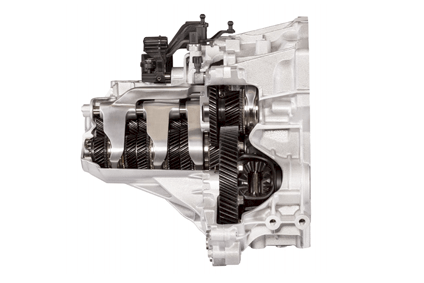
At the 2015 IAA, Calum MacRae spoke with Christof Schulte, Senior Product Development Manager manual transmissions, GETRAG FORD Transmissions GmbH, Germany. MX65 – in three variants 5MTT152, 5MTT215 and 6MTT215 – is the replacement for Ford's venerable iB5 transmission (alternatively known as 5MTT170) and will be produced in four global locations.
Firstly, Christof what does your role involve on a day-to-day basis?
I’m responsible for the product development for Getrag in Cologne of the small manual transmissions. So for the products currently in production I’m responsible for the iB5 globally and we’re now focusing on the replacement of this old architecture because we’re now at the point where we can’t improve customer satisfaction any more without spending a lot of money. The architecture of the iB5 dates back to 1973: it started as a four-speed transmission then went over to five-speeds with an add-on unit. Now in the B-segment we see increasing demand for six-speeds in Europe, North America and China mainly.
Additionally, the iB5 was engineered with a non-synchronised reverse gear, which drives some customers to complain about reverse shiftability, which is not avoidable with such a design architecture.
Therefore, for the past four years we have been thinking about how we can replace this transmission on a global scale as also in scope for the project is the initiation of a new GFT manufacturing location in Sanand, India. Currently, the iB5 for India is made by a Ford contractor (AVTEC) so we only do the engineering service in India.
From a UK perspective, where does the MX65 development leave the Halewood plant?
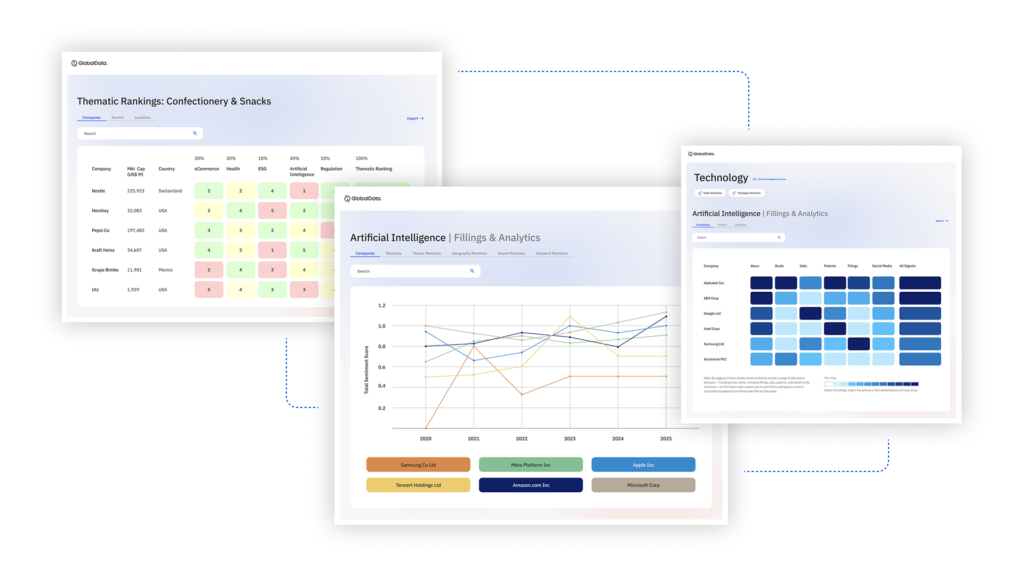
US Tariffs are shifting - will you react or anticipate?
Don’t let policy changes catch you off guard. Stay proactive with real-time data and expert analysis.
By GlobalDataHalewood still has the B6 transmission after moving already from iB5 to the slightly higher torque segment (the 250Nm 6MTT250). Bordeaux will now pick up the lower torque segment with the MX65 so the UK is unaffected. Incidentally, we have a successor to the B6 here at the IAA in the form of the 350Nm torque capacity 6MTT331, which will launch around 2017.
Which plants are building the new MX65 globally?
Three GFT plants at Bordeaux, France; Sanand, India and Ganzhou, China (which has built the iB5 since 2007) plus the Ford transmission plant at Taubate, Brazil.
So a big program globally and what sort of volumes are we looking at?
At the moment we are at about 1.6 million but we see good opportunity, and only within the Ford community, to increase to 2 million. Additionally, because this is a new product we think that third party customer business is within scope too. With iB5 that was never the case as all the other OEMs had the same 5-speed architecture so there was no opportunity. It will exclusively be for Ford in the first year but after that we can look to third party sales.
What sort of design input did Ford have in the new transmission?
We get a group of requirements from them. The design itself, if you want it’s a black box for Ford; they could totally specify and design the attributes but in reality – partly because they’re 50% shareholders in GFT – we work together to get the best design for the market.
