In June 2008, Delphi put its global exhaust systems business up for sale which consisted of mainly hot-end exhaust components, including design and manufacture of the front-end module with catalytic converters and exhaust manifolds. A few months later, Mexico’s Bienes Turgon stepped forward to buy the business. Bienes Turgon officially took over operations on 1 May 2009 under the name, Katcon Global. In this interview, Matthew Beecham talked with Jose De Nigris, executive vice president, sales and engineering, Katcon Global, and Bob Houtschilt, vice president, business development, Katcon Global.
just-auto: How has your business shaped-up over the past two years?
Jose De Nigris: Less than two years after seamlessly absorbing Delphi’s exhaust business globally, Katcon has already seen bright prospects for the future of our company and the industry in general.
We are convinced that exhaust and aftertreatment is a growth industry and are prepared to help our customers face the challenges that lie ahead in this field for gasoline and diesel vehicles, and engines in general.
From very small engines and light duty applications, all the way into enormous heavy duty and industrial applications, our global, experienced and diverse team, with a presence in the United States, Mexico, Venezuela, Luxembourg, Poland, South Africa, India, Australia and China, as well as in Korea through our alliance with industry-leader KDAC, reaffirms our commitment to the industry and our readiness to become one of the key suppliers in the industry.
We have been able to grow not only our manufacturing capabilities worldwide, but also our team’s abilities and competencies, from analysis, design, engineering and development, to specific R&D initiatives; we continue to expand our testing capabilities and have strengthened our relationships with the supply chain, a key element of our business.
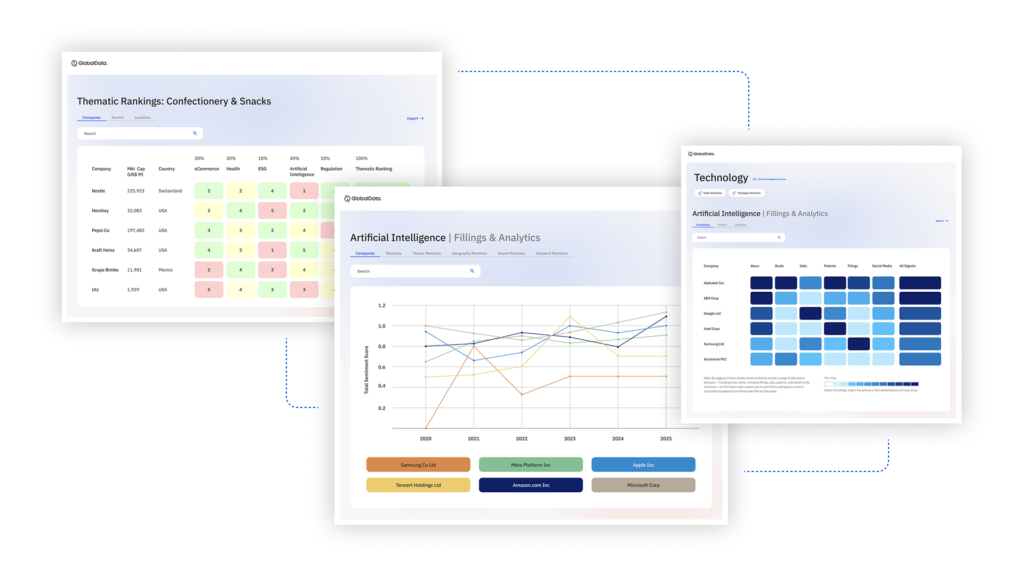
US Tariffs are shifting - will you react or anticipate?
Don’t let policy changes catch you off guard. Stay proactive with real-time data and expert analysis.
By GlobalDataIn short, Katcon is already working on projects that address concerns in vehicle size reduction; this brings not only packaging concerns for customers, but additional thermal and durability factors that need to be solved. We are focused in providing technical and practical solutions from manifold to tail pipe to a variety of customers and applications around the world.
The current trend on gasoline engine, at least in Europe, is the downsizing linked with introduction of turbochargers. For example, a 1.6-litre North America gasoline becomes a 1.2-litre turbo gasoline. In what ways has this trend affected the exhaust system?
Jose De Nigris: Downsizing is a trend forcing exhaust system suppliers to adapt their systems since the engines will deliver exhaust gases with high flow rates. The hot-end attached to the engine turbocharger needs advanced modeling tools to be optimized in terms of structure and flow. A special focus will be given to flow in order to optimise the catalyst usage and reduce PGM loadings. Noise treatment will be also treated accordingly since the high flow rate and the turbocharger will introduce different tuning needs.
Bob Houtschilt: Packaging more content under the hood also brings challenges for thermal management. This will also change the way in which exhaust systems and modules are manufactured.
