Vehicle simulators have changed beyond recognition in the past few years. Developments in responsiveness, graphics, together with improvements in vehicle and road surface modelling fidelity mean that today's simulators offer the potential to do much more. The 'driver in the loop' sector has seen the most development with simulators now relevant for subjective and objective assessment of vehicle and component performance where a human driver is required, such as emergency situations or even the introduction of autonomous cars. Matthew Beecham spoke to Kia Cammaerts, founder of Ansible Motion, a designer and manufacturer of engineering-class driving simulators for ground vehicles.
Could you tell us a little more about Ansible Motion?
Of course. I initially founded sister company Ansible Design in 1998. This division specialises in creating high quality simulation tools for motorsport. One such product that is widely used for motorsport and high performance road cars is AeroLap. This can be used to predict and analyse maximum vehicle performance over a defined path, such as a race track. In 2008, we had the opportunity to look at developing a full scale driving simulator. Rather than simply copy what was out there – mostly technologies lifted from aviation applications which may or may not be well-suited to cars – we literally got out a clean sheet of paper and looked at how we could create an immersive experience for drivers of virtual vehicles. This led us to consider entirely new motion machinery and motion cueing strategies, and ultimately an entire suite of simulation products we define as 'engineering class' simulators.
What is an engineering class simulator and how does it differ?
Although this may sound counter-intuitive at first we are not actually trying to replicate, G for G, a real vehicle's accelerations. That actually can't be done with any simulator since great size would be required for even simple things like driving around in a circle in car park area. Instead, we seek to create a virtual environment so that the driver will interact with a virtual vehicle in a realistic way, behaviour-wise. Our engineering class simulators differ significantly from, say, human factors simulators or entertainment simulators and this is an important distinction when considering simulator use cases. For example, one might guess that important cues for a common driver would be a little different from that for an expert or professional driver. Also, one might expect that vehicle engineers might interrogate simulation data differently than others. This influenced our definition of what a vehicle simulator should be, and it's evident in how we build our simulators. As a small but relevant example, professional drivers are typically very sensitive to vehicle stability – or lack thereof – in certain situations, so we might find that a simulator's yaw rotations together with lateral and longitudinal movements are especially important. We think we have created a range of simulator solutions that are well-suited for those engaged in vehicle engineering work.
The design is compact – can you offer a similar experience to the larger simulators?
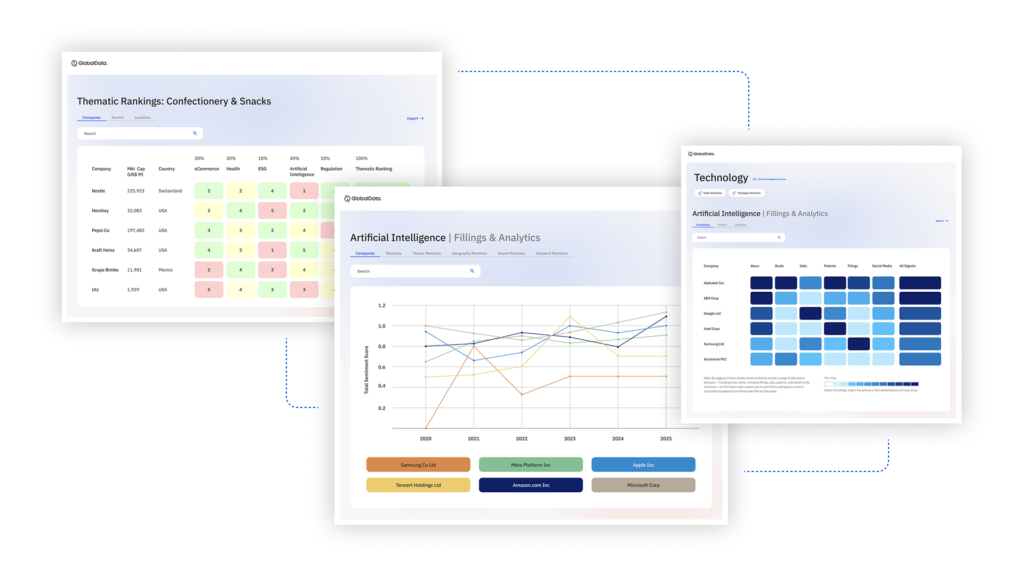
US Tariffs are shifting - will you react or anticipate?
Don’t let policy changes catch you off guard. Stay proactive with real-time data and expert analysis.
