When we last talked to UK-based technology company IDEAdvance, they had developed a sensor-less rotation detection, control and monitoring method for brushed DC electric motors. To find out how their technology has developed, Matthew Beecham talked with Jan Nottelmann, CEO and CTO of IDEAdvance Ltd and their technology partner, Brian Thompson, MD of Control Developments (UK) Ltd.
Could you update us on how you have advanced your technology?
Jan Nottelmann: Over the last couple of years we have met with a number of suppliers of electric motor applications to the automotive segment, in particular suppliers of power windows and seat systems. We have noticed a clear trend in the industry to move towards sensor-less electric motor controllers. The drivers for this are cost and weight reductions and improved reliability. Our patented, sensor-less DCM-MotionTechnology eliminates the need for sensors, sensor wires and connectors traditionally used in all the comfort systems you find in modern cars, and can potentially improve the motor lifetime. Therefore it is an attractive solution for the manufacturers. However, back in 2011 our technology was immature, i.e. we could talk about the technology and how it worked, but we could not demonstrate the performance in a real application, and that was a disadvantage. Therefore we have just finished the development of a sensor-less power seat demonstrator. We have already demonstrated this to a small number of customers and their response has been extremely positive.
What are the prospects for this technology to be applied to other industries?
Brian Thompson: I think the automotive industry remains the biggest opportunity because of the volume and the need to keep cost down. However positional actuators are used in the process and manufacturing areas, disability vehicles and wheelchairs, and the consumer/entertainment industry.
Jan Nottelmann: Motor rotation counting reliability is very important in automotive applications. With our demonstrator we can prove that we can count reliably the number of motor revolutions. For other applications using electric motor actuators – such as precision instruments and machines – counting resolution is very important. Our demonstrator uses an eight-slot motor and therefore has a counting resolution of 1/8 of a motor revolution, which corresponds to a position accuracy of 0.01 mm measured on the linear actuator in the system. Such high detection resolution cannot easily be obtained with traditional sensors.
How well do you really know your competitors?
Access the most comprehensive Company Profiles on the market, powered by GlobalData. Save hours of research. Gain competitive edge.
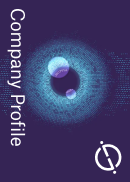
Thank you!
Your download email will arrive shortly
Not ready to buy yet? Download a free sample
We are confident about the unique quality of our Company Profiles. However, we want you to make the most beneficial decision for your business, so we offer a free sample that you can download by submitting the below form
By GlobalDataPresumably there are energy saving opportunities for BDC motors in EVs?
Brian Thompson: It is possible that by braking regeneratively at the right position we may recover kinetic energy, and reduce starting and stopping energy. However the technology may lend itself to improved longevity (by synchronised switching of the commutators), reduced EMC (by the same) and pre-emptive diagnostics by detecting changes in switching characteristics of the brushes.
As we understand it, your DCM-MotionTechnology can eliminate the need for sensors, sensor wires and connectors that are used around BDC motors. Could you possibly quantify the potential cost reduction and/or improved reliability, motor lifetime in a vehicle seat application?
Jan Nottelmann: Because the complexity of the automotive comfort systems vary a lot this is very hard to quantify. The automotive industry often looks to obtain savings of only a few pence in each of their systems. Replacing a sensor-system like a Hall sensor, magnet, wires and connectors in a single electric motor seat system with our technology may save in the order 20-25 pence. However, if you think of a more complex luxury car seat system with up to 12 motors in a single seat the savings become important. If you then include all the other seats and comfort systems driven by electric motors – often 100 motors or more are used in a modern luxury vehicle – our solution becomes very attractive in terms of saved cost and saved weight. We believe this is the main reason the automotive industry is showing an increased interest in sensor-less solutions for their comfort systems.
Brian Thompson: For the motor lifetime my instinct is that our solution will improve the lifetime of the motors, but more importantly it enables the manufacturer’s service organisation to detect when the motor is deteriorating before it fails. This increases long-term reliability and avoids unnecessary part changes.
Is all this development done in-house or have you formed any technology partnerships? And if so, what added-value does your partner bring?
Jan Nottelmann: Sensor-less DCM-MotionTechnology was invented by our parent company. IDEAdvance Ltd was formed in 2010 to further develop the technology, and we hold exclusive rights to commercialise the technology. The aim is to sub-license the technology to manufacturers of electric motor applications. In order to do this it is important that we can not only prove in a laboratory demonstrator that our technology works, but also prove that it works in a real environment or product. Control Developments has a long history of designing electric motor control solutions, which is why we are very happy that they have agreed to partner with us. This partnership will help to bring commercial solutions incorporating DCM-MotionTechnology to the market quickly, which should further help us to remove the entry barriers to much larger potential market segments.
Brian Thompson: The added value/benefits include: additional technical input to progress development more quickly, a large and diverse customer base, a greater level of integration support and technical problem support, wider exposure of the technology, credibility of the technology by using real-world application examples, and a more lateral thinking approach to problems and solutions. Finally, a warmer feeling for the customers once they know they have several channels of support.
How have you financed this development?
Jan Nottelmann: Until a few months ago all inventions and developments were done with our own resources. We have spent years investigating and developing this method and have filed a number of patents. In order to design a demonstrator and get it ready quickly we had to hire a small team of engineers. In tough competition with other technology start-ups we were lucky to secure a grant from the UK Government’s Technology Strategy Board that allowed us to open a small R&D and customer support centre in Berkshire in October 2013. With this financial support we managed to have the first version of our sensor-less power seat demonstrator up and running in November of 2013. The grant will allow us to further refine the technology and the demonstrator in 2014. And the partnership with Control Developments helps us to get products to the market within the same timescale.
How will this technology be commercialised?
Jan Nottelmann: We can offer diverse solutions. We offer technology licences to larger players in each market segment. We can offer hardware/software solutions to system integrators, and bespoke systems/solutions/products to customers who might want the technology, but may not have the resources to develop it. Other customers may prefer a combination of these offerings.
What stage are you now at? And what are your aims for 2014?