The MX65 looks like a very ordinary and typical transmission, but it isn’t. It’s a 5-speed transmission for India and to get that transmission in to the Indian market you need to invest in the product to get it on the market to an acceptable price. In Europe, the transmission will not be more expensive than the one it replaces.
And there are some quality features we have designed on top, like synchronized reverse gear. This is a feature we thought long and hard about – OK, there were some customer complaints over shiftability for reverse gear but actually the number was very, very minor – so we weren’t sure whether to invest in the feature at the beginning or not. Finally, we decided that for quality we should add the feature globally.
The prime development purpose for this transmission was to have “plug and play” capability so it could replace iB5 without any modification to existing drivetrains. That was especially tough because the iB5 does not have a dual-mass flywheel (DMF) – so there's not any NVH damping between engine output and the drivetrain – and when you increase to six-forward gears and one-reverse, you have much more opportunity for gear rattle and chatter. But MX65 has to do without a DMF too, to keep the desired "plug and play" attribute and a DMF would have added about US$70 to the cost, which is not desirable in the small car segment where margins are so thin.
So is there any on-cost for Ford for the MX65?
In some areas yes, but largely it’s cost neutral at least in Europe. That was very important for us as Ford only goes with GFT if the business case makes sense.
So what makes the transmission cost-neutral? Is it the scale of the manufacturing?
We took a bit more time than usual and we always started with the simplest, cheapest and easiest solution. If engineers are designing something they typically want to design the optimum solution. It’s extremely difficult to tell engineers that you don’t want them to design the best they can and that you want them to design to target. We knew that it would be difficult, so we started earlier and allowed some time to fail. Only if you fail and improve your design to target can you then know that you’ve not spent a single cent more than is necessary. All areas were designed to target and not above and that was done working with Ford very, very closely. It needed compromise over attributes and adherence to design to target. If we saw that some targets at the system level were too much we took the cost savings gained and directed the money elsewhere, but whatever we did it couldn’t increase the price of the transmission.
Were there any best-in-class attribute targets for the MX65?
On shift quality yes. You can’t compromise shiftability. Shift quality is the only connection the customer has with the transmission – so don’t compromise that.
Actually, we’re just thinking about making the shift quality even better because the target was somewhere between the old iB5 and not as good as B6 on the global scale. As you know there are regional preferences so we might do a little bit more with shift quality for the European market and get it nearer B6 levels.
We can do that because we have designed scalable solutions at any synchronizer position in the transmission. You can have triple-cone synchronizers, double-cone synchronizers or single-cone synchronizers depending on cost and function requirements, and these are things we can play around with by market. For example, in India shift quality is not so important now, but in five years’ time, who knows? At the moment, we’re looking to reduce some of the attributes for India to take some more cost out, but we need to be prepared to recontent if the market develops to a higher requirement.
As well as synchronizers, MX65 is scalable on the internal controls and on the sealing concepts. With sealing, for example, in some markets – Poland, Switzerland and Russia – the differential seals are critical because they use very aggressive salt on the roads in winter that can cause big problems. So for those markets we have to spend a few dollars more.
So scalability really helps us to get to the sweet spot in each market, and that experience has developed out of all the knowledge the iB5 team has built up of markets over the years.
Is it quite difficult to get a voice within GETRAG for manual transmissions when a lot of the focus is on the DCT portfolio?
No. We work closely together with the Powershift team – actually, MX65 shares some components with Powershift, at least those we can afford for our small manual. There is a big share of manual transmissions in the company. In Cologne, Ford is one of our big manual transmission customers. Also, at our Untergruppenbach HQ, we have our standard manual customers such as BMW and MINI. So it is a settled business. But the growth of course is with Powershift.
However, in the long-run the manual transmission will remain a substantial part of the global market at 50-60% share.
Look around at cost-sensitive markets such as India. There the OEMs are launching models with AMT like crazy. That’s a technology that we thought was dead apart from a few niche applications. Suddenly the technology comes back and catches everybody by surprise.
Do you have any plans for an AMT for the Indian market?
Yes, we kicked off a project five months ago and we will be ready to launch an AMT transmission derived from the MX65 around 2019.
And the clutch actuation technology – is it yours or Marelli’s or Valeo’s for example?
That’s not finally decided as we are talking to a number of different suppliers, but it will be a bolt-on solution.
What is the on-cost for an AMT?
I don’t know yet as we haven’t costed everything through. If you look at it from an affordable business perspective, you can buy a CVT for a small petrol engine for EUR800-900 and the AMT needs to be below that.
So I’d guess that for an Indian market five-speed manual transmission you would be looking at a cost of EUR300-400?
That’s too much. You have to be below that as competition in India is really tough. For the AMT bolt-on we have a target but we haven’t worked through the costs yet.
Finally, what do you think the optimum number of forward gears will be in the future?
That’s difficult to say. For me with manuals – besides some niche markets such as muscle cars and light trucks where seven makes sense – the limit is at six I would say. If you had to operate more than that manually the customer perception would not be very good. If you look at the auto market on a pure CO2 requirement basis then somewhere between six and seven is the optimum and anything else is public relations and politics.