By GlobalDataOur simulator footprints on the whole are quite large -perhaps larger than other simulators since we typically use large projection systems and display screens. But yes, our 6DOF (six degrees-of-freedom) motion platforms themselves are quite compact and we are very proud of this. Interestingly, though, we have found that the smaller-and-lighter-is-better maxim requires some explanation. It is widely understood conceptually that performance is inversely related to mass for dynamic machinery, but we still find that a factory demonstration is the most convincing evidence that our motion space is actually significantly larger than many of the really large simulator systems out there. But actually it's what you can't see that really differentiates us.
Is that the software element?
There is that element, yes, but Ansible Motion believes that it is the driver's emotional involvement that is the key for creating a high quality simulation experience. The human body is adept at controlling vehicles designed to suit our abilities but if we receive feedback that does not fit with what we expect then we become disoriented and confused. This is a key element behind some drivers experiencing motion sickness in DIL (Driver-In-the-Loop) simulators. In fact, simulator sickness is so prevalent that it has even earned a special name – Simulator Adaption Syndrome or SAS. We felt so strongly about these emotion and expectation elements that we embed detailed mathematical models of human anatomy – such as vestibular system models – right into the motion cueing and control algorithms of our dynamic simulators. This human modelling aspect is not unusual in the world of simulators – but what is unique about our approach is the uncompromised way in which we implement human modelling. We can achieve this because our motion control and hardware is up to the task with sufficient headroom to simulate even extreme dynamic situations.
What exactly does this do?
Simply put, the motion has to be correct and delivered in a timely manner. The human vestibular system comprises the semi-circular canals and otoliths of your inner ear. These tiny parts of the body are affected by inertial stimulation and are a key part of your spatial awareness and balance. Factoring this directly into our motion control algorithms fundamentally increases the realism in ways you can experience. When we immerse a driver into a compelling environment and ensure their perceptions are in line with the vehicle behaviour on the road, we can conduct excellent simulator experiments – experiments useful to engineers who are working on vehicle dynamics or vehicle subsystem deployments.
The visual aspect must still be important and aren't there other cues that are needed?
Yes, visual feedback has to correct in order to have a real sense of velocity and location in the worldscape. The motion and vision must be highly synchronised as well, in order to avoid sickness and disorientation. In the area of graphics and image generation, we get on well with companies like rFpro – because they understand the importance of low latency image generation and synchronisation with complex tool chains. Of course, we can also add other cues such as audio and haptic feedbacks through the steering wheel, seat, the pedals, and so on. We can do seatbelt tensioners, for example, but we class all those as supplemental layers on top of the crucial inertial and visual stimulants that are informing the driver.
Do drivers notice the difference in your approach?
Yes, most do and we can tune our simulators to appeal and be effective to a wide range of end users. We have had a number of current F1 drivers in our factory simulator in Hethel and they tend to be surprised how much more emotionally involved they are in the driving experience. For example, we are always delighted when drivers complete a simulator session and begin speaking immediately and enthusiastically in terms of a real car, offering suggestions about tuning actual parts – dampers, tyres, and such. To us this means that they are not getting hung up on any unrealistic aspects of the simulator experience and are ready to communicate with engineers about the thing they are familiar with – the car.
We believe we are much more about the human side and see simulators as the bridge between drivers and engineers. We recently had a visit from an OEM chassis engineer who came to see our simulator in action. When she saw the sim running and was able to work with the driver, there was a genuine connection moment. She said she could actually now see for the first time a particular issue that the driver had been trying to explain but they just couldn't convey or show the problem with data alone. In this particular case, the range of movement we offer over other simulators meant she could actually see the issue and start to talk with the driver about it in real time. It put the driver and engineer right into each other's worlds and, well, this goes back to that emotional link again – that is the Ansible difference.
You mentioned F1. Is motorsport where most of your business lies?
We have roots in F1 and have F1 customers. But actually, no, these days most of our business is with the OEMs. We have now deployed a number of bespoke simulators around the world, ranging from stationary systems through to full-scale dynamic DIL simulators. We are passionate about the engineering aspects of what we do, and we connect well with our customers since they are equally passionate about their pursuits.
How versatile are your simulators? Can you give examples of how Ansible Motion simulators are being used by car manufacturers or suppliers?
The remainder of this interview is available on just-auto's QUBE Global light vehicle safety systems market- forecasts to 2030