Continuing just-auto’s series of interviews with major tyre makers, Matthew Beecham talked with Kate Rock, customer and brand public relations and James Bailey, director, brand public relations, Goodyear Dunlop Europe about the use of winter tyres, tyre labelling and runflat tyres.
There has been much talk in the UK recently about standardising tyre fitting to suit seasonal conditions despite our relatively benign climate. Do you think winter/summer tyre fitting should be standard across the EU?
Goodyear Dunlop believes that tyres should be fitted in line with the temperature. Winter tyres work better in temperatures below 7 degrees C, we have, on average, over 150 days between October and March under this temperature. This is almost half the year. Summer tyres do not offer enhanced grip in cold conditions but low temperatures will also hinder their mileage performance. By fitting a winter tyre in winter and a summer tyre in summer you will get the best performance from your rubber all year round.
For those occasions when we do get snow and slush in the UK, winter tyres enable motorists to drive as normal and still get from A to B without any stress or hassle. Summer tyres do not offer this security and peace of mind.
Winter tyre sales have more than trebled in the UK in the last three years, but still represent a tiny fraction of the overall market. Growing winter tyre usage, which will be a significant contributor to improved winter safety and mobility, is dependent on increased awareness of the benefits.
Tyre labelling is set to become a reality. What’s your view on what it will mean for the consumer?
How well do you really know your competitors?
Access the most comprehensive Company Profiles on the market, powered by GlobalData. Save hours of research. Gain competitive edge.
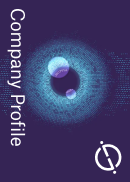
Thank you!
Your download email will arrive shortly
Not ready to buy yet? Download a free sample
We are confident about the unique quality of our Company Profiles. However, we want you to make the most beneficial decision for your business, so we offer a free sample that you can download by submitting the below form
By GlobalDataThe Tyre Label will give the customer an informed view on what they are purchasing but what the customer needs to remember is that the label only looks at three parameters of the tyre. They need to think about the performance of a tyre in three different ways; three tests on the tyre label, up to 15 tests carried out in magazine tests and up to 50 tests are done by the tyre manufacturer. A tyre is not as simple as 1,2,3 and a motorist needs to know what they want out of their tyre before purchasing.
To what extent has the tyre labelling legislation given Goodyear the chance to further innovate and differentiate itself from the competition?
The challenge for Goodyear Dunlop is to produce an A rated tyre which still performs well in all the other test criteria. Some manufacturers may be able to create an A rated tyre but they may sacrifice other performance criteria such as mileage or dry grip. Goodyear Dunlop will not do this and the challenge is to produce tyres across the range that offers these levels of performance.
The OEMs are under the pressure of new regulations for environment and safety. To what extent does that in turn put pressure on Goodyear to develop outstanding products that can match these challenging performance levels, e.g. for rolling resistance?
We thoroughly enjoy working with OEMs as they give us true challenges and parameters to work within. It is always of optimal importance to produce the best possible product for every OEM and we work over the space of five to six years when developing a new tyre for fitment on a new vehicle. It is by working with OEMs that we can be truly market-back with our innovation.
A number of other tyre regulations are being rolled out in Europe, including those relating to rolling resistance, tighter controls on chemical substances, noise emissions and wet grip. Is there too much regulation? What’s your view?
Regulation is there for a reason and this is why we work closely with the government and the EU to ensure that the regulations that they put in place are worthy and useful to the tyre industry.
I guess that TPMS and run-flat tyres will play a part in accelerating the removal of the spare tyre. What’s your view?
We are very proud of our RunOnFlat technology and the development that has gone/goes into it. TPMS and RunOnFlat are closely linked, both offer safety credentials for the motorist. OEMs are looking at ways of saving weight within their vehicles and eradicating the spare wheel is a massive contributor to this. We will, of course, work with OEMs during the mandatory introduction of TPMS across all new vehicle platforms as well as work with them to integrate RunOnFlat tyres across their ranges.
In terms of comfort, how do the latest generation of run-flats compare with conventional tyres?
The next generation of RunOnFlat Technology shows no difference in comfort, and this without any compromise on the tyre’s overall performance and RunOnFlat capability. Specific compounds with new formulations and construction improvements with new materials and a new internal tire structure have led to this high level of comfort.
Our latest generation RunOnFlat tyres have a range of features that enhance performance. For example, a new rayon ply structure gives optimised usage of the ply reinforcement in both inflated and deflated conditions leading to better comfort and rolling resistance. Also, a new compression resistant component in the bead area reinforces the lower sidewall reinforcement giving optimum dry handling and enhanced runflat mileage. To address rolling resistance, we developed special low rolling resistance technologies providing rolling resistance levels better than many standard tyres. For example, the Eagle F1 Asymmetric RunOnFlat tire for the Mercedes E-Class has the same rolling resistance level as the Mercedes E-Class approved standard Goodyear tyre and is better than competitor tyres approved on Mercedes E-Class.
How do you see the roll out of the run-flats amongst car segments?
The roll out of RunOnFlat will take its time to integrate across all car segments and we do not foresee this happening for a number of years.
People talk of the intelligent tyre as vehicles change. With newer forms of propulsion, in what ways will the tyre change and adapt to such technology?
We continue to work with OEMs to develop tyres in line with their hybrid and electric vehicles and we already have a strong partnership with Renault on this topic.
We also continue to look at new ways of producing tyres and the raw materials that we use. Recent developments include the use of Soy Bean and BioIsoprene in tyre manufacture.
Goodyear researchers have found in their tests that using soybean oil in tyres can potentially increase tread life by 10 percent and reduce the tyremaker’s use of petroleum-based oil by up to seven million gallons each year.
In addition, testing at Goodyear’s tyre plant in Lawton, Oklahoma showed improved mixing capabilities in the manufacturing process. The company found that rubber compounds made with soybean oil blend more easily with the silica used in building tyres. This can improve plant efficiency and reduce energy consumption and greenhouse gas emissions.
Goodyear has produced a concept tyre with BioIsoprene technology which represents a breakthrough alternative to a petrochemically produced ingredient in the manufacture of synthetic rubber with renewable biomass. The tyres made with BioNatsyn polymer which is made from BioIsoprene product, are the result of a collaboration between Genencor, a division of Danisco, and Goodyear.
BioIsoprene product is derived from renewable raw materials, and represents a significant development within the biochemical and rubber industries. Aside from synthetic rubber for tyre production, traditional isoprene is used for the production of a wide range of products, such as surgical gloves, golf balls and adhesives. Thus, the potential for BioIsoprene product is substantial.
Finally, reducing road noise from tyres has been the subject of intense research over the years. With the gradual introduction of EVs, I guess the challenge for the tyre industry is to design a tyre that produces a comfortable level of noise for the environment without having a negative effect on the interior vehicle noise. What’s your view?
Noise is a very important part of a tyre’s design and we continually invest in research and development to improve the noise level of our tyres. As previously stated we test over 50 different parameters of a tyre before taking it to market and one of the key tests is noise, both internal and external, we would never trade one over the other.
We continue to work on EVs with OEMs and of course this is one of the key challenges for us as tyre manufacturers.