The economic crises has led to a change in customer behaviour and switching to smaller and smaller vehicles. In terms of exhaust and catalytic systems, does that pose technical challenges?
Jose De Nigris: It mainly forces exhaust suppliers to use modern and sophisticated analytical prediction tools in order to optimise the designs along with downsizing. Looking for more compact and lighter designs goes well together with downsizing.
Bob Houtschilt: Customers have been down pricing their vehicles, as well as downsizing. Lower price vehicles still need long lasting exhaust systems to meet emissions legislation and customer expectations but with greater value in terms of useful life, acoustic quality and engine performance.
Although a lot has been said about the prospects for PEVs, the IC engine will be around for the foreseeable future. How do you see the powertrain market over the next 5–10 years?
Jose De Nigris: The exhaust system will mainly remain the same in terms of demanded functions but the duty cycle will be very different. For instance, the more frequent start and stop of the IC engine will lead to more “cold” starts. The heat recovery systems introduction tendency can be very helpful to provide heat to batteries. This will be a general trend exhaust system suppliers must take in account.
Another important field that might require attention is the overall vehicle noise when operating with the electrical engine only. This might be a good opportunity to use our noise expertise in providing ways to produce noise!
As far as gasoline engines are concerned, after-treatment systems appear to be on a level although we understand that there is some development work underway to control thermal management. What do you see happening with respect to gasoline engine after-treatment systems these days?
Jose De Nigris: In terms of emissions, the major effort will be directed towards reduction of catalyst cost through compact designs with optimised flow and heat management. If gasoline lean burn engines are introduced, NOx aftertreatment will require complex exhaust systems just like for diesel engine. PM numbers might also force gasoline lean burn engine to use some kind of soot aftertreatment.
For some time, we seen how carmakers have paid close attention to exhaust sound in order to maintain and enhance its “brand”. How do you set about supporting the carmakers achieve the right note?
Jose De Nigris: Overall noise and second order noise are very important to customers and we are already supporting them using analytical tools, vehicle measurements and subjective noise assessment.
Bob Houtschilt: Other than performance cars, most auto makers have settled on “quiet”. Achieving a quiet exhaust with low back pressure for engine performance with more and more crowded under body space is the challenge. Our advance modelling and advanced laboratory equipment enable us to optimise sound, performance and value.
I guess because of the increasing cost and price volatility in the precious metal markets, this is forcing manufacturers to squeeze more performance out of smaller catalysts. Is that how you see it?
Jose De Nigris: The exhaust supplier effort resides in canning the small catalyst while improving flow and thermal management to optimize cold start performance and minimize catalyst aging. This activity requires a strong virtual development expertise along with a good understanding on how the catalyst and engine management system works.
Is there a trend toward using multiple exhaust gas sensors in order to deliver the performance improvements and reduced catalyst size?
Jose De Nigris: The trend is definitely there for diesel systems: more temperature sensors, introduction of specific sensors like NOx, ammonia or PM sensors. There is a trend toward using more O2 sensors for gasoline engines to better fine tune air fuel ratio but this has started already a few years ago.
Bob Houtschilt: Some customers are moving to individual cylinder measurement. There are a variety of ways to achieve this. For exhaust suppliers, a key challenge is to optimise gas flow for converter efficiency and sensor performance.
For some time, we’ve seen increasingly stringent emission legislation introduced leading to the exhaust after-treatment system becoming more complex, particularly for diesel engines. What lies ahead for diesel after-treatment systems?
Jose De Nigris: The major challenge for diesel engines will be to have all the required technologies helping to close the “historical” gaps like NOx and PM but still keep cost low and the other “historical” advantage, low CO2, still valid. Systems like DPF, NOx traps and SCR are great to reduce emissions but tend to increase CO2 emissions.
Bob Houtschilt: There are still advances to be made in engine management, fuel systems and even the fuel. Aftertreatment will see a convergence of oxidation catalyst, urea or diesel injection for NOx, and the inclusion of filters with the addition of diesel injection. Thermal management, flow management and structural durability to provide long lasting parts will be the key to minimising cost and mass.
Finally, in terms of developing increasingly complex exhaust systems, how do you manage the delivery of those systems yet keep lead time and costs under control?
Jose De Nigris: The key for success resides in having in house system expertise and advanced virtual development tools requiring complex modelling activity. By system, one should understand exhaust system but also the overall aftertreatment system (catalyst, fuel management, urea management etc.). The challenge for industry competitors is to achieve all this with a lean and cost effective business model that allows them to support increasing customer requirements, pricing pressures, and the necessary financial health that sustains company stake holders in the long run.