JSP is the world leader in the production and development of Expanded Polypropylene (EPP) and its applications, branded as ARPRO. An essential product for the automotive, packaging and consumer product industries, ARPRO is a source of strength, durability and weight reduction and is used in over 23,000,000 vehicles per annum. just-auto talked with Paul Compton, executive vice president and chief operating officer of JSP (Europe).
just-auto: Could you sum up the main properties and advantages for automotive OEMs in using ARPRO EPP?
Paul Compton: ARPRO expanded polypropylene can reduce system mass from 25 to 35 percent in systems like seating. It is inert, unaffected by exposure to oil, grease, petroleum and most chemicals. For safety, it has an extremely high strength to weight ratio, quickly returns to its original shape following dynamic stress, withstands multiple impacts without significant deformation and provides acoustical enhancement in components used throughout the vehicle.
just-auto: The dimension creep syndrome is making each successive generation of cars heavier, so what is JSP doing to assist the auto industry in making lighter cars?
Paul Compton: I believe we can offer the OEM and systems supplier a solution that can take kilos out of a car and this can be in many areas. On a recent example, the new Volvo XC60, we helped replace the anti-submarine ramp, traditionally a body-in-white element, with a moulded ARPRO unit. Not only did this deliver a weight saving, therefore improving fuel economy and responsiveness, but it also considerably simplified costly body-in-white tooling. ARPRO is strong and resilient enough to enable the ramp to be incorporated into the seat, replacing the traditional metal structure and contributing to a simpler vehicle platform. Tooling costs are also lowered.
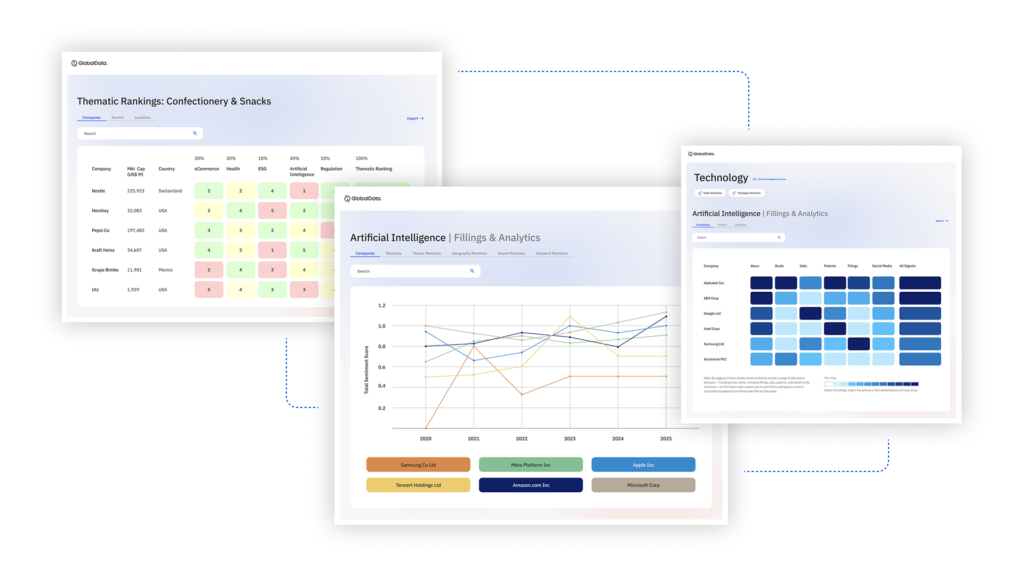
US Tariffs are shifting - will you react or anticipate?
Don’t let policy changes catch you off guard. Stay proactive with real-time data and expert analysis.
By GlobalDatajust-auto: How are the tooling costs reduced?
Paul Compton: Hatchbacks, MPVs and SUVs engineered on the same platform have differing H-Points, where the passengers’ seat heights are raised in relation to the ground. The H-Points are usually created with tool inserts or different tools. Using ARPRO, the variants can be accommodated in the seat itself simplifying costly metal pressing tooling to a single variant. This reduces tool changeover, maintenance and complexity.
just-auto: Does the seat therefore become more difficult to manufacture?
Paul Compton: No. Parts are consolidated. In fact we have developed a J-clip arrangement for attaching the upholstery to the seat bench. Serviceability and assembly are also easier, demonstrating that through good relationships with the OEM and tier ones we can deliver benefits through all areas.
just-auto: So what are the benefits to the end customer, i.e. the consumer?
Paul Compton: In this example, the flat floor delivers a more efficient load space with fewer structural obstacles when the seat is folded. This can make the car more marketable. In other areas of the vehicle, it can reduce noise, an attribute that can severely impact perceived quality. We think this is an area that car manufacturers are increasingly focussing on as powertrain noise levels continue to reduce. Our engineers work closely with tier ones and OEMs to create specific variants of the core product to deliver improvements. As an example, we have recently launched a low squeak application for sun visors and car interior trim. Sun visors are a prime example of noise generation, where the interaction between multiple materials creates alternating sound frequencies and noise harshness. Using the tailored ARPRO provides simpler moulded inserts, enhanced energy absorption, component consolidation, easier assembly, lighter weight and enhanced recyclability.
just-auto: Where else is the technology be applied?
Paul Compton: ARPRO is in the hidden areas, such as bumpers, stowage, consoles, and the ever critical safety impact zones. We are developing many space, noise and weight reducing products. We are also active in diverse areas such as the “Search and Rescue” markets, where ARPRO’s multiple impact resistance and high buoyancy properties are in demand. Solutions from other markets are very often transferable with automotive, and vice versa.
just-auto: Is the technology cost competitive?
Paul Compton: Absolutely. Through intelligent design we are able to minimise part complexity which can enhance piece and manufacturing costs. Our engineers work closely with OEM design and package engineers from the outset to maximise the benefits. ARPRO’s material capabilities such as strength or reduced mass mean it can be used to replace more costly or heavier components. These properties benefit the OEM right through vehicle life, simplifying servicing and recyclability. Our strong and close relationship with the OEMs is key to delivering this and we are proud of the levels of co-operation we enjoy with the vehicle manufacturers.
just-auto: What level of growth are you seeing across Europe, and in what auto applications?
Paul Compton: As an example, even before recent world economic changes, commercial forecasts for the European automotive industry for 2008 were only slightly up on 2007, by just 0.25 percent. By comparison automotive applications of EPP are forecast to rise by as by 6 percent despite the near-flat car production prospects. This is due to new application expansion such as the aforementioned seating where there are a lot benefits for the OEMs.
just-auto: What kind of challenges are you facing and anticipating with recycling and end of life regulations?
Paul Compton: ARPRO is 100 percent recyclable, easily recoverable, and as well as automotive components it can also be used for automotive dunnage. When producing ARPRO, the waste streams are water and CO2, with imperfect product being recycled on site. The water is screened for any solids and then released to the local water supply.
just-auto: Are there any future developments in ARPRO you can discuss?
Paul Compton: Amongst our ongoing tailoring and research activities, we are developing an improved surface finish for enhanced aesthetics and perceived quality. This will enable even more application growth.
See also: Global market review of vehicle seating – forecasts to 2014