Back in the 1970s, a car seat was a functional component with few or no added value features. Nowadays, with drivers spending more time in their car on longer commutes, they expect a comfortable ride. Matthew Beecham caught up with three top executives of Lear Corp to hear how the seat has become an integral part of the car’s overall design and appeal in the showroom. Here, Ryan Burns, Lear’s Vice President of Global Seat Engineering led the discussion with contributions from Karl Henn, Director of Seating Engineering and R&D and Mandy Sarotte, Vice President of Global Trim Sales.
The CAFÉ standards require automakers to nearly double fuel economy to 54.5 mpg by 2025, starting in 2017. This leads to pressure on the need to reduce weight of car seats. Could you tell us how your business is developing seats that help achieve this goal?
With Lear’s market observations regarding the global trend towards weight reduction, Lear has taken – and will continue to take – significant steps to address this need. Lear has been involved in many non-ferrous, lightweight seating programmes, both in the past and in future development.
Also, Lear holds multiple patents related to seat structures using alternate materials.
Lear has been developing full carbon fibre front row seating systems for over ten years, including the Ford GT, Porsche 911 GT3 and Lexus LFA.
Magnesium structural components are used in our products for Ferrari, Mercedes and Maserati, and composite reinforced materials are used in Corvette, Audi and many rear seat structural applications.
How well do you really know your competitors?
Access the most comprehensive Company Profiles on the market, powered by GlobalData. Save hours of research. Gain competitive edge.
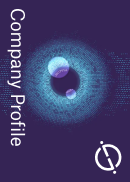
Thank you!
Your download email will arrive shortly
Not ready to buy yet? Download a free sample
We are confident about the unique quality of our Company Profiles. However, we want you to make the most beneficial decision for your business, so we offer a free sample that you can download by submitting the below form
By GlobalDataSemi-structural foams and expanded materials are a large part of Lear’s DECS technology and are core to our continued penetration into low cost, lightweight seat structures and systems. This product supports all segments of vehicle, from base sedans to luxury vehicles.
Although weight reduction is crucial if the auto industry is to meet the CAFÉ standards, is there a negative perception of thin seats amongst consumers? How can you make seats thinner yet maintain seat integrity?
Lear’s market research has never indicated that thin seats are not well perceived among consumers. In fact, thin seats are perceived positively at large and exceptionally so within sports car and performance products. These thin seats provide a “sporty” aesthetic – as well as creating more space within the vehicle – which rates highly as a customer want.
A seat’s structural integrity is only loosely tied to the fore-aft sectional thickness, and Lear has created extremely thin seats for many customers in the past.
Comfort is sometimes cited as a roadblock to thin seats, but using Lear’s proprietary ComforTec system in conjunction with our Crafted Comfort Connect technology, Lear has been able to create multiple thin, light, extremely comfortable seats for performance and luxury car manufacturers such as BMW, Ferrari, Porsche and others.
In terms of the seat structure, to what extent is there a greater use of aluminium (or steel and aluminium combined) in manufacturing either the front or rear seats?
Steel is the primary structural material used in the seating industry. The combination of low cost, high energy absorption, well-known and high capacity forming and joining technologies, and a long history of good performance all help to make steel an excellent structural choice. Specialty, non-ferrous materials have begun to penetrate the market, primarily due to their enhanced strength/weight ratio. In response, the steel industry has developed new, better performing, lighter alloys. Although specialty materials will continue to have their place, the medium-term outlook still shows steel as the dominant material in seating applications.
As we understand it, a key trend that within five years is that more than 60 percent of cars will have lighter coloured interiors, which presents more of a challenge for keeping the seats clean. How is Lear addressing that challenge?
Material protection is a significant need for interior surface materials and Lear has responded by producing its TeXstyle Defense protection system. TeXstyle Defense is a layered system, offering various levels of protection depending on the customer’s preferences. It can protect light coloured materials from stains, bacteria, static, dust, and many other degrading effects that lead to customer dis-satisfaction. This technology will allow vehicle designers greater flexibility in colour and style choices without the significant concern of warranty and degradation that have traditionally accompanied these selections.
I guess leather and leather-look fabrics have always been classical materials used in cars and they are still very much a status symbol reflecting luxury and hence always favoured by customers. As some people down-size their vehicles, do they still want some genuine materials such as leather in their cars available as optional?
Premium materials are an extremely high “want” from consumers in all vehicle segments. The seat is the first large component that a consumer sees when opening the door and the seat surface material is on constant contact with the occupants. Fuel and size-conscious consumers still desire the entirety of the feature enhancement, comfort, and styling that is available, regardless of the size of vehicle they select.
With so many devices and materials stuffed into new vehicles seats these days, is there competition for real estate in the seat?
The largest driver of seat thickness is seat content. With the incorporation of side airbags, heat/cool systems, active head restraints, multi-contour comfort systems and increased power feature proliferation, significant development effort has been required to ensure that the seat thickness has not grown significantly.
Designing seats to meet the needs of all occupants is a tough challenge. Could you explain how you set about understanding the many needs of drivers and passengers and how those needs vary between, say, China and North America?
The remainder of this interview is available on just-auto’s QUBE research service