power steering?
The switch to electric power steering (EPS) is being driven by the need to reduce fuel consumption and CO2 emissions. Because it only provides assistance on demand – when turning the steering wheel – replacing a hydraulic system with EPS can improve fuel economy by up to 4 percent and carbon emissions by up to 8g/km.
The increasing use of EPS is also helping to integrate the steering with safety functions such as lane-keeping, stability control, or driver convenience functions like pull compensation and torque steer control. More advanced software and electronics are allowing us to implement much more seamlessly, cost-effectively and with greater levels of optimization.
The migration to EPS has been slowest in larger vehicles because the rack forces required are higher and more challenging. Our rack-assist EPS can provide rack forces of more than 15kN and is used on the Ford Mustang muscle car and F-150 pick-up truck. The system’s low-friction, inertia-compensated, means the steering gives the driver the same performance and feel as a hydraulic system, but with a substantial improvement in fuel economy.
How much pressure is there on suppliers to add more electronic functions into their systems? How is this affecting the strategies of Tier One suppliers?
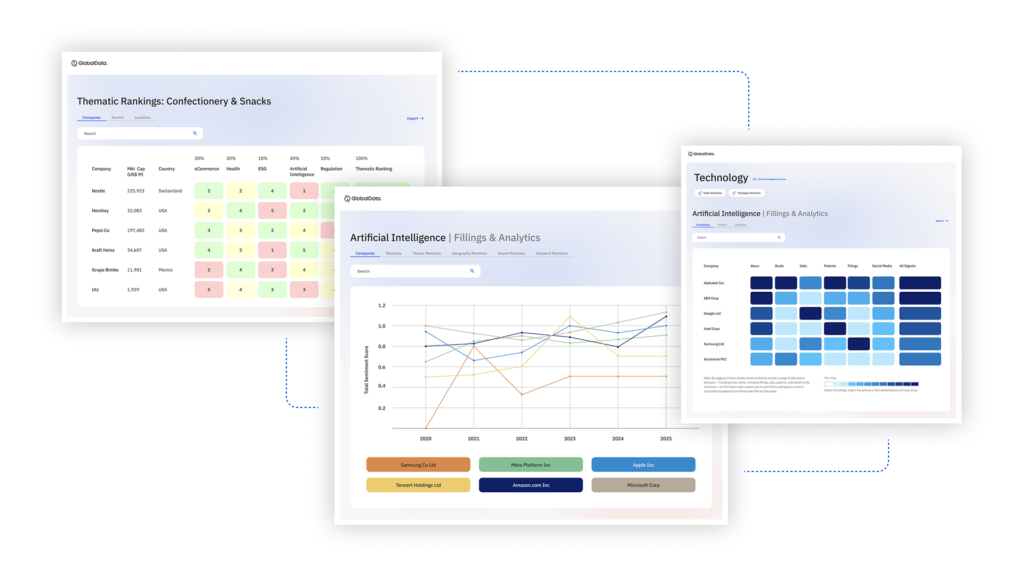
US Tariffs are shifting - will you react or anticipate?
Don’t let policy changes catch you off guard. Stay proactive with real-time data and expert analysis.
By GlobalDataThe amount of memory and processing speed that steering systems require is growing rapidly. There are a number of causes: the introduction of new functional safety standard ISO 26262, increases in the number of electronic vehicle functions, new communications protocols and the introduction of standardized Autosar software.
To meet the need for increased processing power, Nexteer is introducing a new electronic architecture with far greater scalability than is possible with current systems, and built-in safety enhancements. To give the most cost-effective solution for each application, electronics architectures will have to be modular and flexible.
At the entry level, carmakers need a simplified control platform that offers a cost-optimised system for entry-level cars and emerging markets, with the flexibility to add more sophisticated features for future models. For premium platforms, modular architectures allow a high level of additional features to provide a wide range of options and a development path into the future.
The usual approach by suppliers has so far been to maximize the volumes of standardized units in order to drive down production costs. But standardized systems built from high-end requirements end up carrying redundant features that are required only by certain customers, resulting in over-specification of the product for many applications.
What are you doing to exploit the greater levels of functionality in steering systems?
There are additional functions that add real value for the OEM and which improve the brand experience for the driver. An example of this is wheel imbalance rejection. Our in-house software developers have created code that filters out uncomfortable wheel vibrations from the steering and this has significantly reduced warranty costs for customers. A key enabler is to have in-house software capabilities in order to constantly innovate and introduce new steering functions with a fast time-to-market
What signs are you seeing that OEMs will retain 12-volt architectures in vehicles?
Not everything will be a 12-volt system in the future, but it makes sense from a cost-perspective to keep as much as you can running on 12 volts. Managing the vehicle’s energy demands is much simpler. We have successfully developed 12-volt steering systems for large North American SUVs and pick-up trucks, despite the very high rack force requirements.
How does the increasing electronics/software content of systems affect the way that the industry develops new technologies?
The remainder of this interview is available on just-auto’s QUBE research service