In this interview, Matthew Beecham talked with Jan Nottelmann, Chief Technical Officer, IDEAdvance Ltd about the company’s technology for sensorless motion detection, control and monitoring of DC motors.
just-auto: What is it?
Jan Nottelmann: Traditionally brush commutated DC (BDC) electric motors are used in automotive applications such as power windows and power seats with the motors controllers relying on feedback from motion sensors such as Hall elements or optical sensors in the motor control loop. Feedback from these sensors to the motor controller requires sensor wires and connectors.
DCM-MotionTechnology is a new sensor-less rotation Detection, Control and Monitoring method for BDC motors. With a modern luxury car typically containing 100 or more BDC motors, sensor-less rotation detection and control is very attractive since no sensors, sensor wires or connectors are needed, thus providing substantial cost saving and improved reliability in automotive BDC motor applications.
Who invented it?
DCM-MotionTechnology was invented by the two Danish inventors Mikkel Willadsen and Bo Fich. Working together for a number of years in developing a motion control system for office furniture they discovered that the voltage transients generated on the supply wires during rotation of the BDC electric motors they used could be extracted for position and rotation detection. Without traditional motion sensors it was now possible to provide sensor-less feedback control to obtain synchronous operation of several motors, a feature that is essential in electric height adjustable work desks. Having realised that the discovery was unique and could benefit a number of BDC motor applications in other industries such as automotive they applied for patents of the method. DCM-MotionTechnology is now patented all over the world. In 2010 the UK based IDEAdvance Ltd was founded to further develop and commercialise DCM-MotionTechnology.
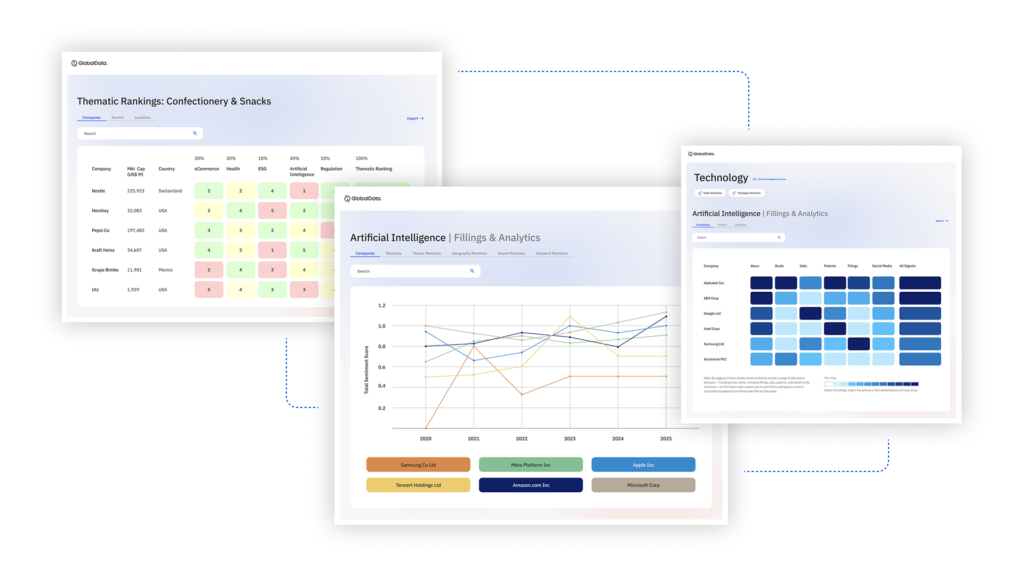
US Tariffs are shifting - will you react or anticipate?
Don’t let policy changes catch you off guard. Stay proactive with real-time data and expert analysis.
By GlobalDataWhat does it do and how does it work?
The DCM-TransientDetector is the basic element of DCM-MotionTechnology. It is a simple electronic filter circuit that detects the so-called kick-back voltage transients which are generated by any BDC motor every time a brush disengages with a commutator. The transients are generated as a result of the collapsing magnetic field whenever the power to a coil in the motor is instantaneously switched off (Lenz’s law). The detector also detects the lower amplitude negative voltage transients which are generated by the instant change of impedance when a brush either engages or disengages with a commutator (see fig. 1).
Each set of transients, what we call the transient fingerprint, represents an angular rotation of the motor with the angle depending on the actual motor configuration (the number of commutators and their positions in the motor), and can therefore be used to detect position and count motor commutations. When the number of commutations is known the actual position of the motor can be determined and the rotational speed can be derived by measuring the duration between each transient fingerprint. We call this Transient Counting.
Why is it useful?
The transients can be detected anywhere on the power supply wires to the motor and as such the technology can be fully integrated in most motor control system. We have verified that the transients can be detected on the power supply wires at least up to 20 metres from the motor generating the transients. So in a vehicle application it is now possible to measure the angular position inside the motor control unit where the information is required rather than relying on distant and often sensitive motion sensors located on or near the electric motor assembly, which is often located in a harsh environment.
As an example a power seat in a modern luxury car can include up to eleven electric motors and at least as many motion sensors. Each sensor typically requires 3-4 electric wires to power the sensor and to send the counting or position information back to the central power seat control unit where it is used in the motor control loop.
When using DCM-MotionTechnology in a power seat assembly no motion sensors, sensor/power wires and sensor wire connectors are required. The angular rotation of each motor is detected in the central power seat control unit where it is utilised in the feedback control loop for each motor. This not only saves cost, but it also reduces weight and improves durability since fewer components and wires are required in the power seat assembly and the power seat control system.
Why is it different and how is it significant?
Sensorless rotation detection for BDC motor systems has been known for some years. A method known as Ripple Counting has been used with some success in a limited number of automotive applications. Ripple Counting relies on measuring the changes in the back electromotive force (BEF) represented by the change in the current (the current ripples) to the motor as it rotates. Ripple Counting is however not a very reliable counting method since the current ripple waveform characteristics are highly dependent of a number of factors such as the supply voltage and the actual load, speed, direction, temperature and wear of the motor. Other factors such as the in-rush current (when the motor is started) and whether the motor rotates in a powered or unpowered mode (i.e. coasting in generator mode driven by the inertia of the load on the motor) also impacts the ripple waveform. Ripple Counting therefore requires quite sophisticated detection algorithms in the motor controller to generate more reliable counting signals.
Our tests have shown that Transient Counting is a very reliable counting method. The DCM-TransientDetector is a simple and inexpensive electrical circuit and the performance of the circuit is by and large unaffected by the parameters influencing Ripple Counting. Whether the motor is powered or unpowered has no influence on the counting and commutations can be reliably detected from start to stop of the motor, even in a worn motor. Further, the detector is almost totally unaffected by external interference.
What does it replace?
Due to the reliability of DCM-MotionTechnology we believe that sensor-less Transient Counting has great potential as a replacement for traditional sensor based position and rotation counting methods in a number of automotive BDC motor applications (ref. fig 2). Transient Counting has also shown superior performance over other sensor-less counting methods such as Ripple Counting.
Reliable position detection and counting is however not the only advantages of the method (ref. fig. 3) The precise physical detection of commutations per time unit enables advanced direction, speed and torque control of electric motors. With new tough safety requirements and improved comfort features being introduced in certain automotive applications such as power windows the movement of each motor can be controlled with higher precision enabling dynamic speed control and torque controlled anti-squeeze/anti-trap control.
In other automotive applications the use of DCM-MotionTechnology to accurately detect and control the angular rotation of an ordinary, inexpensive BDC motor can replace more expensive brushless DC motors, servo motors, stepper motors and precision actuators.
By introducing special algorithms in the motor controller the detected transient pattern can be continuously monitored and analysed. A changed transient shape or fingerprint pattern can reveal electric motor wear before it leads to malfunction or breakdown. This information can be used by car manufacturers to offer improved service & maintenance procedures for electric motor applications in cars.
Another exciting opportunity with the new technology is energy saving in BDC motor applications. This may not be so important in today’s cars powered by combustion engines, but mass produced electric cars will hit the roads soon, and the future owners of electric cars will expect to find the same electric applications and comfort features as they had in their petrol or diesel cars. But they don’t want these features to significantly drain the battery.
Our first experiments have shown that it is possible to improve the efficiency in BDC electric motors by around 15% by accurately controlling the power to the electric motor during each commutation, without compromising the output power of the motor. We call this DCM-SparkReduction. In simple terms the method works by reducing the power to the motor in the instant a brush leaves a commutator, thus reducing the arcing that is a known problem in every BDC motor. This not only reduces the power consumption of the motor, but it also reduces the EMC noise and significantly extends the lifetime of the motor, since the brushes will last much longer. The latter is potentially also interesting in petrol and diesel driven cars as it will improve the durability of the BDC motors used in the numerous electrical control and comfort systems in modern cars.
What does it threaten?
DCM-MotionTechnology’s sensor-less detection solution is a low cost alternative to sensor based rotation detection. The simple DCM-TransientDetector circuit can be easily integrated in the existing electric motor controller and in most cases only minor modifications to the controller software is required to obtain reliable positioning and motion control with the new method.
We know that most car manufacturers have considered adopting sensor-less detection in some of their BDC motor applications for several years, as they can save cost and obtain improved durability of their applications if they can avoid external sensors, sensor/power wires and connectors. The problem is that so far there hasn’t been a sensor-less detection method that could offer the detection reliability they require without using very complex detection algorithms. We believe DCM-MotionTechnology’s Transient Counting offers the simple and reliable sensor-less solution they have been looking for. This is why we have started discussions with the automotive industry and we have already received very positive responses from several manufacturers.
When will it appear and who will want it?
In IDEAdvance we have spent most of our time up to now developing and refining DCM-MotionTechnology and to secure the intellectual property of the method. So we haven’t really been ready and able to talk much about it until now.
As mentioned we are in discussions with a number of automotive suppliers. The automotive industry is certainly the most important for us, and we are very interested in meeting even more potential adopters and customers in the automotive segment to discuss the advantages of DCM-MotionTechnology.
We are aware that the lead time for new and innovative technical solutions to appear in production cars is usually quite long. One of the main advantages of our sensor-less detection method is that it is simple and quick to integrate in existing motor controllers, so it may not take that long for DCM-MotionTechnology to appear in a new car model. We are also in discussions with a number of suppliers in other industries using BDC electric motors, such as the process industry and manufacturers of power tools, consumer electronics, precision instruments, toys and models. With several billion small BDC electric motors being supplied to the world market every year and most of them requiring some form of motion feedback system the opportunities for DCM-MotionTechnology are almost unlimited.